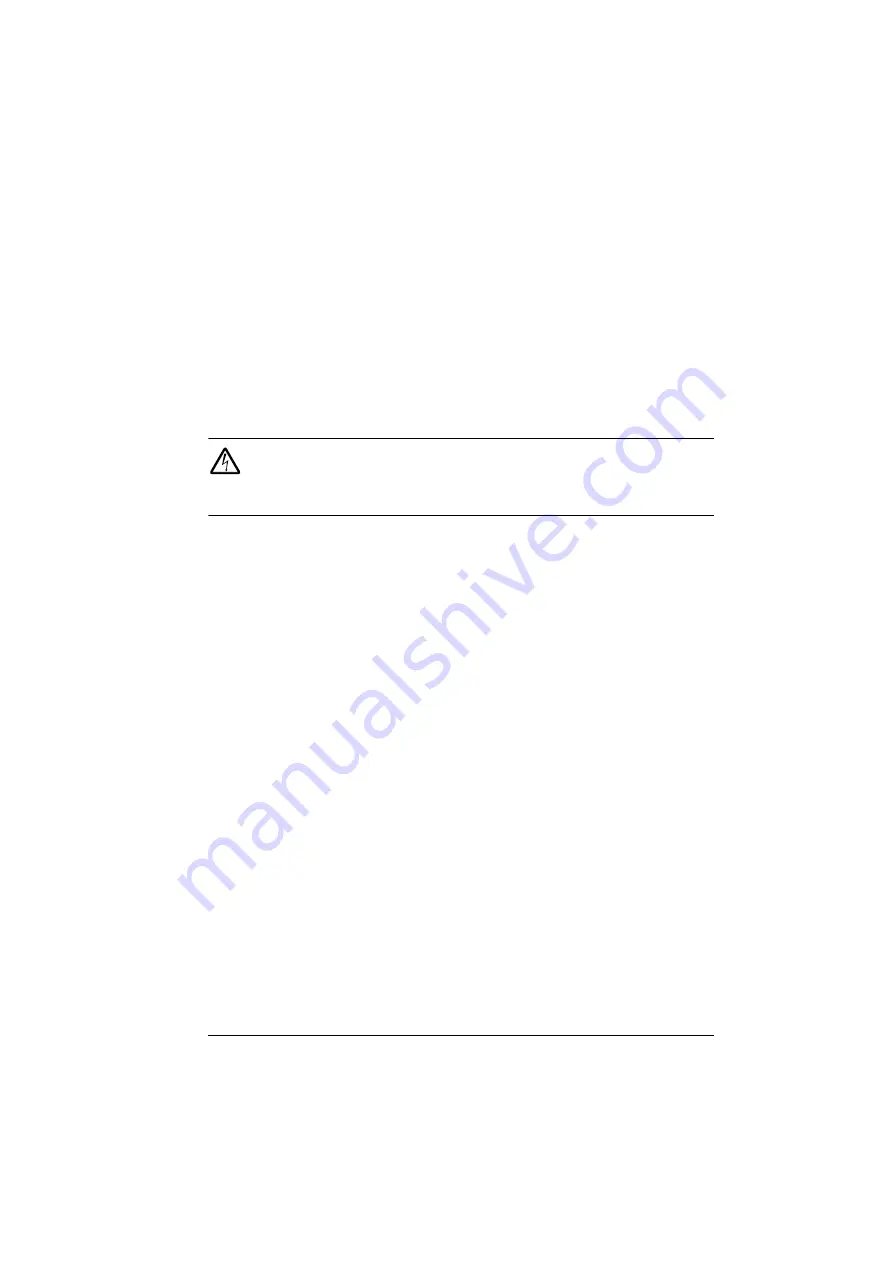
Program features 59
). After this, when power is applied to the drive, the motor is
assumed to be at the estimated temperature.
2. Motor temperature is calculated using the user-adjustable motor thermal
time and motor load curve. The load curve should be adjusted in case the
ambient temperature exceeds 30
°
C.
3. The motor thermal model can be used only when one motor is connected to
the drive.
Insulation
WARNING!
IEC 60664 requires double or reinforced insulation between
live parts and the surface of accessible parts of electrical equipment
which are either non-conductive or conductive but not connected to the
protective earth.
To fulfil this requirement, connect a thermistor to the drive’s control terminals
using any of these alternatives:
• Separate the thermistor from live parts of the motor with double reinforced
insulation.
• Protect all circuits connected to the drive’s digital and analog inputs. Protect
against contact, and insulate from other low voltage circuits with basic
insulation (rated for the same voltage level as the drive’s main circuit).
Use an external thermistor relay. The relay insulation must be rated for the
same voltage level as the drive’s main circuit
Temperature monitoring using thermistor relays
A normally closed or a normally open thermistor relay can be connected to
digital input DI6.
Summary of Contents for ACQ80
Page 1: ... ABB DRIVES FOR WATER ACQ80 standard program control Firmware manual ...
Page 2: ... Related documents are listed on page 13 ...
Page 4: ......
Page 10: ...10 Table of contents ...
Page 32: ...32 Startup control with I O and ID run ...
Page 34: ...34 Using the control panel ...
Page 74: ...74 Program features ...
Page 78: ...78 Control macros ...
Page 380: ...380 Fieldbus control through a fieldbus adapter ...
Page 384: ...384 Parameterization with Drive Composer ...
Page 388: ...388 Parameterization with Automation builder drive manager ...