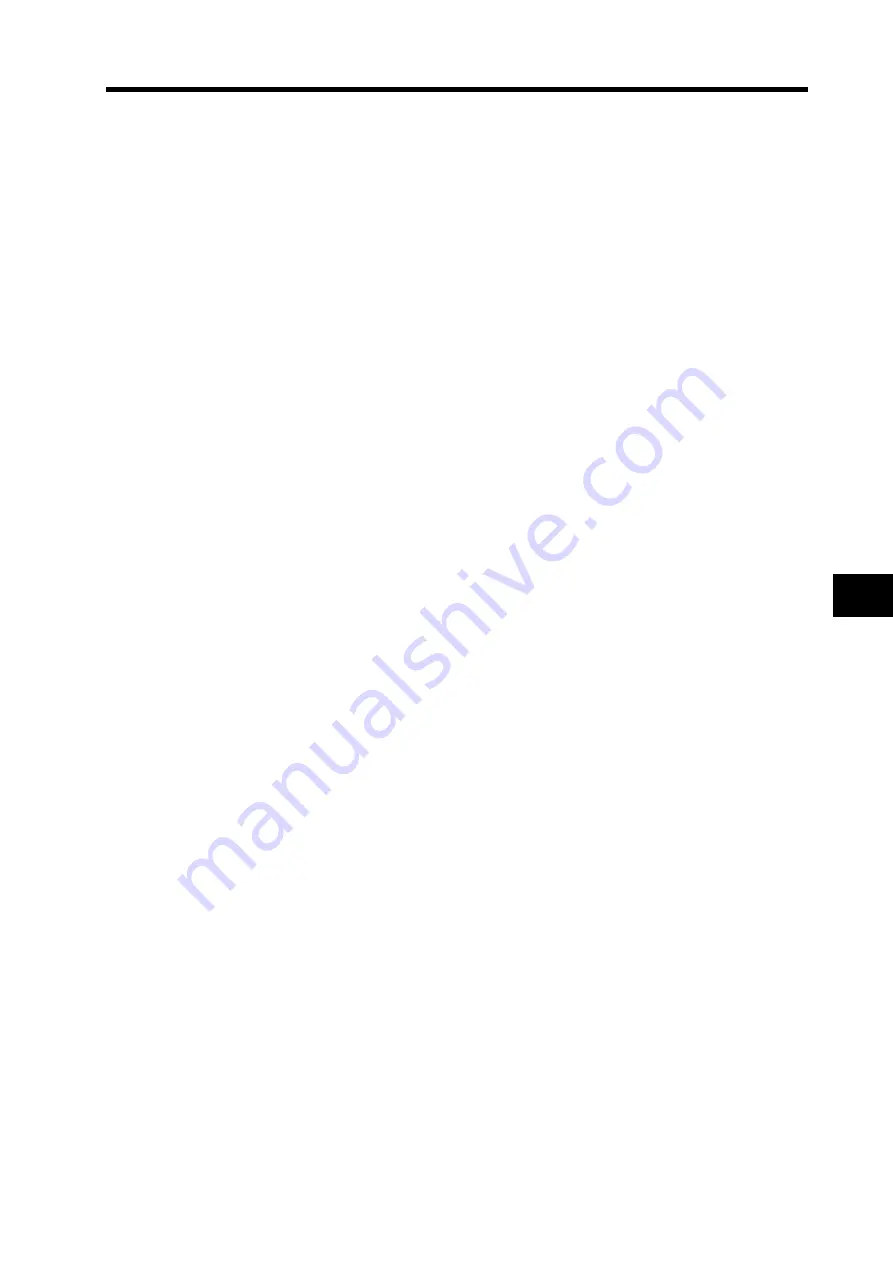
8-2
8-1 Error Processing
8
Troubleshooting
Precautions When Troubleshooting
When checking and verifying I/O after a problem has occurred, the Servo Drive may suddenly start
to operate or suddenly stop, so always take the following precautions.
You should assure that anything not described in this manual is not possible with this product.
Precautions
• Disconnect the cable before checking for wire breakage. Even if you test conduction with the cable
connected, test results may not be accurate due to conduction via bypassing circuit.
• If the encoder signal is lost, the Servomotor may run away, or an error may occur. Be sure to
disconnect the Servomotor from the mechanical system before checking the encoder signal.
• When measuring the encoder output, perform the measurement based on the SENGND (CN1 pin
13). When an oscilloscope is used for measurement, it will not be affected by noise if
measurements are performed using the differential between CH1 and CH2.
• When performing tests, first check that there are no persons in the vicinity of the equipment, and
that the equipment will not be damaged even if the Servomotor runs away. Before performing the
tests, verify that you can immediately stop the machine using an emergency stop even if the
Servomotor runs away.
Replacing the Servomotor and Servo Drive
Use the following procedure to replace the Servomotor or Servo Drive.
Replacing the Servomotor
1. Replace the Servomotor.
2. Perform origin position alignment (for position control).
• When the Servomotor is replaced, the Servomotor’s origin position (phase Z) may deviate, so
origin alignment must be performed.
• Refer to the Position Controller’s manual for details on performing origin alignment.
3. Set up the absolute encoder.
• If a Servomotor with an absolute encoder is used, the absolute value data in the absolute encoder
will be cleared when the Servomotor is replaced, so setup is again required. The rotation data will
be different from before the Servomotor was replaced, so reset the initial Motion Control Unit
parameters.
• For details, refer to
Absolute Encoder Setup Procedure
Replacing the Servo Drive
1. Copy the parameters.
Use the Parameter Unit or the operation keys on the Servo Drive to write down all the parameter
settings.
2. Replace the Servo Drive.
3. Set the parameters.
Use the Parameter Unit or the operation keys on the Servo Drive to set all the parameters.
4. Set up the absolute encoder.
• If a Servomotor with an absolute encoder is used, the absolute value data in the absolute encoder
will be cleared when the Servo Drive is replaced, so setup is again required. The rotation data will
be different from before the Servo Drive was replaced, so reset the initial Motion Control Unit
parameters.
• For details, refer to
Содержание R88D-GT series
Страница 20: ...18 Table of Contents ...
Страница 234: ...3 133 3 8 Reactor Specifications 3 Specifications ...
Страница 448: ...7 37 7 5 Manual Tuning 7 Adjustment Functions ...
Страница 474: ...8 25 8 5 Periodic Maintenance 8 Troubleshooting ...
Страница 475: ...Chapter 9 Appendix 9 1 Connection Examples 9 1 9 2 Parameter Tables 9 11 ...
Страница 509: ......