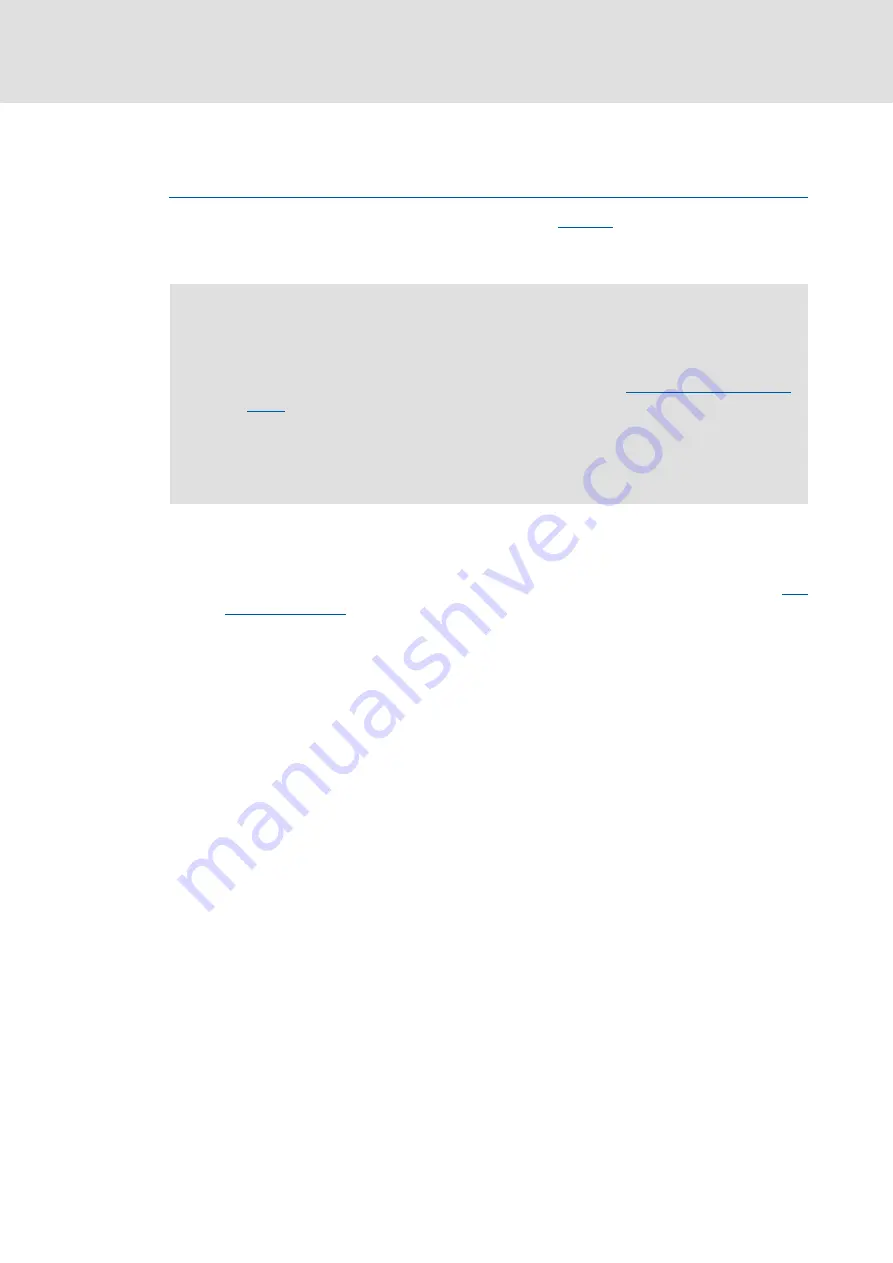
8400 motec | Software Manual
Motor control (MCTRL)
Braking operation/braking energy management
116
L
Firmware
≤
02.00 - DMS 2.1 EN - 03/2011
5.11.3.1
Inverter motor brake
This function extension is available from version 02.00.00!
With this alternative brake procedure to be selected in
, energy of the regenerative
energy is converted in the motor by a dynamic acceleration/deceleration in connection
with the ramping down of the ramp function generator.
Tip!
If no brake resistor is used, the DC injection brake can also be used for braking in
addition to the "inverter motor brake" and "stop of deceleration" function.
For applications with high mass inertia and long braking times (> 2 s), we
recommend to use the DC injection brake.
• The DC injection brake allows for an oscillation-reduced braking process. The
duration of the braking process is generally longer than with the "inverter
motor brake" function with an optimum setting. Moreover, the function is only
recommended for a braking to a standstill.
In the following cases we recommend to use the "inverter motor brake" function:
• For all applications where it is not braked to a standstill (e.g. braking to a lower
speed setpoint) or where the braking process can be interrupted by defining a
new speed setpoint.
• For applications with low mass inertias and a short braking time (< 1 s).
• For all applications where a quick braking is to be achieved.
Stop!
• This braking procedure only works with speed-controlled applications
without intervention of a position controller!
• When the "Inverter motor brake" function is used, the
is not adapted. If it is braked too frequently, there is a risk of the motor
being thermally overloaded or the motor overload monitoring does not work
properly!
• The "inverter motor brake" function must not be used with vertical conveyors
(hoists) or active loads!
Содержание 8400 motec Series
Страница 375: ...L 375 ...