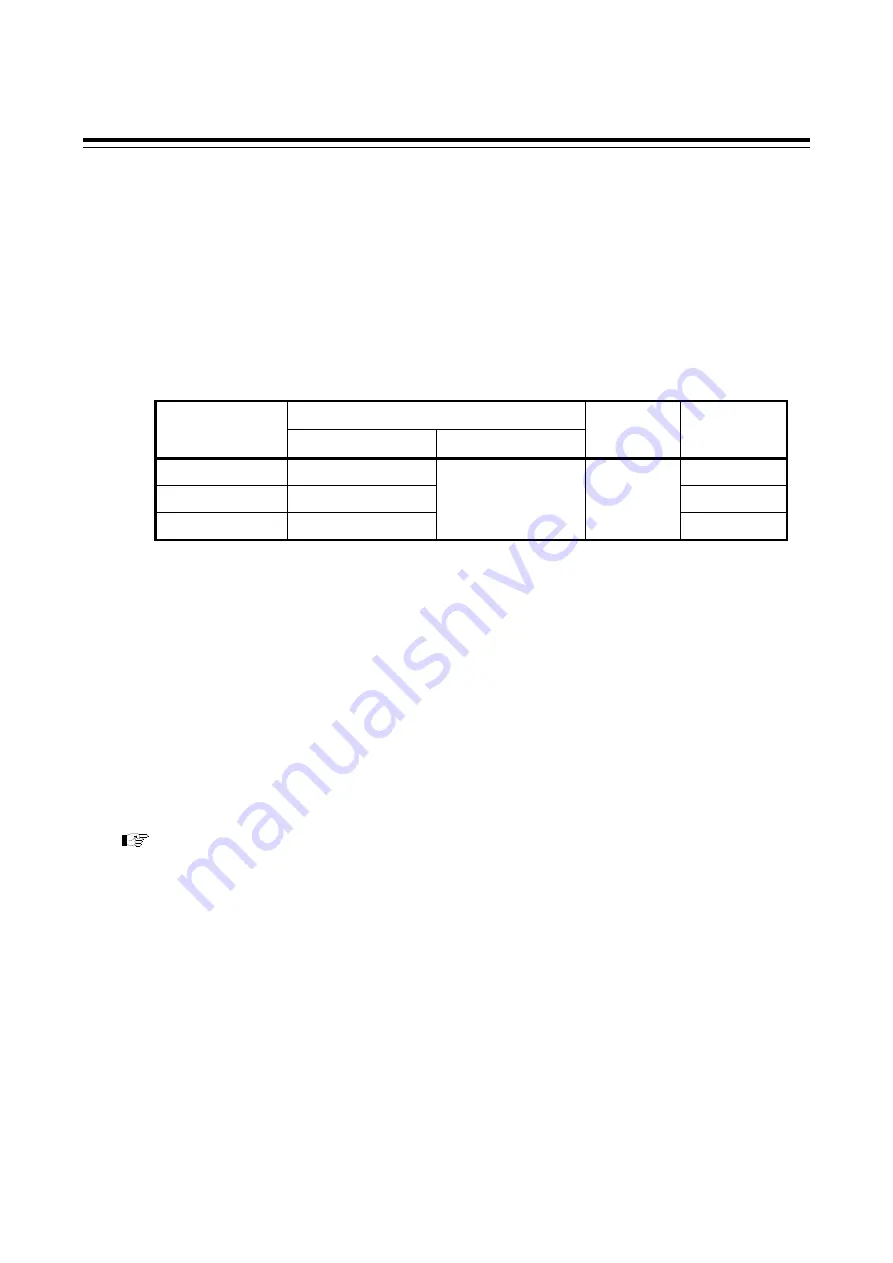
100
IMR01Y36-E2
10. SPECIFICATIONS
DeviceNet communication
Protocol:
DeviceNet
Supported connection:
Polling I/O, Explicit message
Connection method:
Multi-drop connection, T-branch connection
(Terminating resistor is necessary)
Communication speed:
125 kbps, 250 kbps, 500 kbps
(Communication speed can be selected with switch)
Factory set value: 125 kbps
Communication length:
* The maximum of length between nodes
Maximum number of connection nodes:
64 (including master)
Error control:
CRC error, Node address (MAC ID) duplication check
Conforms to DeviceNet specification:
Volume
I
−
Release2.0
Volume
II
−
Release2.0
Device profile name:
Generic
Device
Connection cable:
Use the special cable
Connector type:
Open-style connector or Micro-style connector
Termination resistor:
121
Ω
, 1/4 W (externally connected)
For details of the device profile, refer to the
APPENDIX A. DEVICE PROFILES (P. 103)
.
Controller communication
Interface:
Base on RS-485, EIA standard
Multi-drop connection is available.
Protocol:
Modbus-RTU
Synchronous method:
Half-duplex start-stop synchronous type
Connection method:
2-wire system, half-duplex multi-drop connection
Communication speed:
9600 bps, 19200 bps, 38400 bps
Data bit configuration:
Data 8-bit, Without parity, Stop 1-bit
Maximum connections:
31 controllers (SRZ module) *
*
A combined total of up to 31 Z-TIO and Z-DIO modules can be connected in the SRZ.
However, the maximum joinable number of functional modules of the same type is 16.
Connection method:
Terminals
Termination resistor:
Built-in terminal base of COM-JH [ON/OFF select with switch (120
Ω
)]
Maximum network length *
Communication
speed
Thick trunk length Thin trunk length
Maximum
drop length
Cumulative
drop length
125 kbps
500 m
156 m or less
250 kbps
250 m
100 m
6 m
78 m or less
500 kbps
100 m
39 m or less