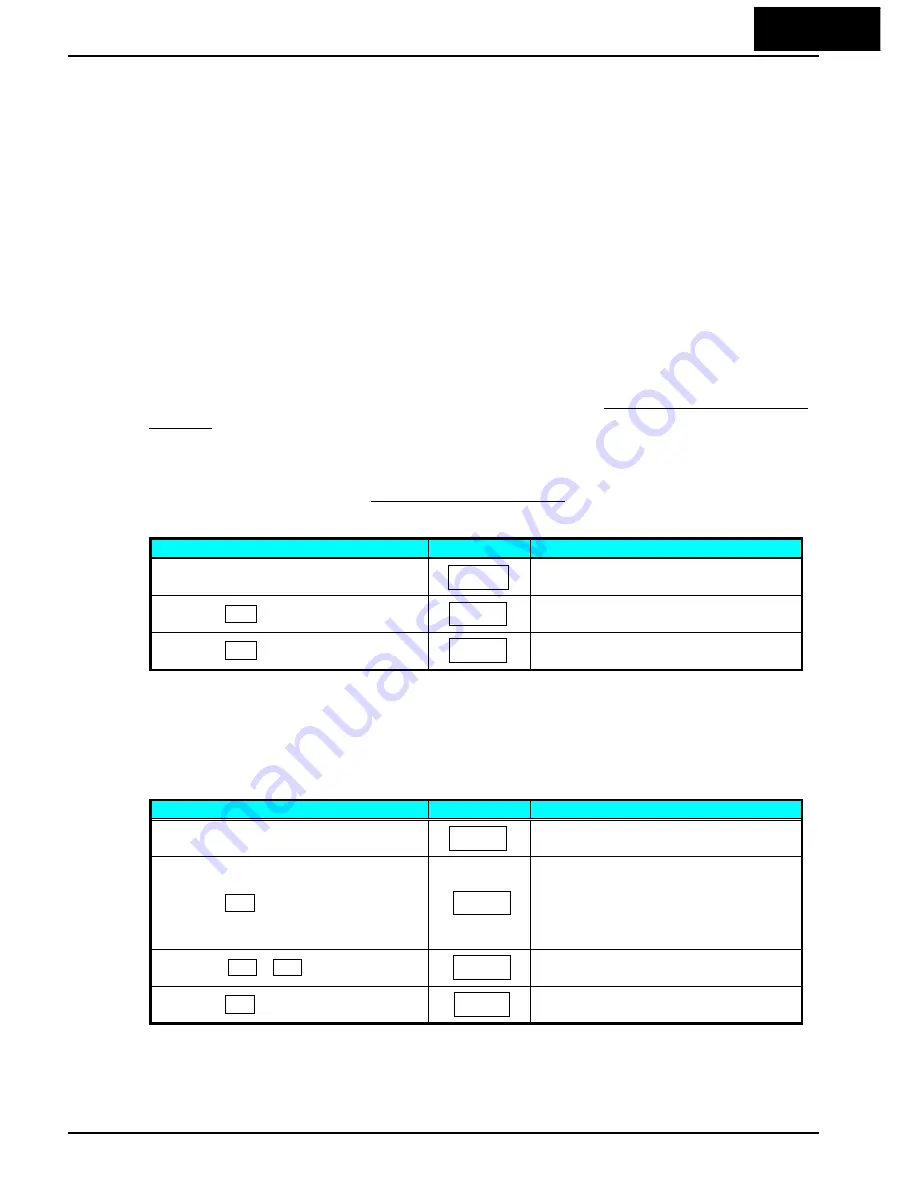
2
−
29
Selecting Functions and Editing Parameters
To prepare to run the motor in the powerup test, this section will show how to
configure the necessary parameters:
1.
Select the digital operator as the source of motor speed command (
A001
=
02
).
2.
Select the digital operator as the source of the RUN command (
A002
=
02
).
3.
Set the motor base frequency (
A003
) and AVR voltage of the motor (
A082
).
4.
Set the motor current for proper thermal protection (
b012
).
5.
Set the number of poles for the motor (
H004
).
The following series of programming tables are designed for successive use. Each table
uses the previous table’s final state as the starting point. Therefore, start with the first
and continue programming until the last one. If you get lost or concerned that some of
the other parameters setting may be incorrect, refer to “Restoring Factory Default
Settings” on page 6-8.
Prepare to Edit Parameters –
This sequence begins with powering ON the inverter,
then it shows how to navigate to the “A” Group parameters for subsequent settings.
You can also refer to the “Keypad Navigation Map” on page 2-26 for orientation
throughout the steps.
Action
Display
Func./Parameter
Turn ON the inverter
0
.
0
Inverter output frequency displayed
(0Hz in stop mode)
Press the ESC key.
d001
“
d
” group selected
Press the ESC key 2 times.
A001
“
A
” group selected
1. Select the digital operator for Speed Command –
The inverter output frequency
can be set from several sources, including an analog input, memory setting, or the
network, for example. The powerup test uses the keypad as the speed control source
for your convenience. Note that the default setting depends on the country.
Action
Display
Func./Parameter
(Starting point)
A001
“A” Group selected
Speed command source setting
Press the SET key
01
00
…
Potentiometer of ext. operator
01
…
Control terminals
02
…
Digital operator (F001)
03
…
ModBus network
etc.
Press the
U
/
V
key to select
02
02
…
Digital operator (selected)
Press the SET key to store
A001
Stores parameter, returns to “
A001
”
Содержание WJ200 Series Software
Страница 19: ...xviii Revisions Revision History Table No Revision Comments Date of Issue Operation Manual No ...
Страница 59: ...2 14 Dimensional drawings continued Power Type W mm H mm D mm D1 mm 3 phase 200V WJ200 150LF 220 350 175 84 ...
Страница 295: ...4 92 Safe Stop Function To be finalized after TUV approval ...
Страница 296: ...5 1 5 Inverter System Accessories In This Chapter page Introduction 2 Component Description 3 ...
Страница 322: ...A 1 A Glossary and Bibliography In This Appendix page Glossary 2 Bibliography 8 ...
Страница 378: ...B 49 Note 2 Be sure not to write into above 1F02h to 1F1Dh ...
Страница 382: ...C 1 Drive Parameter Setting Tables In This Appendix page Introduction 2 Parameter Settings for Keypad Entry 2 C ...