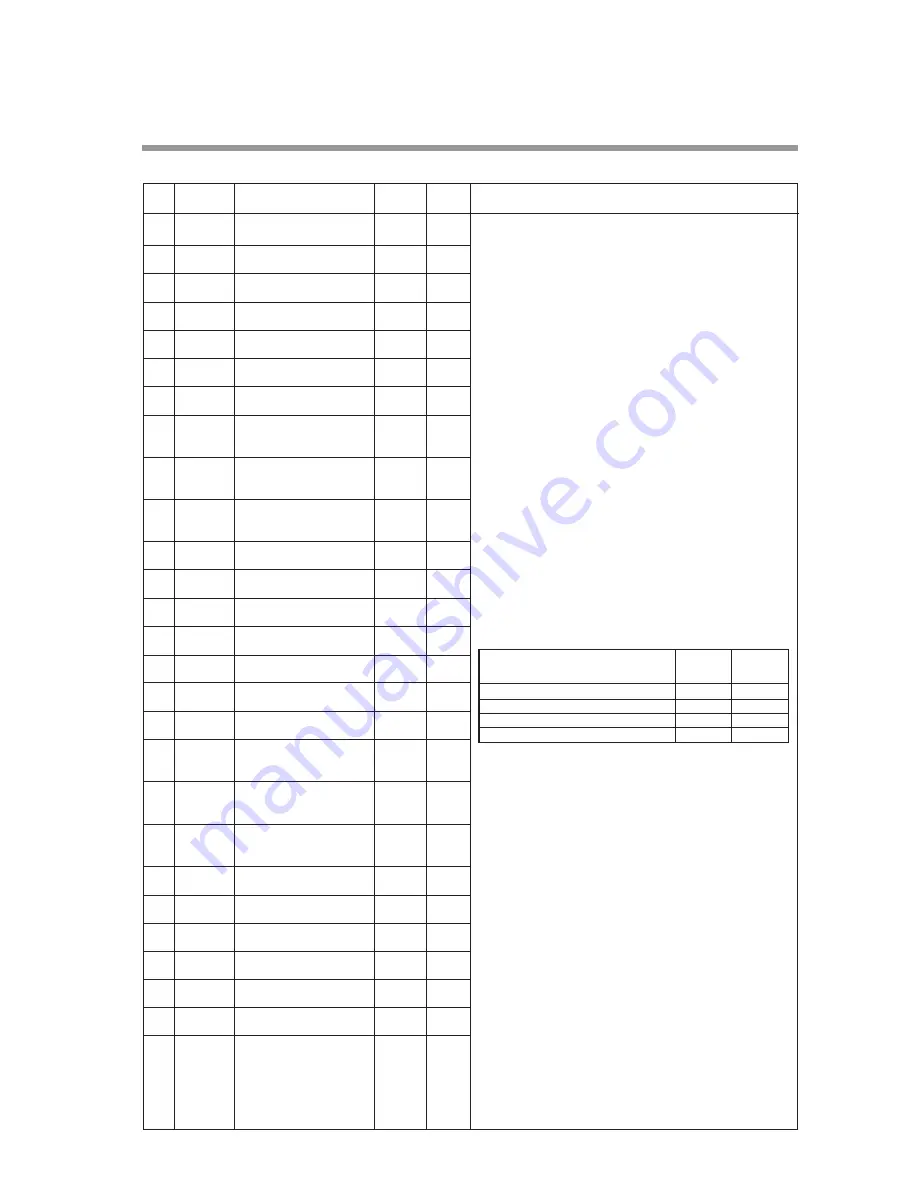
Chapter 7. PARAMETER SETUP
■
PID parameter 1 settings “
PId
”
Setting
P : 0.1 to 999.9%
I
: 0 to 3600 seconds
0 disables integrating action.
d : 0 to 1200 seconds
0 disables derivative action.
oL : -10.0 to +MV upper limit %
oH : MV lower limit to +110.0%
rE : 0.0 to 100.0%
br : 0 to 30
0 disables the brake function.
dP : 0.1 to 999.9%
dI : 1 to 3600 seconds
dd : 0 to 1200 seconds
[Note]
• These parameters are used for control of CH1.
• When variable parameter
m-C setting is 2 (estimated position
control only) on 2G output models when setup data
C44
setting is 0, “- - - -” is displayed for items
oL and oH, and
setting is not possible.
• When
I setting is not 0, “- - - -” is displayed for rE and setting
is not possible.
• When variable parameter
St setting is 0 (smart-tuning
disabled), “- - - -” is displayed for
br and setting is not
possible.
• When variable parameter
2PId setting is 0 (2 degrees of
freedom PID disabled), the items for
dP, dI, dd are not
displayed.
• The following table shows the PID parameter set Nos. that are
used for PID operation on heat/cool models when setup data
C44 setting is 0.
• When variable parameter
2 PID setting is 1 (2 degrees of
freedom PID enabled), the parameter (
P, I, d) ideal for control
when SP changes and the parameter (
dP, dI, dd) ideal for
inhibiting disturbance during settling are automatically
switched.
• Decreasing the proportional band (
P, dP) value improves
controllability. However, it also makes overshoot or hunting
more likely to occur.
Use of the controller on a motor or actuator shortens the
controller’s life. Do not set the proportional band (
P, dP) to too
small a value.
• Decreasing the reset time (
I, dI) improves trackability.
However, it also makes cycling caused by integrating action
more likely to occur.
When
I setting is 0, integrating operation for inhibiting
disturbance also functions.
• Increasing the rate time (
d, dd) allows overshoot to be
inhibited more easily. However, it also make hunting more
likely to occur as the controller reacts to minute changes in
PV.
In a temperature control system, setting the rate time to 1/3 to
1/4 of the integrating time is generally considered to be
appropriate. In a pressure or flow rate control system,
derivative action causes hunting. Either set the
d setting to 0.0
to disable derivative action, or decrease the setting to inhibit
hunting.
No. Item Code
Item
1
P-1
Proportional band
(PID set 1-1)
2
I - 1
Reset time
(PID set 1-1)
3
d - 1
Rate time
(PID set 1-1)
4
oL - 1
MV lower limit
(PID set 1-1)
5
oH - 1
MV upper limit
(PID set 1-1)
6
rE - 1
Manual reset
(PID set 1-1)
7
br - 1
Brake
(PID set 1-1)
8
dP - 1
Disturbance inhibit
proportional band
(PID set 1-1)
9
dI - 1
Disturbance inhibit reset
time
(PID set 1-1)
10
dd - 1
Disturbance inhibit rate
time
(PID set 1-1)
11
P - 2
Proportional band
(PID set 1-2)
12
I - 2
Reset time
(PID set 1-2)
13
d - 2
Rate time
(PID set 1-2)
14
oL - 2
MV lower limit
(PID set 1-2)
15
oH - 2
MV upper limit
(PID set 1-2)
16
rE - 2
Manual reset
(PID set 1-2)
17
br - 2
Brake
(PID set 1-2)
18
dP - 2
Disturbance inhibit
proportional band
(PID set 1-2)
19
dI - 2
Disturbance inhibit reset
time
(PID set 1-2)
20
dd - 2
Disturbance inhibit rate
time
(PID set 1-2)
21
p - 3
Proportional band
(PID set 1-3)
22
I - 3
Reset time
(PID set 1-3)
23
d - 3
Rate time
(PID set 1-3)
24
oL - 3
MV lower limit
(PID set 1-3)
25
oH- 3
MV upper limit
(PID set 1-3)
26
rE - 3
Manual reset
(PID set 1-3)
27
br - 3
Brake
(PID set 1-3)
Factory
Setting
100.0
0
0
0.0
100.0
50.0
0
100.0
120
0
100.0
0.0
0
0.0
100.0
50.0
0
100.0
120
0
100.0
0.0
0
0.0
100.0
50.0
0
User
Setting
PID Set
(cool)
1-2
1-4
1-6
1-8
PID Set
(heat)
1-1
1-3
1-5
1-7
PID Set No. Designated in Program or
Zone No. by PID Set Auto-switching
1
2
3
4
7-25