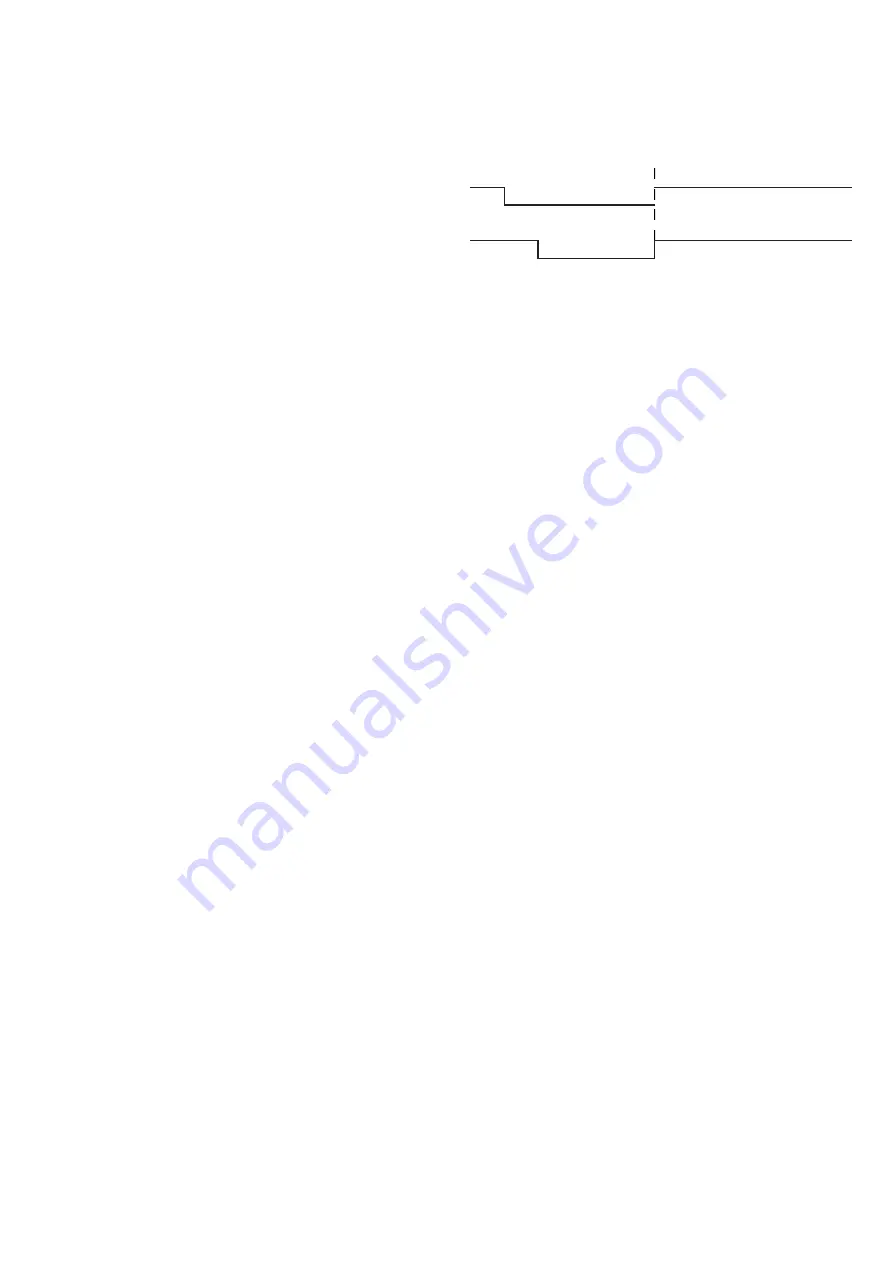
Operation 83/132
RE 30201-B/07.2014, SYEPS series 1X,
Bosch Rexroth AG
Fig. 59: Acknowledging errors
▶
When starting the machine up, adhere to the above switch-on sequence!
▶
Switch on the power supply of the HNC100.
▶
After the ready output OUT 4 was set by the HNC100 the motor can be switched
on.
▶
After the start/delta start-up of the motor, close the accumulator discharge valve
and activate the pressure controller by feeding forward the pressure command
values.
▶
Only when the operating pressure is reached may the valve enable be given by the
PLC. Typically, this takes 2 seconds.
▶
In the standard variant, operating mode 52 must now be called in order to carry
out automatic zero point correction. When this is successfully completed, OUT 7
is set to High. After OUT 7 was set, the enable can be set at input IN 1.
After the valve enable was given, the axes move to the failsafe position. This
position can be freely adjusted for the axes by means of R parameter 443.
When the enable is set at input IN 1 of the HNC100, the axes move to the rest
position of the selected boot mode.
9.1.1 Boot mode
After booting of the HNC100, the latter changes over to the boot mode, which can be
set by means of R parameter 400 “boot mode”. After the enable was withdrawn, the
boot mode is set and the HNC100 is reset to its basic state.
The standard operating
mode for the boot mode is mode 32 “Tool change”. In this operating mode the state
signals that OUT1 is set, the startup is completed, the axis is in position PTE and
ready for operation.
The standard punching system does not feature a boot mode.
After booting, the HNC100 first waits until operating mode 52 is started. With
the standard punching system, this is a precondition for proper functioning of
positioning.
After the HNC100 enable IN1 was set the axis is in closed-loop control in position
PTE or POP.
If IN4 is low, the axis is in PTE; if IN4 is high, the axis is in POP.
An exception is operating mode 32; in this mode the axis is always in position PTE
independently of the status of the IN4.
When the enable IN1 is withdrawn, the axis moves to the upper mechanical stop.
HNC
HNC
HNC OUT4
Ready
IN1 enable after
elimination of the
cause of error
Error condition
Error acknowledged
Acknowledging errors
Advanced/High
Standard