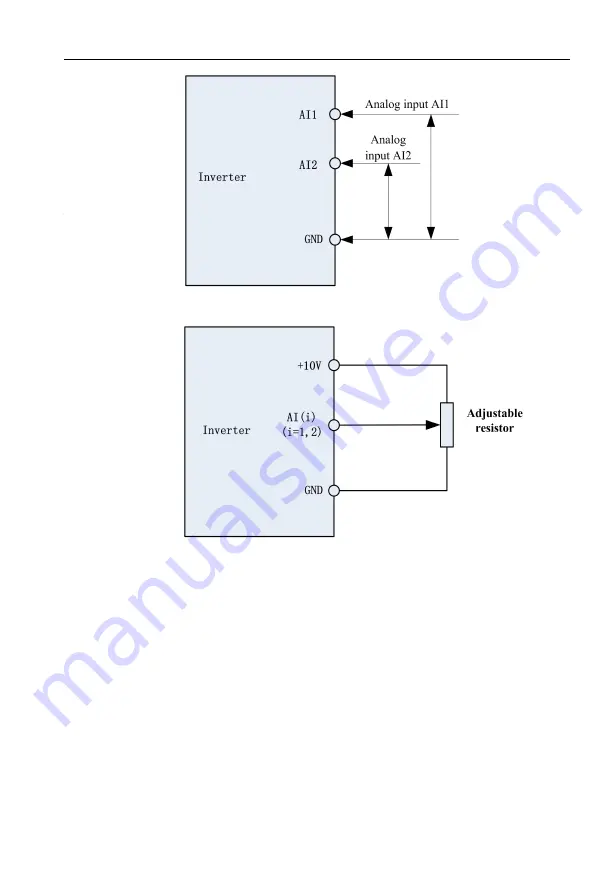
FR500A&FR510A Series Vector Control Inverter
- 83 -
as Fig. 6-2:
Fig. 6-2
If 10V power supply inside the drive is used with potentiometer, the connection diagram is shown
as Fig. 6-3. Note that the toggle switch should be switched to voltage input side.
Fig. 6-3
3: Communication
Upper computer is the master frequency command source of the drive through standard RS485
communication interface on the drive. Refer to Group F15 and appendix on this manual for further
information about communication protocol, and programming, etc.
4: Multi-reference
In multi-reference mode, combinations of different DI terminal states correspond to different set
frequencies. The FR500A&FR510A supports a maximum of 16 speeds implemented by 16 state
combinations of four DI terminals (allocated with functions 13 to 16) in Group F04. The multiple
references indicate percentages of the value of F01.08 (Maximum frequency).
If a DI terminal is used for the multi-reference function, you need to perform related setting in
group F04.
5: PLC
Master frequency command is determined by simple PLC. See parameter Group F12 for details.
6: Process PID output
Master frequency command is determined by process closed-loop PID computation result. See
parameter Group F13 for details.
7: DI7/HI pulse input
If this parameter value selected, command frequency will be determined by pulse frequency input
via terminal DI7/HI only. In such a case, F00.09 should be set to 1. Corresponding relation between
pulse frequency and command frequency is specified in F06.32
~
F06.35.
8: AI2