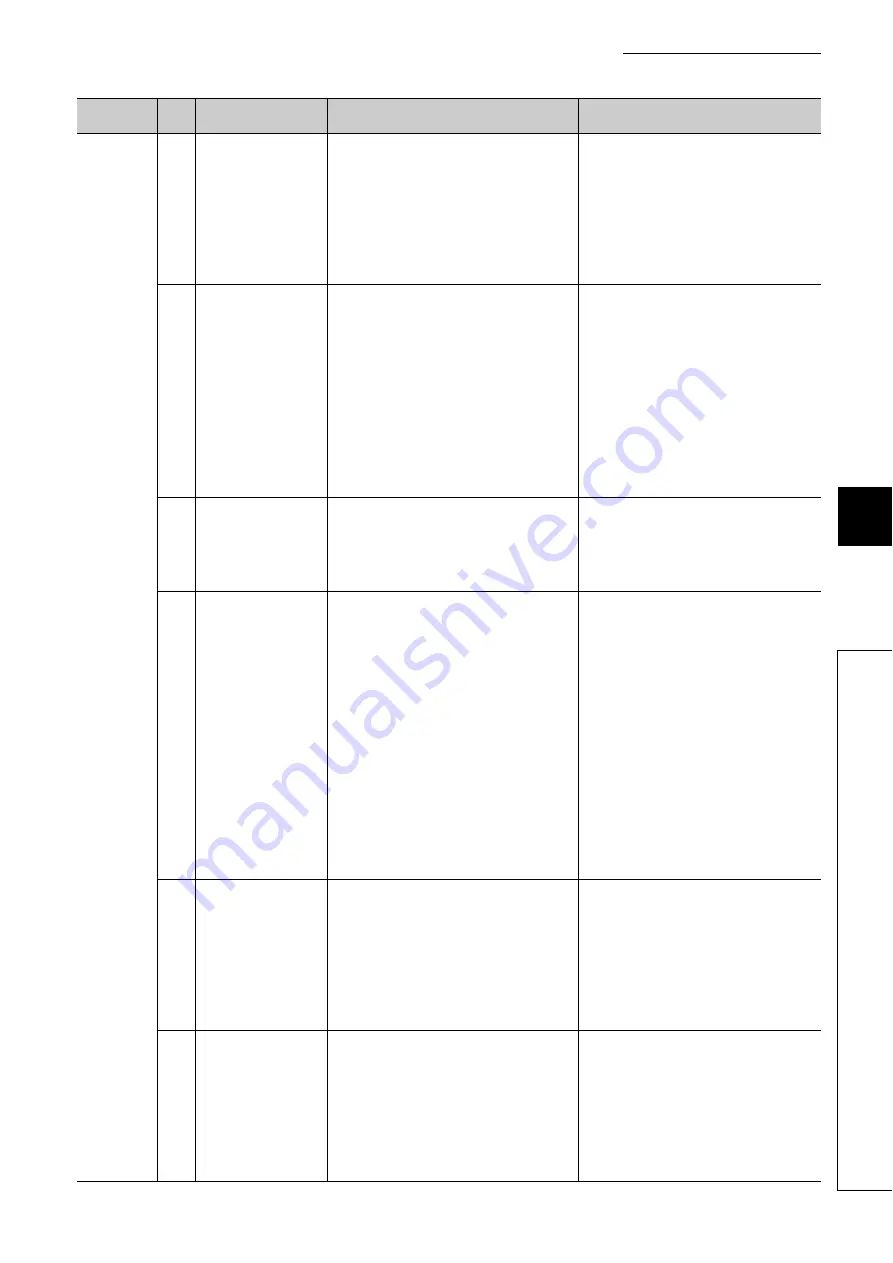
667
CHAPTER 15 TROUBLESHOOTING
15
15.
5
List
of
E
rrors
Parameter
905
Rotation direction setting
error
■
Description
The set value of the basic parameter 1 "Rotation
direction setting" is outside the setting range.
■
Operation status at error occurrence
The LD75 READY signal (X0) does not turns ON.
■
Action
With the setting brought into the setting range,
turn the PLC READY signal [Y0] from OFF to ON.
■
Buffer memory address
Axis 1: 5
Axis 2: 155
Axis 3: 305
Axis 4: 455
■
Setting range
0, 1
906
Outside bias speed range
■
Description
• The set value of the basic parameter 1 "Bias
speed at start" is outside the setting range.
• The bias speed exceeds the speed limit.
■
Operation status at error occurrence
The LD75 READY signal (X0) does not turns ON.
■
Action
• Set the bias speed to not more than the speed
limit value.
• With the setting brought into the setting range,
turn the PLC READY signal [Y0] from OFF to
ON.
■
Buffer memory address
Axis 1: 6, 7
Axis 2: 156, 157
Axis 3: 306, 307
Axis 4: 456, 457
■
Setting range
0 to 4000000 [pulse/s], 0 to 2000000000 [
10
-2
mm/min or other]
908
Use prohibited area write
error
■
Description
Any value other than 0 was set at buffer memory
address 101, 251, 401, 551 (use prohibited area).
■
Operation status at error occurrence
LD75 READY signal (X0) does not turn on.
■
Action
• With the setting value being 0, turn on PLC
READY signal [Y0].
• Review the program which sets a value at
buffer memory address 101, 251, 401, 551 (use
prohibited area).
910
Outside speed limit value
range
■
Description
The set value of the basic parameter 2 "Speed limit
value" is outside the setting range.
• The value obtained by the conversion of the
speed limit value with respect to the frequency
exceeds the maximum output frequency of the
unit.
• The speed limit value is smaller than the OPR
speed.
■
Operation status at error occurrence
When the power is turned ON or PLC READY
signal (Y0) is turned from OFF to ON: LD75 READY
signal (X0) is not turned ON.
At start: The system will not operate.
■
Action
The value converted into the frequency should
not exceed the maximum output frequency of the
module.
LD75P
: 200000 [pulse/s]
LD75D
: 4000000 [pulse/s]
• Set a value which is not less than the OPR
speed.
• With the setting brought into the setting range,
turn the PLC READY signal [Y0] from OFF to
ON.
■
Buffer memory address
Axis 1: 10, 11
Axis 2: 160, 161
Axis 3: 310, 311
Axis 4: 460, 461
■
Setting range
1 to 4000000 [pulse/s], 1 to 2000000000 [
10
-2
mm/min or other]
911
Outside acceleration time
0 range
■
Description
The set value of the basic parameter 2
"Acceleration time 0" is outside the setting range.
■
Operation status at error occurrence
When the power is turned ON or PLC READY
signal (Y0) is turned from OFF to ON: LD75 READY
signal (X0) is not turned ON.
At start: The system will not operate.
■
Action
With the setting brought into the setting range,
turn the PLC READY signal [Y0] from OFF to ON.
■
Buffer memory address
Axis 1: 12, 13
Axis 2: 162, 163
Axis 3: 312, 313
Axis 4: 462, 463
■
Setting range
1 to 8388608
912
Outside deceleration time
0 range
■
Description
The set value of the basic parameter 2
"Deceleration time 0" is outside the setting range.
■
Operation status at error occurrence
When the power is turned ON or PLC READY
signal (Y0) is turned from OFF to ON: LD75 READY
signal (X0) is not turned ON.
At start: The system will not operate.
■
Action
With the setting brought into the setting range,
turn the PLC READY signal [Y0] from OFF to ON.
■
Buffer memory address
Axis 1: 14, 15
Axis 2: 164, 165
Axis 3: 314, 315
Axis 4: 464, 465
■
Setting range
1 to 8388608
Classification
of errors
Error
code
Error name
Operation status at error occurrence
Action/Related buffer memory address/Set
range (Setting with program)
Содержание MELSEC-L LD75D
Страница 1: ...MELSEC L LD75P LD75D Positioning Module User s Manual LD75P1 LD75P2 LD75P4 LD75D1 LD75D2 LD75D4 ...
Страница 2: ......
Страница 11: ...9 Memo ...
Страница 47: ...45 CHAPTER 2 SYSTEM CONFIGURATION 2 2 1 General Image of System 1 When connected to a CPU module ...
Страница 176: ...174 ...
Страница 264: ...262 ...
Страница 266: ...264 ...
Страница 267: ...265 CHAPTER 6 PROGRAM USED FOR POSITIONING CONTROL 6 6 4 Positioning Program Examples ...
Страница 268: ...266 ...
Страница 269: ...267 CHAPTER 6 PROGRAM USED FOR POSITIONING CONTROL 6 6 4 Positioning Program Examples ...
Страница 270: ...268 ...
Страница 271: ...269 CHAPTER 6 PROGRAM USED FOR POSITIONING CONTROL 6 6 4 Positioning Program Examples ...
Страница 272: ...270 Z ABRST1 instruction execution ...
Страница 273: ...271 CHAPTER 6 PROGRAM USED FOR POSITIONING CONTROL 6 6 4 Positioning Program Examples ...
Страница 278: ...276 ...
Страница 279: ...277 CHAPTER 6 PROGRAM USED FOR POSITIONING CONTROL 6 6 4 Positioning Program Examples ...
Страница 280: ...278 ...
Страница 281: ...279 CHAPTER 6 PROGRAM USED FOR POSITIONING CONTROL 6 6 4 Positioning Program Examples ...
Страница 282: ...280 ...
Страница 283: ...281 CHAPTER 6 PROGRAM USED FOR POSITIONING CONTROL 6 6 4 Positioning Program Examples ...
Страница 284: ...282 ...
Страница 285: ...283 CHAPTER 6 PROGRAM USED FOR POSITIONING CONTROL 6 6 4 Positioning Program Examples ...
Страница 286: ...284 ...
Страница 287: ...285 CHAPTER 6 PROGRAM USED FOR POSITIONING CONTROL 6 6 4 Positioning Program Examples ...
Страница 316: ...314 Memo ...
Страница 685: ...683 APPENDICES A Appendix 1 Function Update Appendix 1 1 Function comparison Memo ...
Страница 738: ...736 Memo ...
Страница 806: ...804 5 LD75D2 Unit mm 6 LD75D4 Unit mm 45 4 90 4 95 4 45 45 DIN rail center 45 4 90 4 95 4 45 45 DIN rail center ...
Страница 817: ......