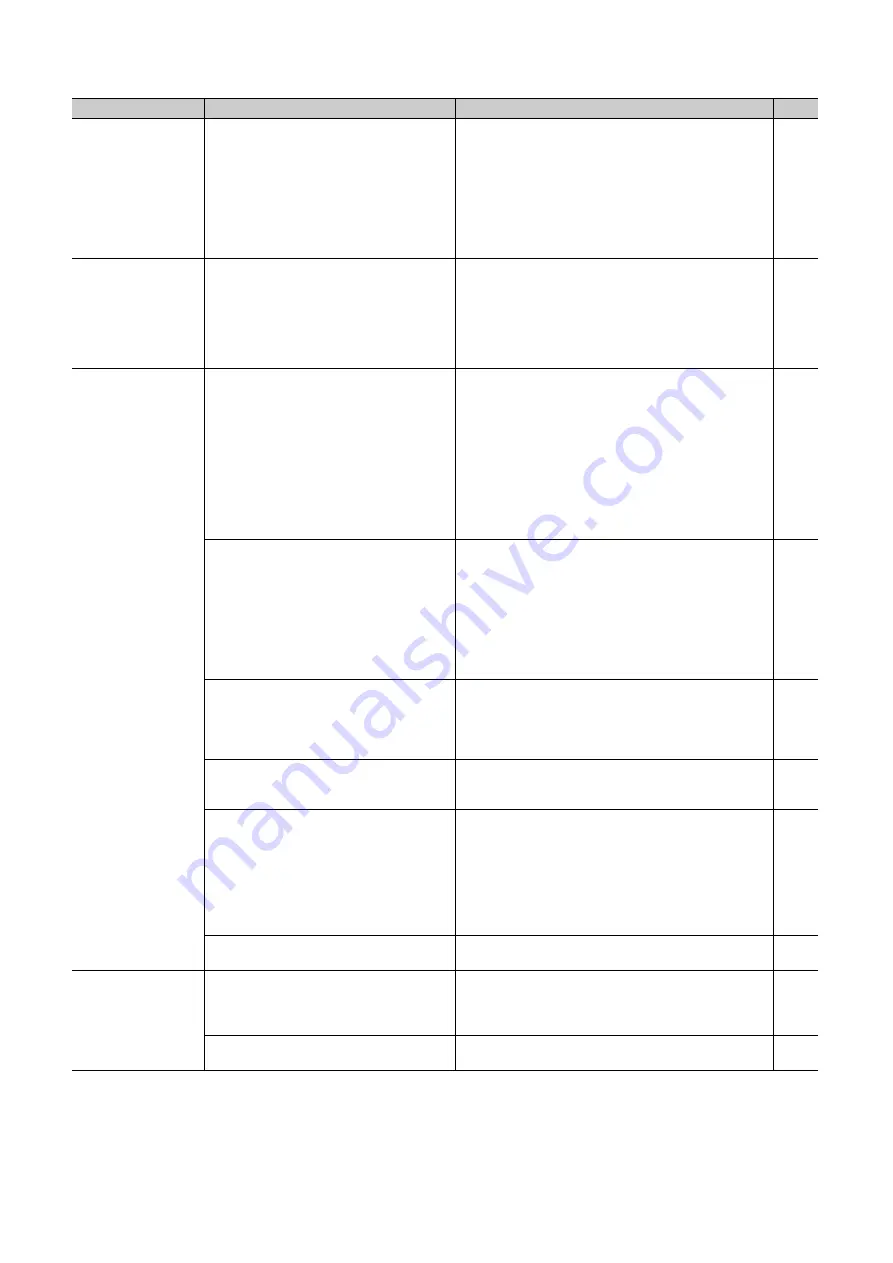
790
Electronic gear
A setting of "1
m = 1 pulse" is required in the
following system.
• Ball screw pitch = 10mm
• Feedback pulses = 8192 pulse
In this case, the following values will result.
• No. of pulses per rotation = 8192
• Movement amount per rotation = 10000
• Unit magnification = 10
Therefore, the "Movement amount per pulse" will become
"1.2207
m".
This value is fixed by the machine system, so it cannot be
changed.
Thus, the setting "1
m = 1pulse" cannot be achieved.
17
Error compensation
The machine only moves to "10081230", although
positioning with a command value of "10081234"
carried out.
How can the error be compensated?
The following values are currently set.
• [Pr.2] No. of pulses per rotation = 8192
• [Pr.3] Movement amount per rotation = 8000
Reset [Pr.3] and [Pr.2] in the following order.
1)
Calculate "8192/8000
10081230/10081234".
2)
Obtain the reduced value.
3)
Set the numerator in "[Pr.3] Movement amount per rotation",
and the denominator in "[Pr.2] No. of pulses per rotation".
18
OPR
When carrying out a count method machine OPR,
the message "Leave Sufficient Distance From The
OP Position To The Near-Point Dog OFF." appears.
Is there a problem if the distance is short?
The near-point dog must be set to turn OFF at a position after the
OP is passed.
(When the machine OPR is started on the near-point dog on in a
count-method machine OPR, the machine enters a normal
machine OPR operation after returning to the near-point dog OFF
region.)
(If the near-point dog is turned OFF before the OP, and the
machine OPR is started between the near-point dog OFF position
and the OP, the machine will mistakenly interpret that its current
position is before the near-point dog ON position, and it will pass
over the OP and continue moving.)
19
In the near-point dog method machine OPR, the
stop positions are not uniform.
Carry out the following measures.
1)
Separate the near-point dog signal and zero signal detection
positions.
2)
Lower the values in "[Pr.46] OPR speed" and "[Pr.47] Creep
speed".
3)
Confirm whether the zero signal and near-point dog signal
turn ON normally.
4)
Check that there is no play (backlash) in the machine
system.
20
Can the machine OPR be carried out with the OPR
retry function when it is started with the near-point
dog ON and the upper/lower limit OFF?
A "Hardware stroke limit error" will occur and the operation will not
be carried out.
(The machine will interpret any position where the near-point dog
is ON as being within the working range, and that the upper/lower
limit is ON.)
21
Are ABS and INC positioning possible without
carrying out an OPR?
They are possible.
In this case, the position where the power is turned ON is handled
as the current feed value "0".
22
After an OPR, the OPR request flag sometimes
turns ON for no apparent reason.
The OPR request flag turns ON in the following cases.
1)
When the power is turned ON.
2)
When the PLC READY signal [YO] turns from OFF to ON.
3)
When an OPR is carried out.
4)
When the servo amplifier power is turned OFF.
If no problem is found when the above are checked, then it is
possible that the communication is being interrupted by "a fault in
the bus cable", "noise influence", etc.
23
The OPR complete flag ([Md.31] Status: b4)
sometimes turns ON when it shouldn't be ON.
Check whether the drive unit READY signal is weak or the power
supply is unstable.
24
Start
The positioning start signal [Y10] is kept ON until
the BUSY signal is OFF, but is there any problem
with turning it OFF before the BUSY signal turns
OFF?
After the BUSY signal turns ON, there is no problem with turning
[Y10] OFF before the BUSY signal turns OFF.
(The LD75 detects the rising edge (OFF
ON) of the positioning
start signal [Y10].)
25
The operation will not start even when the start
signal is turned ON.
Check the "[Md.26] Axis operation status" and "[Md.23] Axis error
No.".
26
Trouble type
Questions/Trouble
Remedy
No.
Содержание MELSEC-L LD75D
Страница 1: ...MELSEC L LD75P LD75D Positioning Module User s Manual LD75P1 LD75P2 LD75P4 LD75D1 LD75D2 LD75D4 ...
Страница 2: ......
Страница 11: ...9 Memo ...
Страница 47: ...45 CHAPTER 2 SYSTEM CONFIGURATION 2 2 1 General Image of System 1 When connected to a CPU module ...
Страница 176: ...174 ...
Страница 264: ...262 ...
Страница 266: ...264 ...
Страница 267: ...265 CHAPTER 6 PROGRAM USED FOR POSITIONING CONTROL 6 6 4 Positioning Program Examples ...
Страница 268: ...266 ...
Страница 269: ...267 CHAPTER 6 PROGRAM USED FOR POSITIONING CONTROL 6 6 4 Positioning Program Examples ...
Страница 270: ...268 ...
Страница 271: ...269 CHAPTER 6 PROGRAM USED FOR POSITIONING CONTROL 6 6 4 Positioning Program Examples ...
Страница 272: ...270 Z ABRST1 instruction execution ...
Страница 273: ...271 CHAPTER 6 PROGRAM USED FOR POSITIONING CONTROL 6 6 4 Positioning Program Examples ...
Страница 278: ...276 ...
Страница 279: ...277 CHAPTER 6 PROGRAM USED FOR POSITIONING CONTROL 6 6 4 Positioning Program Examples ...
Страница 280: ...278 ...
Страница 281: ...279 CHAPTER 6 PROGRAM USED FOR POSITIONING CONTROL 6 6 4 Positioning Program Examples ...
Страница 282: ...280 ...
Страница 283: ...281 CHAPTER 6 PROGRAM USED FOR POSITIONING CONTROL 6 6 4 Positioning Program Examples ...
Страница 284: ...282 ...
Страница 285: ...283 CHAPTER 6 PROGRAM USED FOR POSITIONING CONTROL 6 6 4 Positioning Program Examples ...
Страница 286: ...284 ...
Страница 287: ...285 CHAPTER 6 PROGRAM USED FOR POSITIONING CONTROL 6 6 4 Positioning Program Examples ...
Страница 316: ...314 Memo ...
Страница 685: ...683 APPENDICES A Appendix 1 Function Update Appendix 1 1 Function comparison Memo ...
Страница 738: ...736 Memo ...
Страница 806: ...804 5 LD75D2 Unit mm 6 LD75D4 Unit mm 45 4 90 4 95 4 45 45 DIN rail center 45 4 90 4 95 4 45 45 DIN rail center ...
Страница 817: ......