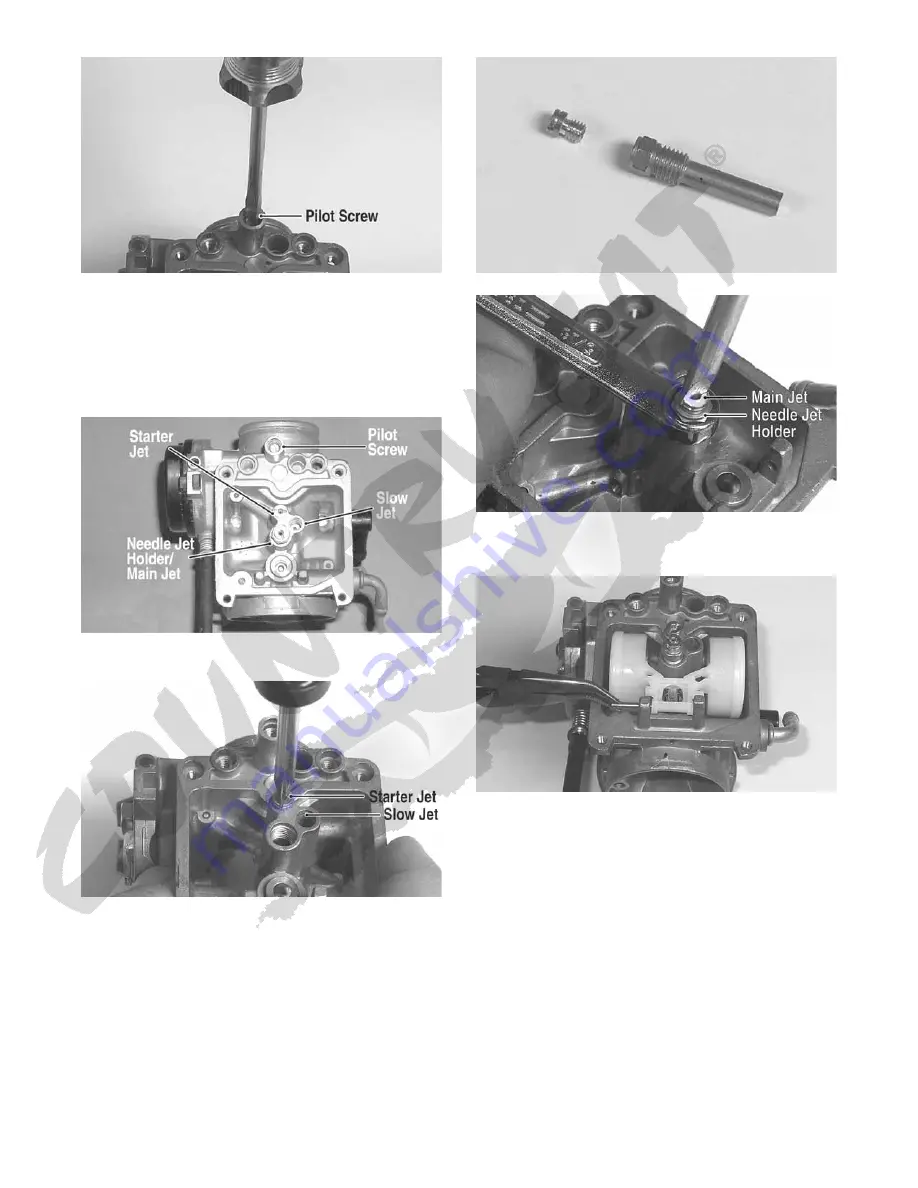
81
KC0028A
NOTE: Turn the pilot screw clockwise until it is
lightly seated; then turn it counterclockwise the rec-
ommended number of turns as an initial setting.
NOTE: Note the locations of the jets and holder dur-
ing assembling procedures.
CC761A
3. Install the starter jet and slow jet. Tighten securely.
KC0032A
4. Install the main jet into the needle jet holder and
tighten securely; then install the needle jet and nee-
dle jet holder assembly into the carburetor and
tighten securely.
KC0031
KC0030A
5. Place the float assembly (with float valve) into posi-
tion and secure to the carburetor with the float pin.
KC0024
NOTE: Check float height by placing the carburetor
on its side w/float contacting the needle; then mea-
sure with a caliper the height when the float arm is in
contact with the needle valve. Float arm height
should be 17 mm.
Содержание 2014 400
Страница 1: ...400 ATV SERVICE MANUAL 2014 ...
Страница 3: ......
Страница 124: ...Printed in U S A Trademarks of Arctic Cat Inc Thief River Falls MN 56701 p n 2259 829 ...