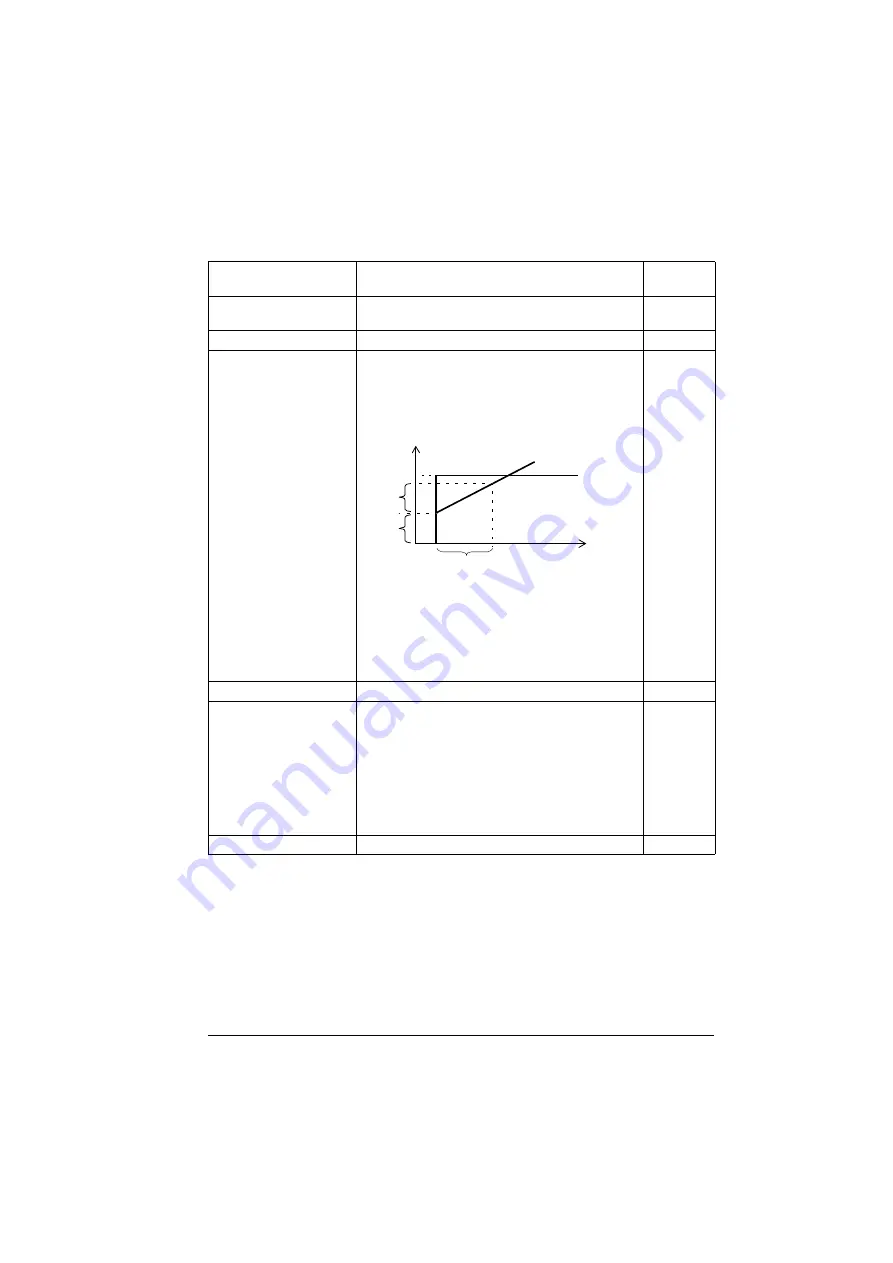
Parameters 195
Defines the gain for the process PID controller.
See parameter
1.00
0.01…100.00
Gain for PID controller.
100 = 1
Defines the integration time for the process PID
controller. This time needs to be set to the same
order of magnitude as the reaction time of the
process being controlled, otherwise instability
will result.
Note:
Setting this value to 0 disables the “I” part,
turning the PID controller into a PD controller.
60.0 s
0.0…9999.0 s
Integration time.
1 = 1 s
Defines the derivation time of the process PID
controller. The derivative component at the
controller output is calculated on basis of two
consecutive error values (E
K-1
and E
K
) according
to the following formula:
PID DERIV TIME × (E
K
- E
K-1
)/
T
S
, in which
T
S
= 2 ms sample time
E = Error = Process reference - process feedback.
0.000 s
0.000…10.000 s Derivation time.
1000 = 1 s
No.
Name/Value
Description
Def/
FbEq16
Ti
O
I
G × I
G × I
I = controller input (error)
O = controller output
G = gain
Ti = integration time
Time
Error/Controller output
Summary of Contents for ACQ80
Page 1: ... ABB DRIVES FOR WATER ACQ80 standard program control Firmware manual ...
Page 2: ... Related documents are listed on page 13 ...
Page 4: ......
Page 10: ...10 Table of contents ...
Page 32: ...32 Startup control with I O and ID run ...
Page 34: ...34 Using the control panel ...
Page 74: ...74 Program features ...
Page 78: ...78 Control macros ...
Page 380: ...380 Fieldbus control through a fieldbus adapter ...
Page 384: ...384 Parameterization with Drive Composer ...
Page 388: ...388 Parameterization with Automation builder drive manager ...