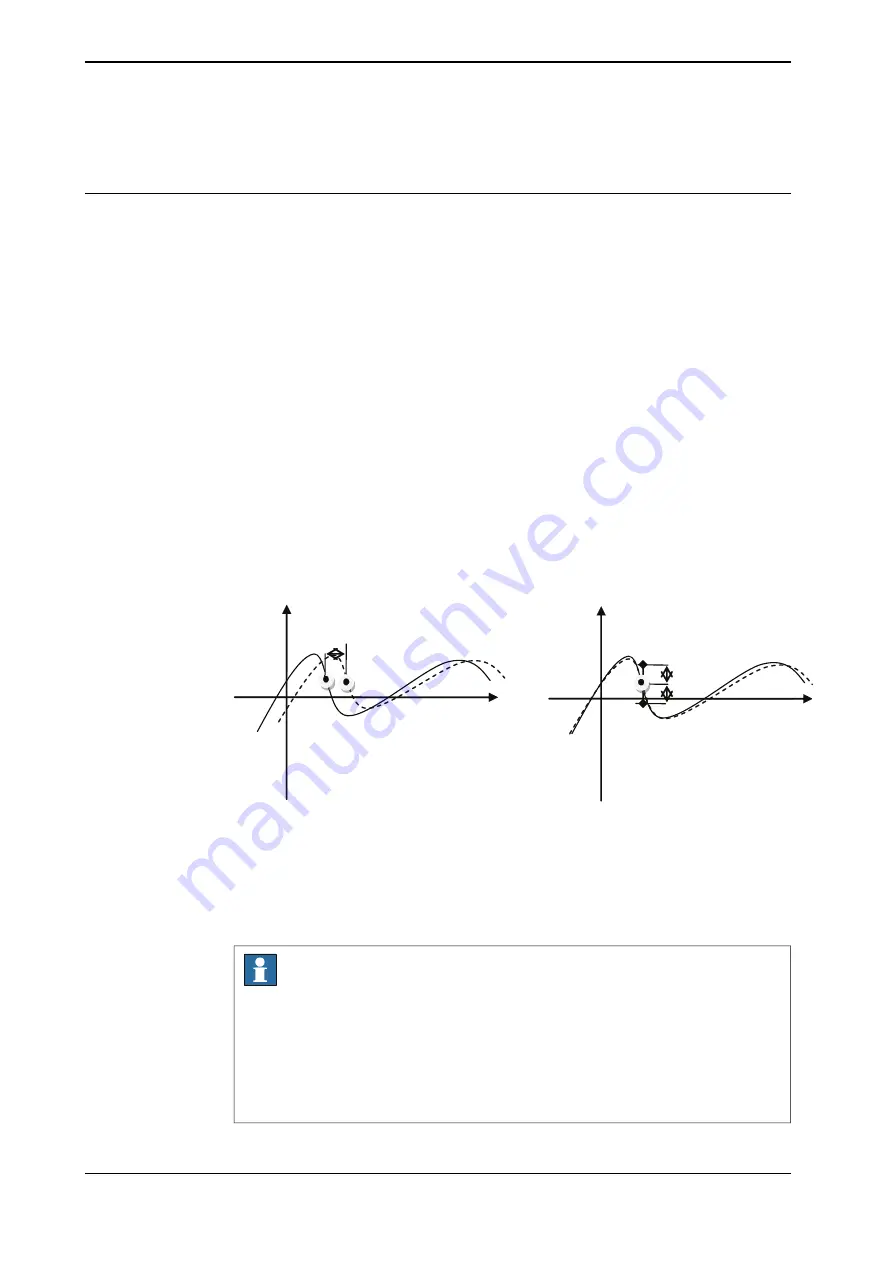
10.3 Servo Delay Factor and Servo Lag
System parameters Servo Delay Factor and Servo Lag
To explain what is affected by the parameters
Servo Delay Factor
and
Servo Lag
in the SafeMove configuration (see
Configure additional axes on page 147
) it is best
to consider an example.
In graph (a) in the figure below, the
Servo Delay Time
is illustrated using a
constructed example where a reference and a corresponding measured angular
motor position is shown. The corresponding
Servo Delay Factor
can be computed
using:
Servo Delay Factor = Servo Delay Time / 4
In graph (b) in the figure below, the
Servo Lag
parameter is illustrated when the
measured signal is shifted with the
Servo Delay Time
. The measured position
should now be within a distance of +/-
Servo Lag
from the reference at every time
instance. If the measured position is outside the specified region the SafeMove
position supervision is triggered.
me
angle
S
e
rv
o
D
e
la
y
T
im
e
angle
me
Servo Lag
(a)
(b)
en1100000626
Figure 10.1: Illustration of Servo Delay Time (a) and Servo Lag (b). Solid line is motor angular position
reference (test signal 17) and dashed is the corresponding measured motor angular position (test signal
18). In (b) the measured motor angular position signal is shifted Servo Delay Time in order to illustrate
that it is the time shifted signal (samples) that should lie /- Servo Lag radians from the reference.
Note
The signals in the figure are only for illustrative purpose. The
Servo Delay Time
in a real system is small, typically in the range 12-16 ms, which means a
Servo
Delay Factor
in the range 3-4. If the
Servo Delay Factor
is incorrect the
Servo
Lag
has to compensate this since the difference between reference and measured
motor angular position will be large when the axis accelerates, runs at high speed,
or decelerates.
Continues on next page
208
Application manual - Functional safety and SafeMove2
3HAC052610-001 Revision: P
© Copyright 2016-2020 ABB. All rights reserved.
10 Reference information
10.3 Servo Delay Factor and Servo Lag
Summary of Contents for SafeMove2
Page 1: ...ROBOTICS Application manual Functional safety and SafeMove2 ...
Page 8: ...This page is intentionally left blank ...
Page 16: ...This page is intentionally left blank ...
Page 34: ...This page is intentionally left blank ...
Page 56: ...This page is intentionally left blank ...
Page 72: ...This page is intentionally left blank ...
Page 112: ...This page is intentionally left blank ...
Page 194: ...This page is intentionally left blank ...
Page 196: ...This page is intentionally left blank ...
Page 234: ...This page is intentionally left blank ...
Page 237: ......