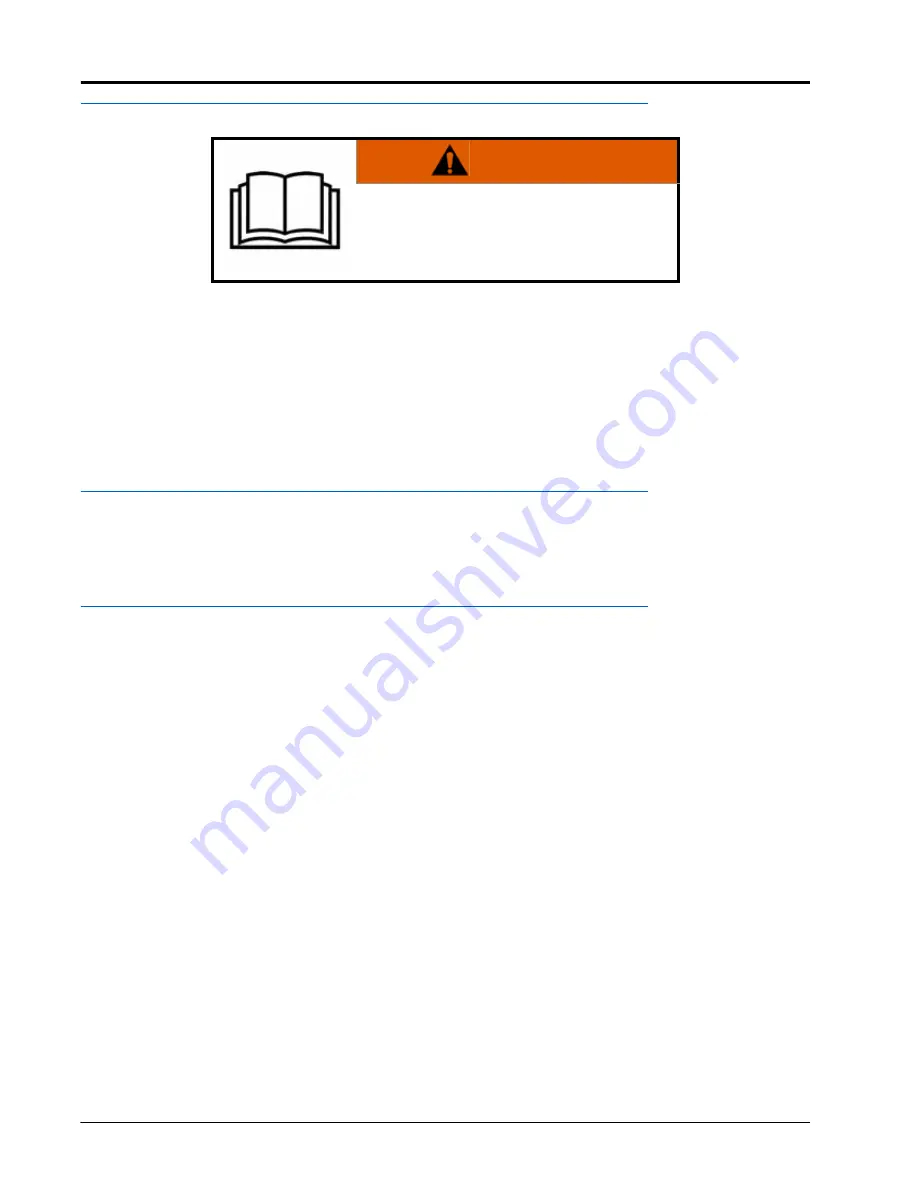
C
HAPTER
2
6
SmarTrax™ MD Calibration & Operation Manual
INSTALLATION
RECOMMENDATIONS
Before installing the SmarTrax MD system, park the machine where the ground is level, clean, and dry. Leave the
machine turned off for the duration of the installation process.
During the installation process, follow good safety practices. Be sure to carefully read the instructions in this
manual as you complete the installation process.
POINT OF REFERENCE
The instructions in this manual assume that you are standing behind the machine, looking toward the cab.
UPDATES
UPDATING THE NODE
The SmarTrax node may be updated in two ways:
• Via a USB drive loaded with the latest software and plugged into the field computer.
• Via the Raven Service Tool. Refer to the Raven Service Tool Installation & Operation Manual (P/N 016-5030-
022) for instructions on updating the node software.
Refer to the appropriate field computer manual for instructions on updating the node software:
• Viper/Viper 4+ Installation & Operation Manual (P/N 016-0171-539)
• Viper Pro Installation and Operation Manual (P/N 016-0171-122)
• Envizio Pro & Envizio Pro II Installation and Operation Manual (P/N 016-0171-148)
• Cruizer II Operation Guide (P/N 016-0171-415)
UPDATING THE MECHANICAL DRIVE
Update the mechanical drive software using a Windows-based operating system computer and the instructions
stored on the USB drive (P/N 063-0173-595) contained in the Raven Service Tool kit (P/N 117-0171-464).
When updating SmarTrax MD software, refer to the Raven Service Tool Installation Manual (P/N 016-5030-022)
located on the flash drive supplied with the installation kit. Software and manual updates are available on the
WARNING
Carefully read and follow all safety requirements
and precautions contained in this manual and the
machine-specific Installation Manual. Failure to
follow safety instructions may lead to equipment
damage, personal injury, or death.
Содержание SmarTrax MD
Страница 6: ...Table of Contents iv SmarTrax MD Calibration Operation Manual ...
Страница 10: ...CHAPTER 1 4 SmarTrax MD Calibration Operation Manual ...
Страница 14: ...CHAPTER 2 8 SmarTrax MD Calibration Operation Manual ...
Страница 46: ...CHAPTER 3 40 SmarTrax MD Calibration Operation Manual ...
Страница 76: ...CHAPTER 4 70 SmarTrax MD Calibration Operation Manual ...
Страница 112: ...CHAPTER 6 106 SmarTrax MD Calibration Operation Manual ...
Страница 114: ...CHAPTER 7 108 SmarTrax MD Calibration Operation Manual FIGURE 1 Cruizer II with Phoenix 300 and Slingshot Steering Only ...
Страница 115: ...7 P N 016 5030 020 Rev D 109 SYSTEM DIAGRAMS FIGURE 2 Envizio Pro or Viper Pro with Slingshot Steering Only ...
Страница 116: ...CHAPTER 7 110 SmarTrax MD Calibration Operation Manual ...
Страница 131: ...P N 016 5030 020 Rev D 125 ROADWAY HOMOLOGATION CERTIFICATION ...
Страница 132: ...CHAPTER 8 126 SmarTrax MD Calibration Operation Manual ...