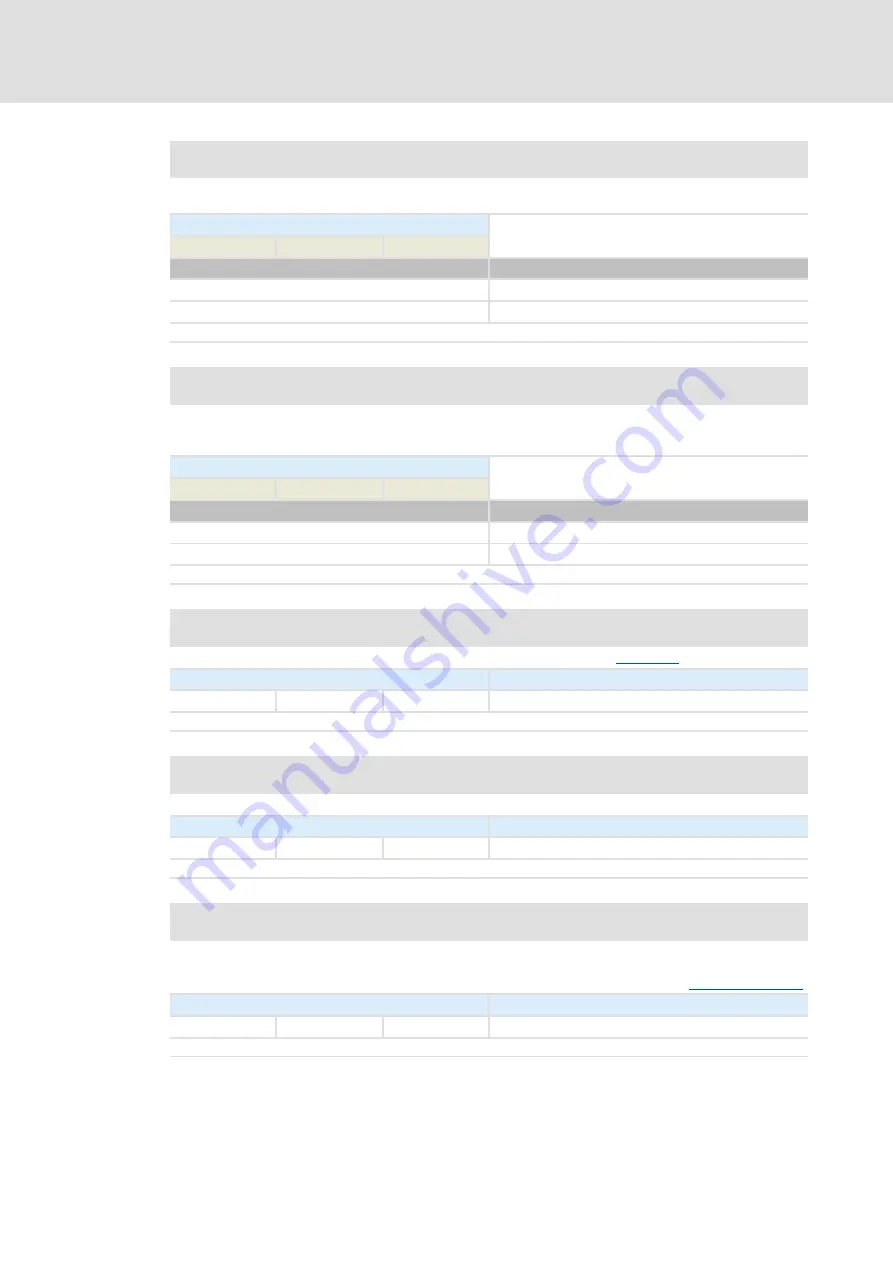
8400 motec | Software Manual
Parameter reference
Parameter list | C00980
292
L
Firmware
≤
02.00 - DMS 2.1 EN - 03/2011
C00980
C00981
C00982
C00984
C00987
Parameter | Name:
C00980 | Output power
Data type: INTEGER_32
Index: 23595
d
= 5C2B
h
These display parameters serve to execute an energy analysis in the respective application. From this, decisions can
be derived whether a measurement for energy optimisation is economical.
Display range
(min. value | unit | max. value)
0.000
kW
32.000
Subcodes
Info
C00980/1
Active output power
C00980/2
Apparent output power
;
Read access
Write access
CINH
PLC STOP
No transfer
COM
;
MOT
Scaling factor: 1000
Parameter | Name:
C00981 | Energy display
Data type: INTEGER_32
Index: 23594
d
= 5C2A
h
These display parameters serve to execute an energy analysis in the respective application. From this, decisions can
be derived whether a measurement for energy optimisation is economical.
• The values are saved in the device by switching off the mains and cannot be reset.
Display range
(min. value | unit | max. value)
0.00
kWh
21474836.47
Subcodes
Info
C00981/1
Output energy in motor mode
C00981/2
Output energy in generator mode
;
Read access
Write access
CINH
PLC STOP
No transfer
COM
;
MOT
Scaling factor: 100
Parameter | Name:
C00982 | VFC-ECO: Minimum voltage V/f ramp
Data type: UNSIGNED_8
Index: 23593
d
= 5C29
h
Voltage ramp for cancelling V sub with energy-saving V/f characteristic control (
Setting range
(min. value | unit | max. value)
Lenze setting
0.1
s
5.0
0.5 s
;
Read access
;
Write access
CINH
PLC STOP
No transfer
COM
;
MOT
Scaling factor: 10
Parameter | Name:
C00984 | Motor flux Add
Data type: INTEGER_16
Index: 23591
d
= 5C27
h
From version 02.00.00
Setting range
(min. value | unit | max. value)
Lenze setting
0.0
%
199.9
20.0 %
;
Read access
;
Write access
CINH
PLC STOP
No transfer
COM
MOT
Scaling factor: 100
Parameter | Name:
C00987 | Inverter motor brake: nAdd
Data type: INTEGER_16
Index: 23588
d
= 5C24
h
From version 02.00.00
Speed hub that is applied to the deceleration ramp in pulse mode when the motor is braked.
Setting range
(min. value | unit | max. value)
Lenze setting
0
rpm
1000
80 rpm
;
Read access
;
Write access
CINH
PLC STOP
No transfer
COM
;
MOT
Scaling factor: 1
Содержание 8400 motec Series
Страница 375: ...L 375 ...