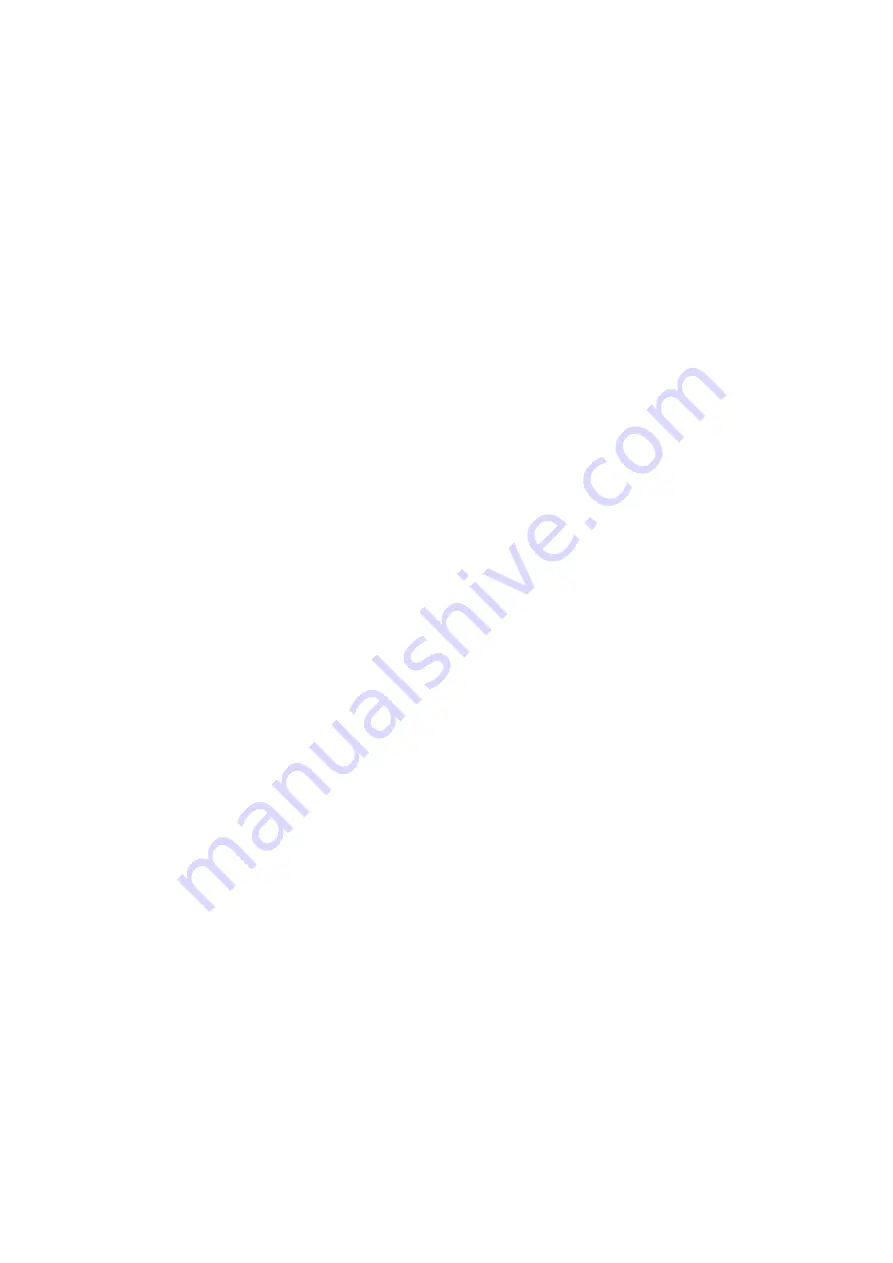
62
26, then back off by 1/6-1/4 a turn. The sealant squeezing-out into the gap between
the end faces of the walking-beam nut and bushing is not allowed. Upon adjustment
torque coupling bolt 18 to 44-56 N m (4.4-5.6 kgf m). Replace the damaged cap
gasket having lubricated it on either side with
УН
-25 sealant (alternatively with
Loktite-573).
Fill lubricant into the walking-beam hubs up to the filling hole level available
in the cap. Eliminate lowering of oil level below the mark available on the walking-
beam caps.
As the oil filled into the walking-beam hubs when reassembling gradually packs
the gaps in joints and is absorbed by the wooden plugs, which are pressed into the
axle pipe on both sides, an insignificant lowering of oil level is possible.
When preparing a new truck for operation check lubricant level in the walking-
beam hubs and bring it up to the filling hole level in the caps, if need be.
Torque the torque rod pin nuts to 600 N m (60 kgf m). If the cotter pin holes fail
to match with nut slots, tighten up the nut into coincidence and cotter it. Pack grease
into the torque rod hinges until fresh grease is squeezed out, or the rubber packing
rings begin to be deformed. In this case the grease needs not be squeezed out.
Loosing of bolt connections of suspension parts is not allowed.
If working fluid leaks out of the shock absorber, tighten up nut 2 (see Fig. 46).
The shock absorber should exhibit uniform resistance being expanded or compressed.
The rebound effort must be within 5.9-8.0 kN (595-800 kgf), while the compression
effort, 1.5-2.2 kN (152-228 kgf). For effort testing use the press with a rod stroke of
100 mm and a speed of 100 strokes per minute. If the shock absorber rod travels
freely, it indicates that the unit is faulty.
The shock absorber should be disassembled and reassembled in workshops
keeping required cleanliness. Polished surfaces of the rod, operation cylinder,
compression rings and piston should be protected from dents and other injuries.
When changing the working fluid, proceede as follows:
1.
Clamp the shock absorber in the vice by its lower head and pull out the rod
completely.
2.
Fit a special wrench in a slit formed between the casing and body and
unscrew the body nut.
3. Slightly rocking the rod at its upper end, take it in assembly with the
piston out of the operation cylinder.
4. Take the operation cylinder out of the container and drain the working
fluid completely.
Every time, when disassembling and also when replacing the fluid, wash all the
parts of the shock absorber in kerosene and dry them. Lubricate the collar inner faces
with shock absorber fluid in accordance with the Lubrication Chart. If the fluid is
unsufficient the shock absorber is not capable of exerting force, if excessive, it may
break down. It is not permitted to use other fluids as shock absorber ones. Insert the
piston in assembly with rod into the cylinder, fit the gland housing, packing ring,
washer, move all other parts and torque the body nut to 120-150 N m (12-15 kgf m).
On the shock absorber with a plastic casing being extended the access to the
body nut is cut off. To tighten up the body nut remove the shock absorber from the
truck and thrusting against the casing end press the latter off to the upper head’s
side. Having tighten up the body nut reset the casing on its original place.
Содержание 4320-10
Страница 1: ...URAL 4320 10 URAL 4320 31 TRUCKS AND THEIR MODIFICATIONS ...
Страница 180: ...179 Fig 119 Truck Lubrication Diagram ...