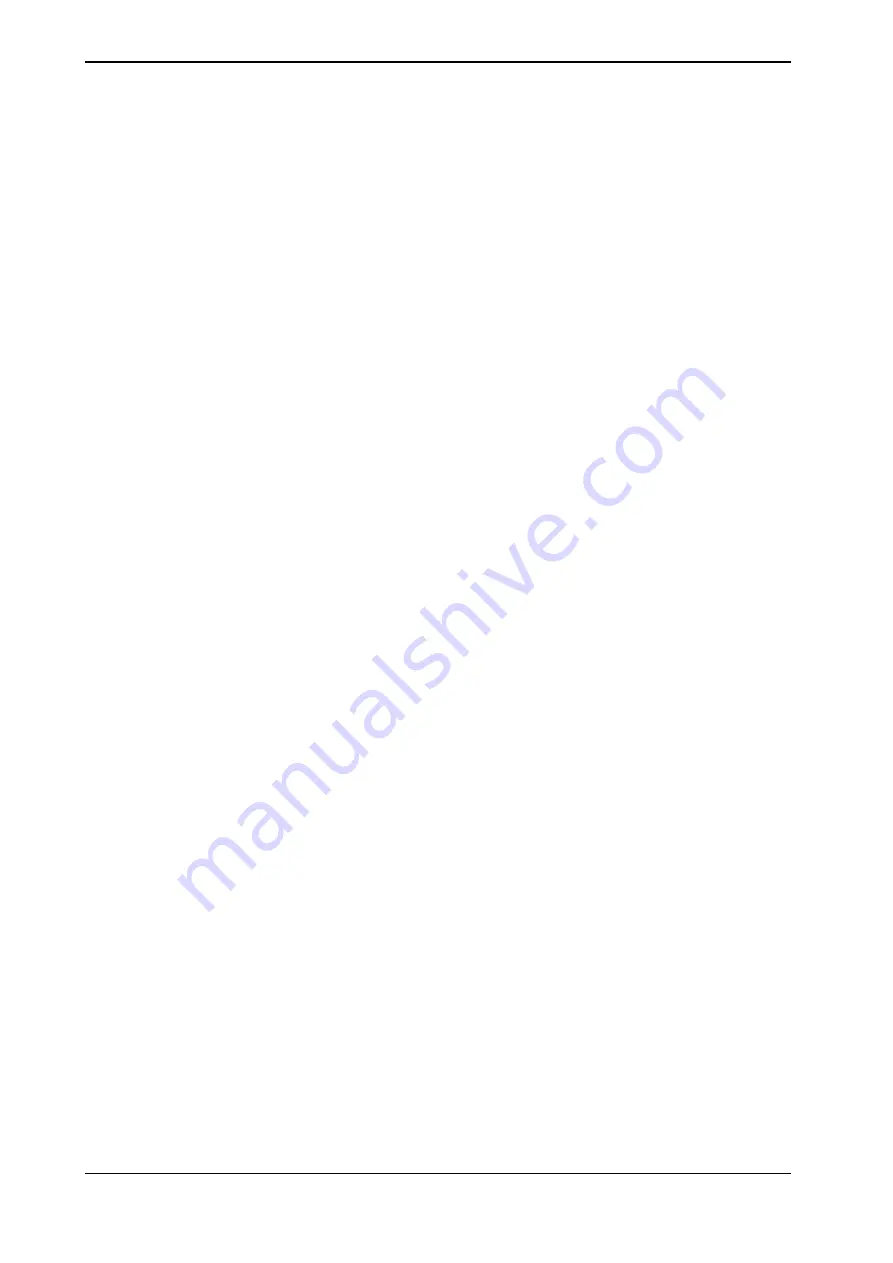
SafetyControllerSyncRequest, 195
safety controller version, 192
Safety module, 57
safety users, 141
save configuration, 170
Servo Delay Factor, 208
servo lag, 39, 55
Servo Lag, 208
servo tool changer, 30
servo welding gun, 29
shared drive modules, 30
signals for Cyclic Brake Check, 204
soft servo, 39
software synchronization
description, 41
SST, 33, 46
stand alone controller, 30
Stand Still Supervision, 33, 46
description, 46
stopping time, 189
supervision functions, 35, 46
supported cabinets, 27
supported positioners, 29
supported robots, 27
supported tracks, 28
synchronization
description, 41
guidelines, 197
sync position, 42, 197, 199
sync switch, 58
system integrator requirements, 15
system parameters changed, 192
T
tool, 199
tool changer, 30
tool coordinate system changed, 192
Tool Orientation Supervision, 33, 54
description, 54
Tool Position Supervision, 33, 53
description, 53
Tool Speed Supervision, 33, 49
description, 49
TOR, 33, 54
TPO, 33, 53
TSP, 33, 49
U
UAS grants, 141
unsynchronized state, 191
user interface
FlexPendant, 113
V
validated configuration file, 184
violation signal, 35, 85, 189
virtual signals for brake check, 204
Visual SafeMove, 73
W
work area for additional axes, 29
world coordinate system changed, 192
write configuration, 171
236
Application manual - Functional safety and SafeMove2
3HAC052610-001 Revision: P
© Copyright 2016-2020 ABB. All rights reserved.
Index
Summary of Contents for SafeMove2
Page 1: ...ROBOTICS Application manual Functional safety and SafeMove2 ...
Page 8: ...This page is intentionally left blank ...
Page 16: ...This page is intentionally left blank ...
Page 34: ...This page is intentionally left blank ...
Page 56: ...This page is intentionally left blank ...
Page 72: ...This page is intentionally left blank ...
Page 112: ...This page is intentionally left blank ...
Page 194: ...This page is intentionally left blank ...
Page 196: ...This page is intentionally left blank ...
Page 234: ...This page is intentionally left blank ...
Page 237: ......