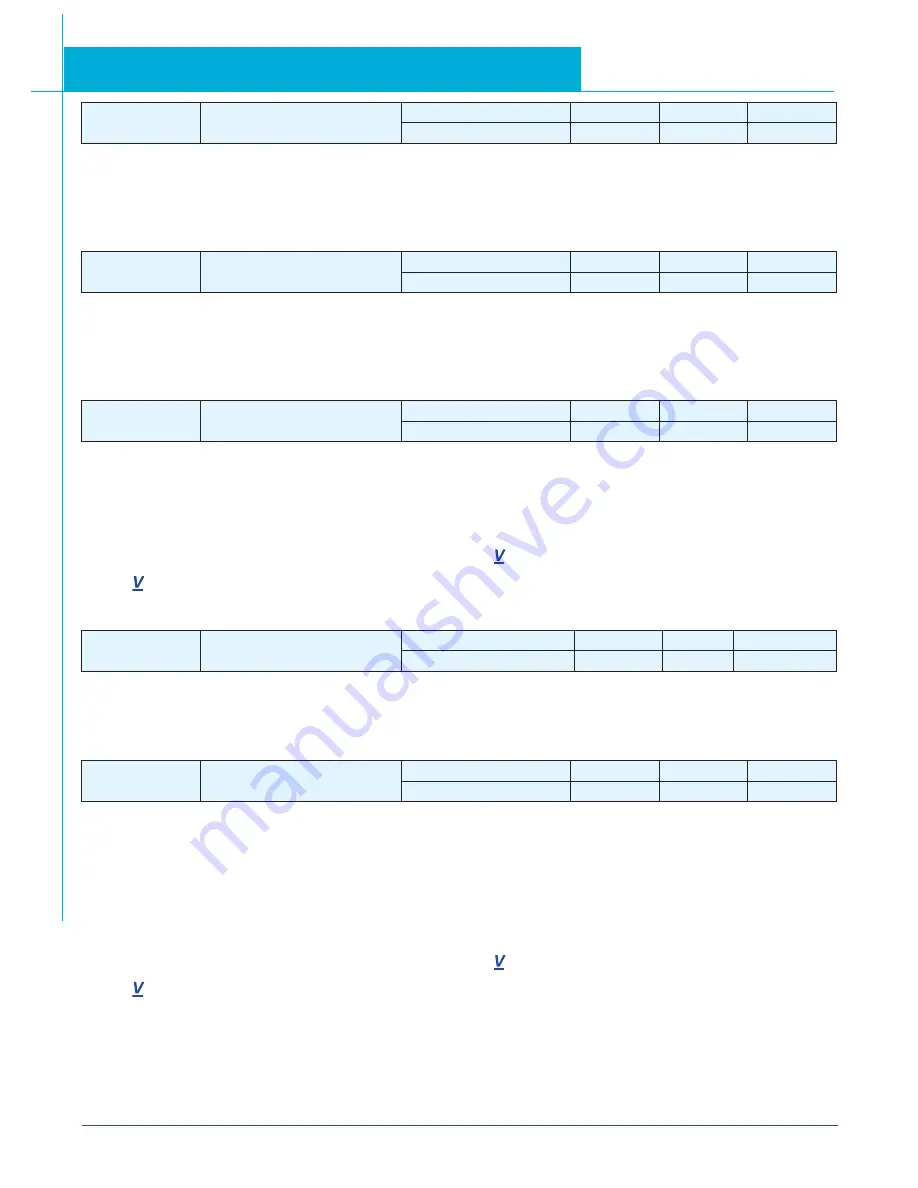
127
SV200 DC Hardware Manual
920-0126A
4/14/2017
P-46 (PD)
In Position Error Range
Data Range
Default
Unit
LED Display
0 - 32000
10
10
This parameter is used to set the in-position error range. For example, motor is in position when the actual position is within the target
In-position error range for the time that is longer than PE specified timing. Then the driver will define the motion as complete or motor
is in-position. Refer to P-47 (PE) and Section 7.2.7 In-Position Error Output.
P-47 (PE)
In Position Duration Count
Data Range
Default
Unit
LED Display
0 - 32000
10
250us
10
PE sets the timing counts for in-range determination. For example, if In-Position error P-46 (PD) is defined, PE sets the time duration
for the test. If In-Position is reached within the time duration, the drive will define the motor as In-Position. Time is counted as
processor cycles, one cycle refers to 250µsec. Refer to Section 7.2.7 In-Position Error Output.
P-48 (TT)
Pulses Input Completion Count
Data Range
Default
Unit
LED Display
0 - 2500
2
ms
16
This parameter is used to define a time duration. It will determine whether the drive has finished receiving all pulses. If the drive
has not receive any pulses for a period longer than TT defined time, then the drive will define no pluses sent to drive. One count is
equivalent to 125µs.
NOTE: if you need to view or set this value on the drive’s control panel, refer to the following calculation:
LED
display
value
=
/ 0.125
Where is time of pulse input completion count unit(ms)
P-49 (AP)
Analog Position Gain
Data Range
Default
Unit
LED Display
-32767 - 32767
8000
counts
DEC
AP sets the analog input gain for motor position when the drive is in analog position command mode. Gain value sets the commanded
position when the analog input is at the configured full scale value.
P-50 (AG)
Analog Velocity Gain
Data Range
Default
Unit
LED Display
-100.000 - 100.000
20.000
rps @+10Vdc
4800
Analog gain value used in analog velocity modes. The gain value is used to establish the relationship between the analog input and the
motor speed in units of 0.25 rpm. For example, if the analog input is scaled to 0 - 5 volt input and the gain is set to 2400, when 5 volts
is read at the analog input the motor will spin at 10 rps.
TIP: To set the analog velocity gain to the desired value, multiply the desired motor speed in rps by 240, or the desired motor speed in
rpm by 4.
NOTE: if you need to view or set this value on the drive’s control panel, refer to the following calculation:
LED
display
value
=
x 240
Where is target velocity setting, Unit is rps (rev/sec).