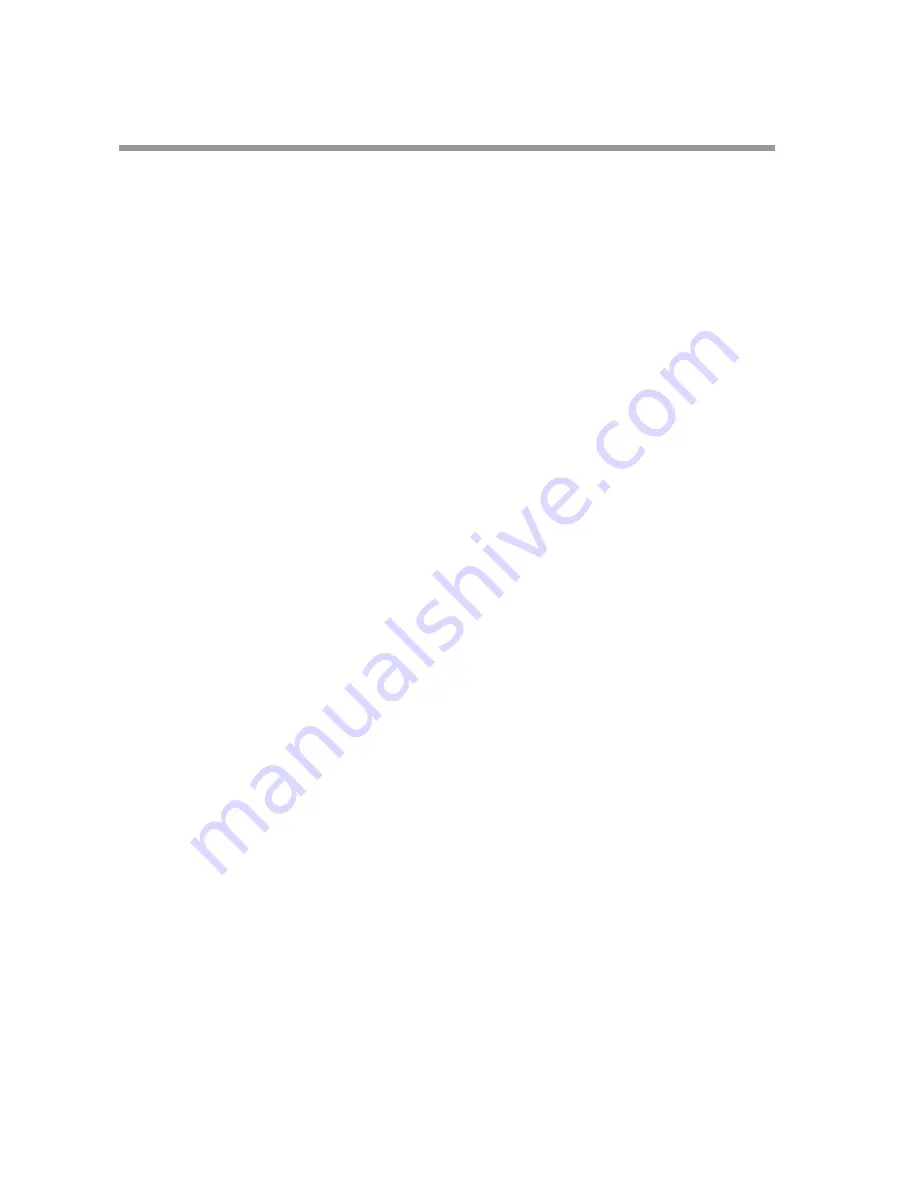
7-44
Chapter 7. PARAMETER SETUP
●
C93 (CPL communications port selection)
・
When set to 0, CPL communications from the loader jack is not possible. In
this case, CPL communications is possible from the addon terminal under
setup
C84
and
C85
communications conditions if the controller model
supports CPL communications.
・
When set to 1 to 15, CPL communications from the loader jack is not possible,
and the
C93
setting becomes the CPL communications address.
Communications conditions are also 4800bps, even parity and 1 stop bit.
In this case, CPL communications is not possible from the addon terminal even
if the controller model supports CPL communications.
・
Use the special cable to connect the RS-232C port on the personal computer
and the loader jack on the equipment.
・
When the setup
C00
(ROM revision) setting indication is 0 or 1, the setup
C93
setting indication cannot be set at "---".
Also, communications from the loader jack is not possible.
・
For details about CPL communications, refer to DigitroniK CPL
Communications "DCP30", Manual No. CP-UM-1760E.