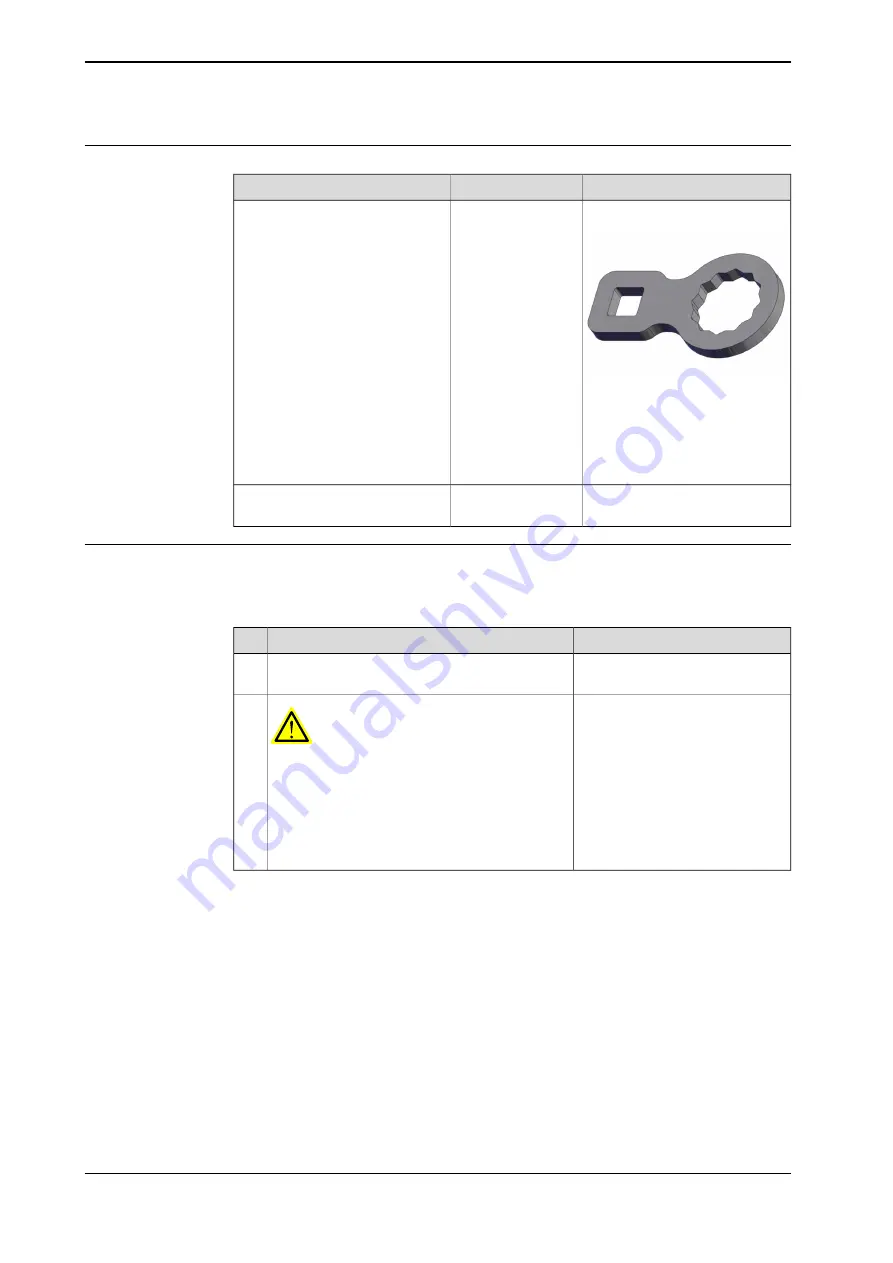
Required tools and equipment
Note
Article number
Equipment
Included in robot delivery.
xx2000000282
Used with a torque wrench (not
included in delivery) to loosen
and tighten the universal joint and
telescopic shaft screws.
Hole interface: 1/4" square.
3HAC063379-001
Torque wrench head, closed end
Content is defined in section
.
-
Standard toolkit
Removing the cable harness
Use these procedures to remove the cable harness.
Preparations before removing the cable harness
Note
Action
This is done to facilitate updating
of the revolution counter.
Jog the robot to calibration position.
1
DANGER
Turn off all:
•
electric power supply
•
hydraulic pressure supply
•
air pressure supply
to the robot, before entering the safeguarded
space.
2
Continues on next page
170
Product manual - IRB 390
3HAC066566-001 Revision: B
© Copyright 2020 - 2021 ABB. All rights reserved.
5 Repair
5.4.4 Replacing the cable harness
Continued
Summary of Contents for IRB 390
Page 1: ...ROBOTICS Product manual IRB 390 ...
Page 8: ...This page is intentionally left blank ...
Page 14: ...This page is intentionally left blank ...
Page 36: ...This page is intentionally left blank ...
Page 44: ...This page is intentionally left blank ...
Page 118: ...This page is intentionally left blank ...
Page 330: ...This page is intentionally left blank ...
Page 344: ......
Page 345: ......