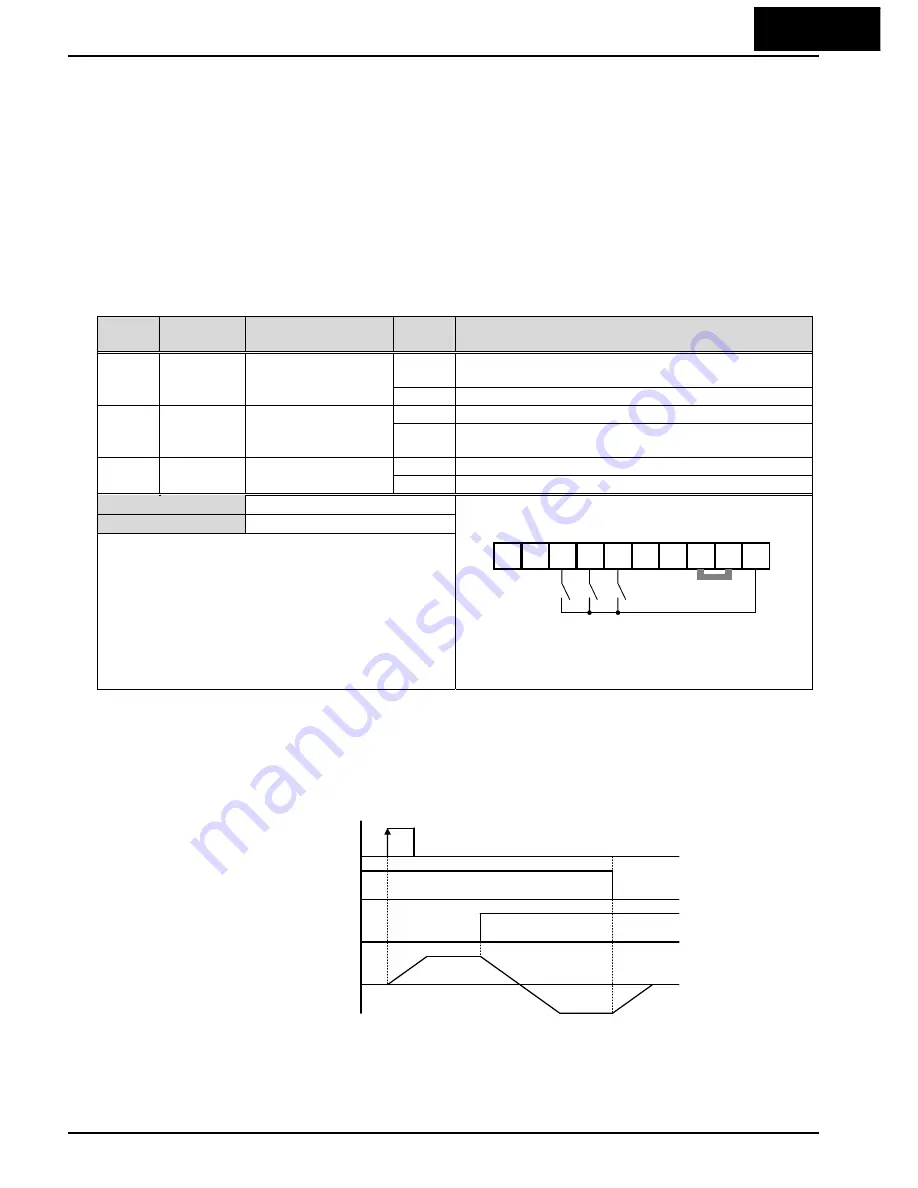
4
−
31
Three-wire Interface Operation
The 3-wire interface is an industry standard motor control interface. This function uses
two inputs for momentary contact start/stop control, and a third for selecting forward
or reverse direction. To implement the 3-wire interface, assign
20
[STA] (Start),
21
[STP] (Stop), and
22
[F/R] (Forward/Reverse) to three of the intelligent input terminals.
Use a momentary contact for Start and Stop. Use a selector switch, such as SPST for
the Forward/Reverse input. Be sure to set the operation command selection
A002
=
01
for
input terminal control of motor.
If you have a motor control interface that needs logic-level control (rather than
momentary pulse control), use the [FW] and [RV] inputs instead.
Option
Code
Terminal
Symbol
Function Name
State
Description
20
STA
Start Motor
ON
Start motor rotation on momentary contact (uses
acceleration profile)
OFF
No change to motor operation
21
STP
Stop Motor
ON
No change to motor operation
OFF
Stop motor rotation on momentary contact (use
deceleration profile)
22
F/R
Forward/Reverse
ON
Select reverse direction of rotation
OFF
Select forward direction of rotation
Valid for inputs:
C001
~
C007
Example (default input configuration shown):
See I/O specs in chapter 4
.
Required settings
A002
=
01
Notes:
•
The STP logic is inverted. Normally the switch will
be closed, so you open the switch to stop. In this
way, a broken wire causes the motor to stop
automatically (safe design).
•
When you configure the inverter for 3-wire
interface control, the dedicated [FW] terminal is
automatically disabled. The [RV] intelligent
terminal assignment is also disabled.
The diagram below shows the use of 3-wire control. STA (Start Motor) is an
edge-sensitive input; an OFF-to-ON transition gives the Start command. The control of
direction is level-sensitive, and the direction may be changed at any time. STP (Stop
Motor) is also a level-sensitive input.
F/R STP STA
7
6
5
4
3
2
1
L
PCS
P24
[STP] terminal
1
0
t
[F/R] terminal 1
0
Motor revolution
speed
[STA] terminal
1
0
PLC
Содержание WJ200 Series Software
Страница 19: ...xviii Revisions Revision History Table No Revision Comments Date of Issue Operation Manual No ...
Страница 59: ...2 14 Dimensional drawings continued Power Type W mm H mm D mm D1 mm 3 phase 200V WJ200 150LF 220 350 175 84 ...
Страница 295: ...4 92 Safe Stop Function To be finalized after TUV approval ...
Страница 296: ...5 1 5 Inverter System Accessories In This Chapter page Introduction 2 Component Description 3 ...
Страница 322: ...A 1 A Glossary and Bibliography In This Appendix page Glossary 2 Bibliography 8 ...
Страница 378: ...B 49 Note 2 Be sure not to write into above 1F02h to 1F1Dh ...
Страница 382: ...C 1 Drive Parameter Setting Tables In This Appendix page Introduction 2 Parameter Settings for Keypad Entry 2 C ...