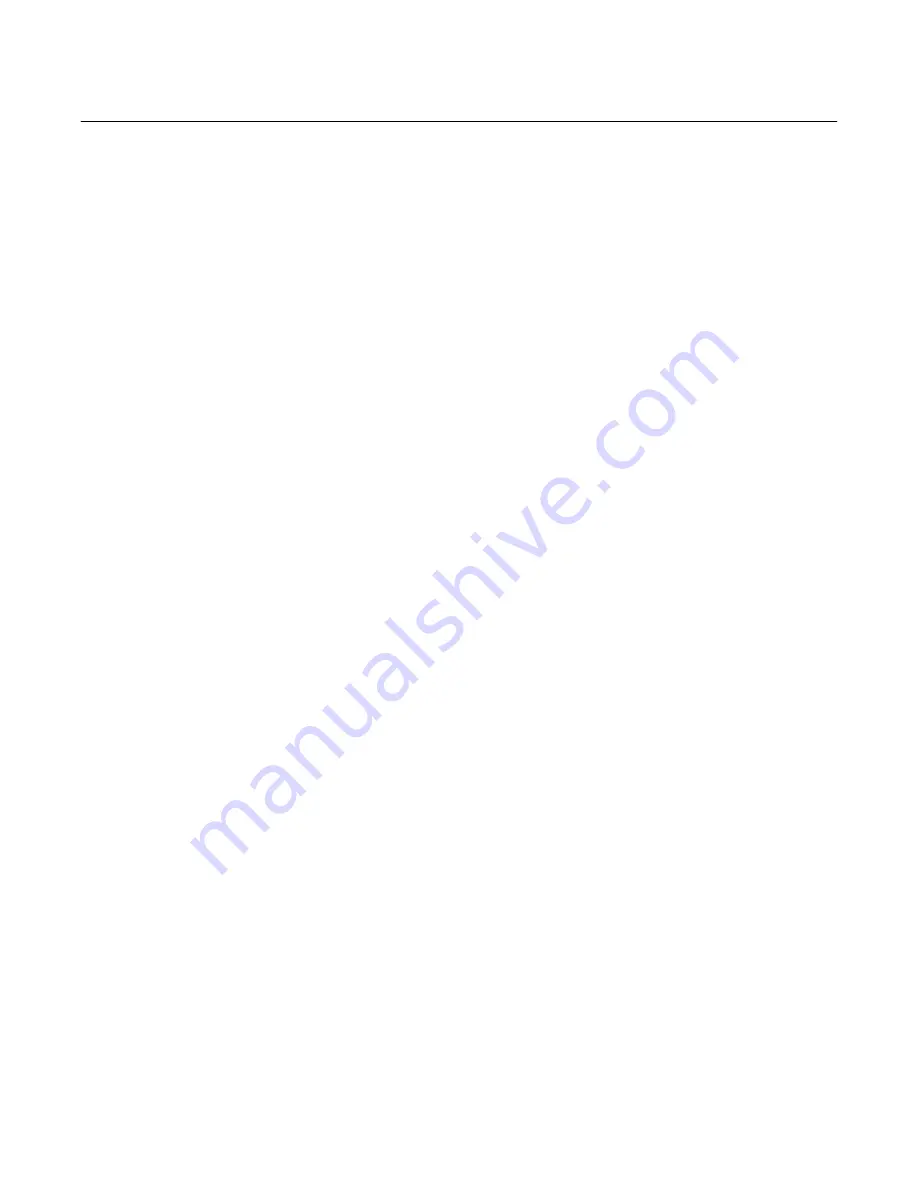
Reference Manual
748384-C
September 2003
1-26 Introduction
Rosemount Analytical Inc. A Division of Emerson Process Management
NGA2000 Reference
1-12 ANALYZER ALGORITHM
The Analog to digital converter is read 30 times
a second. The value is stored as an integer in
the 20 bit range.
There are 2 digital filters: A 7 point median filter
followed by an IIR filter (controlled by the t90
time).
In the zero/span adjust section the raw signal
(the output of the digital filters) is linearly con-
verted to a scale based on the calibration coeffi-
cients (span factor and zero offset) using the
following equation:
Output = SpanFactor * (Input -ZeroOffset)
If the output of the zero/span adjust is between
-0.05 and 1.05 then the value is linearized. A
forth order linearizer is used with the following
formula:
Output = C
0
+ C
1
*Input + C
2
*input
2
+ C
3
*lnput
3
+ C
4
*lnput
4
The output of the linearizer (if used) or the
zero/span adjust is input to the temperature
compensation. The temperature compensation
algorithms is as follows:
TempCompMultiplier = 1 + CaseTempe
TempCompFactor
Output = input + TempCompMultiPlier
This feature is not normally used in the FID.
The output of the temperature compensation
function is multiplied by CALRNGFU to gener-
ate the PVA output. The calibration routine
(which is actually two routines a zero routine
and a span routine) is used to adjust the span
and zero offsets used by the zero/span adjust
routine. It tries to adjust the factors so that
when a 0 ppm gas is read a 0 will be output
from the temperature compensation section and
when a RNGHI ppm. gas is read, 1 will be out-
put from the temperature compensation section.
This is achieved using a successive approxima-
tion technique.
The values of the raw signal from the 20-bit
ADC are typically 520,000 at zero, and some-
where under 900,000 at the highest fullscale
range. The span value is quite variable and it
depends on a series of factors as shown below.
Range fullscale values. In the case of the FID
analyzer only, it sets its PGA gains and its pre-
amplifier gains used based on a rather compli-
cated algorithm. It does this in such a way as to
verify that the maximum signal seen is less than
the fullscale counts for a fullscale gas. The fac-
tors considered are: the range fullscale value;
the response factor (methane or propane, etc.);
the fuel type; the sample gas pressure; and the
type of capillary. These gains are set for each
range, but are not changed dynamically. Earlier
than V2.3 CLDs adjusted their PGA gain based
on the fullscale value, dividing the gain by 2 for
every doubling of range above 100 ppm. Later
CLDs and other analyzers do not use a PGA.
In the case of the FID, the pre-amplifier acts as
a current-to-voltage converter, and its transfer
ratio is selected from two alternatives by choos-
ing either a 200 M or a 5 G feedback resistor.
Following this there is a PGA which can select
its gain from values of 1, 1/2, or 1/4. For meth-
ane and mixed fuel, the preamp changes gain at
a fullscale range of 850 ppm. For methane and
pure hydrogen, the equivalent value is 270 ppm.
These values vary according to the other factors
mentioned. It is not in general possible to say
what scales are used in what ranges, but that
information could be determined from a table.
You can display the main reading at a resolution
of up to seven significant figures (on the plat-
form). The PVA value is transmitted to a PC as
a floating point value, also of about seven sig-
nificant figures of resolution. The PC can dis-
play it according to its programming. This
means that you could display the reading to
hundredths of a ppm if the value of the reading
is less than 99999.99 ppm. However, the noise
level of around 0.1% of reading typically will
make this of questionable value.
Network variables: RAW_SIGNAL, ZERO,
SPAN, LINSTAT, LINA0_, LINA1_, LINA2_,
LINA3_, LINA4_, CALRNGHI, BAROMETER,
CAL_PRESS, CAL_PRESSURE, PVA, PVA-
CEMS