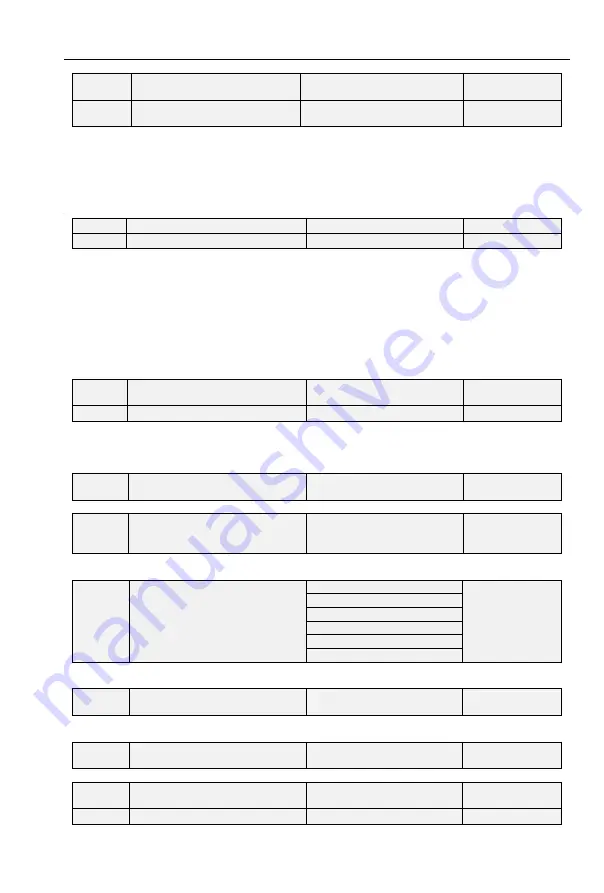
FR500A&FR510A Series Vector Control Inverter
- 117 -
The target torque is set by means of communication.
F10.18
Forward speed limited value
under torque control
Range:0.0
~
Fmax
Default:50.0Hz
F10.19
Reverse speed limited value
under torque control
Range:0.0
~
Fmax
Default:50.0Hz
When F00.26=0,Two parameters are used to set the maximum frequency in forward or reverse
rotation in torque control mode.
In torque control, if the load torque is smaller than the motor output torque, the motor's rotational
speed will rise continuously. To avoid runaway of the mechanical system, the motor maximum rotating
speed must be limited in torque control.
You can implement continuous change of the maximum frequency in torque control dynamically
by controlling the frequency upper limit.
F10.20
Set torque accel time
Range:0.0
~
6000.0s
Default:0.0s
F10.21
Set torque decel time
Range:0.0
~
6000.0s
Default:0.0s
In torque control, the difference between the motor output torque and the load torque determines
the speed change rate of the motor and load. The motor rotational speed may change quickly and this
will result in noise or too large mechanical stress. The setting of acceleration/deceleration time in
torque control makes the motor rotational speed change softly.
However, in applications requiring rapid torque response, set theacceleration/deceleratio time in
torque control to 0.00s.
For example, two AC drives are connected to drive the same load. To balance the load allocation,
set one AC drive as master in speed control and the other as slave in torque control. The slave
receives the master's output torque as the torque command and must follow the master rapidly. In this
case, the acceleration/deceleration time of the slave in torque control is set to 0.0s.
F10.22
Static friction torque
compensation
Range:0.0
~
100.0%
Default:5.0%
F10.23
Static friction frequency range
Range:0.0
~
20.0Hz
Default:1.0Hz
This parameter takes effect only in torque control. To compensate the static friction of system at
the start, additional torque might be needed. When the motor runs, static friction torque compensation
is disabled. 100% corresponds to rated torque of motor.
F10.24
Static Frequency of Open-Loop
Torque
Range: 1.00
~
10.00Hz
Default:1.00Hz
It is setting the initial frequency that is effective in torque control mode.
F10.25
SVC optimization method
0: Optimization method 0
1: Optimization method 1
2: Optimization method 2
Default:1
Vector control optimization method.
F10.26
Max Frequency source under
torque control
0: Set by F10.18 & F10.19
Default: 0
1:Keypad potentiometer
2:AI1
3:AI2
4:AI3
5: Pulse setting ( DI7/HI )
This parameter takes effect only in torque control. F10.26 is used to set the Max frequency source
under torque control.
F10.27
Start Excitation Current of
Synchronous Motor
0.0
~
150.0%
Default: 50.0%
For synchronous motor control, when starting, give the motor an excitation current to accelerate
the starting process.
F10.28
Flux weakening control of
synchronous motor
0: Invalid
1: Valid
Default: 1
It is suitable for areas above rated frequency of motor.
F10.29
Flux weakening Voltage of
synchronous motor
70.0
~
100.0%
Default: 95.0%
F10.30
Flux weakening gain(Kp) of
0.0
~
500.0%
Default: 50.0%