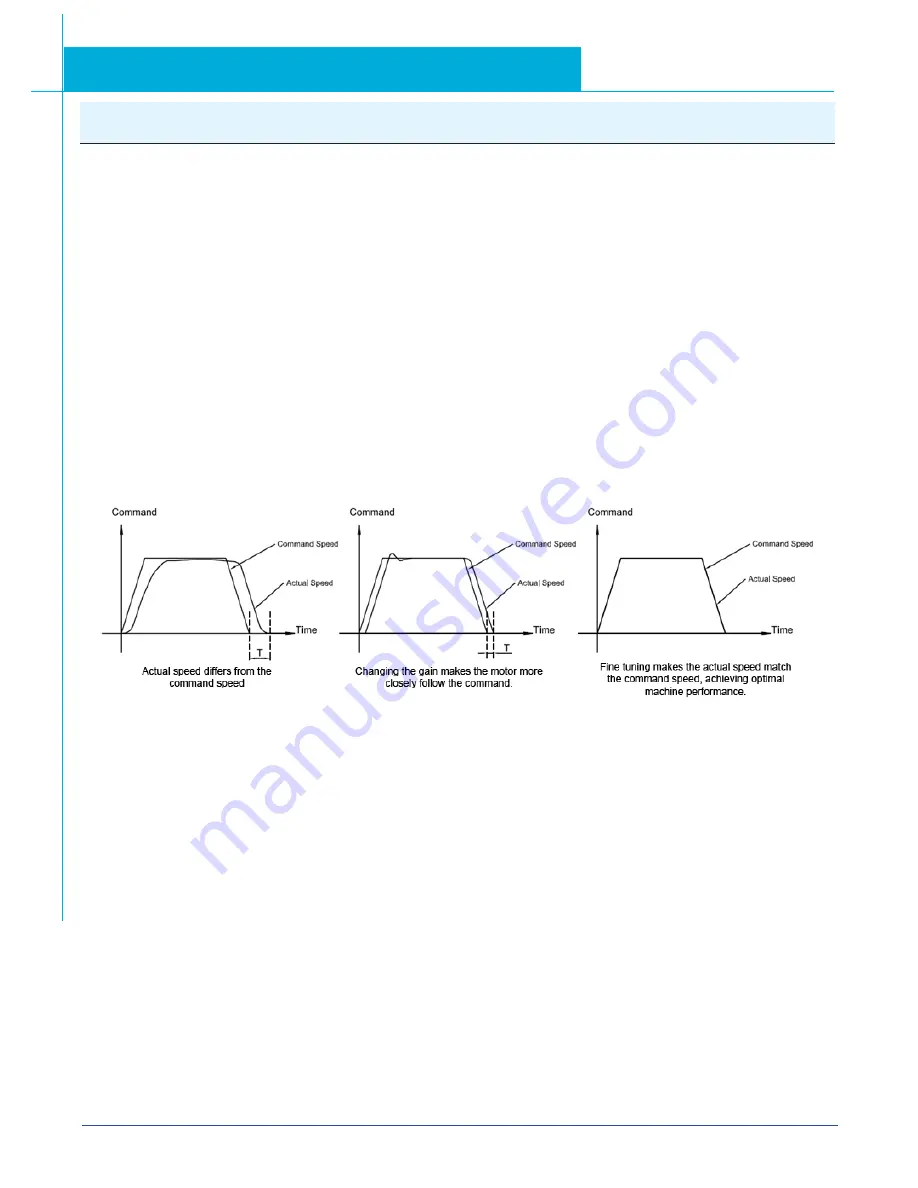
169
SV200 DC Hardware Manual
920-0126A
4/14/2017
11 SV200 Tuning Guide
Like most modern servo drives, the SV200 series employs sophisticated algorithms and electronics for controlling the torque, velocity
and position of the motor and load.
Feedback sensors are used to tell the drive what the motor is doing at all times. That way the drive can continuously alter the voltage
and current applied to the motor until the motor meets the commanded torque, velocity or position, depending on the control mode
selected. This form of control is called “closed loop control.”
One of the loops controls the amount of current in the motor. This circuit requires no adjustment other than specifying the maximum
current the motor can handle without overheating.
The PID loop compares the intended motor position to the actual motor position as reported by the encoder. The difference is called
error, and the PID loop acts on this error with three gain terms: the Proportional term, the Integral term and the Derivative term. The
Acceleration Feedforward term is also added to achieve greater system control.
11.1 Servo Tuning – Adjustment of Gain Parameters
Servo tuning is used to optimize the servo system’s overall performance and reduce system response time. Servo tuning allows
the servo motor to execute host control commands more precisely in order to maximize its system potential. Therefore, it is highly
recommended that the gain parameters be optimized before actual system operation.
The PID loop compares the intended motor position to the actual motor position as reported by the encoder. The difference is called
error. The PID loop acts on this error with these three gain terms: Global gain (KP), Integrator Gain (KI), Derivative gain (KD).
In addition to the PID loop control, the SV200 series drives add a number of extra terms to enable greater system control. These
additional terms include: position loop gain (KF), Damping gain (KV), Inertia feed forward gain (KK), Follow Factor (KL), Derivative
filter gain (KE), and PID filter (KC).
In general, for systems having stiff mechanical transmissions, increasing the servo gain parameters will improve response time. On
the other hand, for systems having more compliant mechanical transmissions, increasing servo gain parameters will potentially cause
system vibrations and reduce system response time.