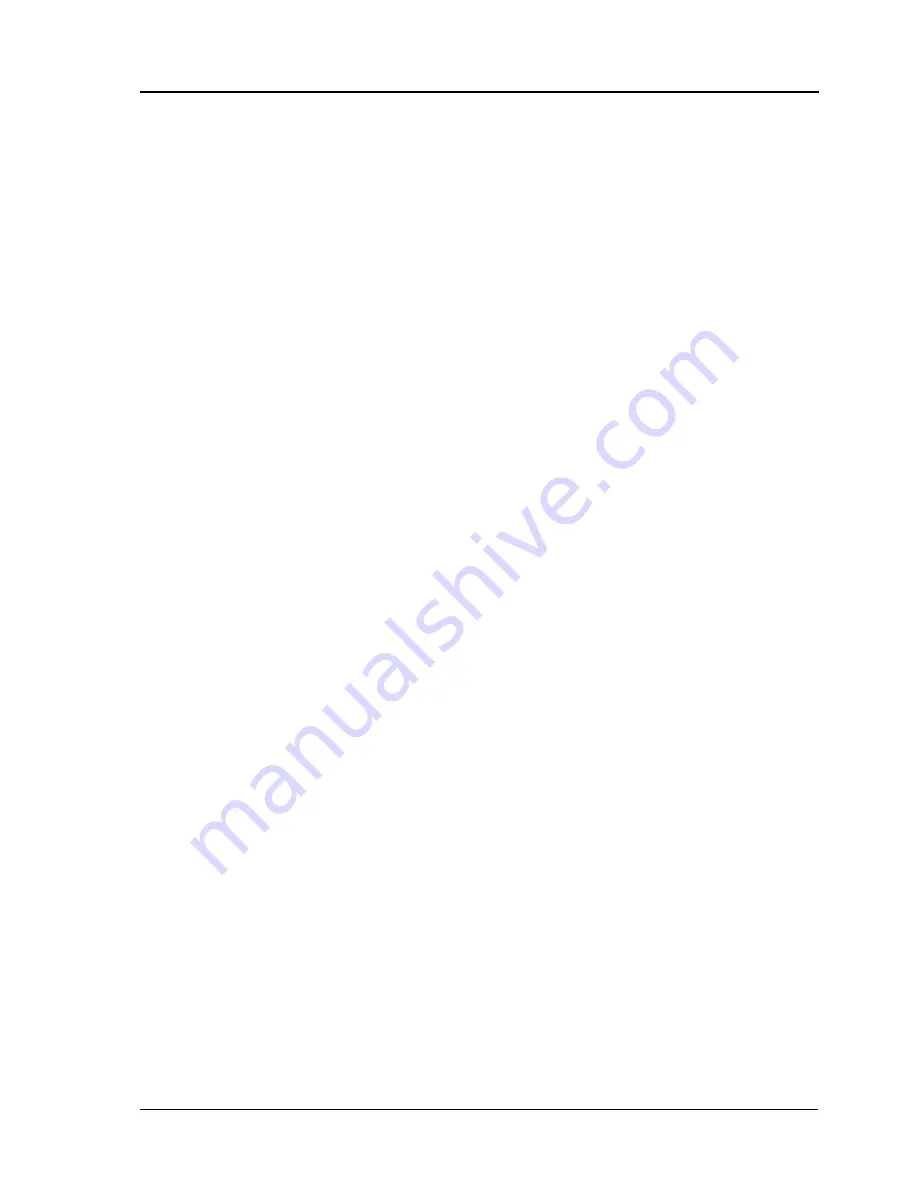
Workshop Manual, TPD 1350, issue 3
1
New 1000 Series
Perkins New 1000 Series
Models AJ to AS and YG to YK
WORKSHOP MANUAL
4 and 6 cylinder diesel engines for industrial and
agricultural applications
Publication TPD 1350E issue 3
© Proprietary information of Perkins Engines Company Limited, all rights reserved.
The information is correct at the time of print.
Published in March 2000 by Technical Publications.
Содержание New 1000 Series
Страница 16: ...10 16 Workshop Manual TPD 1350 issue 3 New 1000 Series L A0378N A0379...
Страница 30: ...30 This page is intentionally blank...
Страница 62: ...62 This page is intentionally blank...
Страница 108: ...108 This page is intentionally blank...
Страница 140: ...140 This page is intentionally blank...
Страница 160: ...19 160 Workshop Manual TPD 1350 issue 3 New 1000 Series 1 2 3 4 A A0289...
Страница 161: ...Workshop Manual TPD 1350 issue 3 161 19 New 1000 Series A A0290 1 2 3...
Страница 180: ...180 This page is intentionally blank...
Страница 284: ...284 This page is intentionally blank...