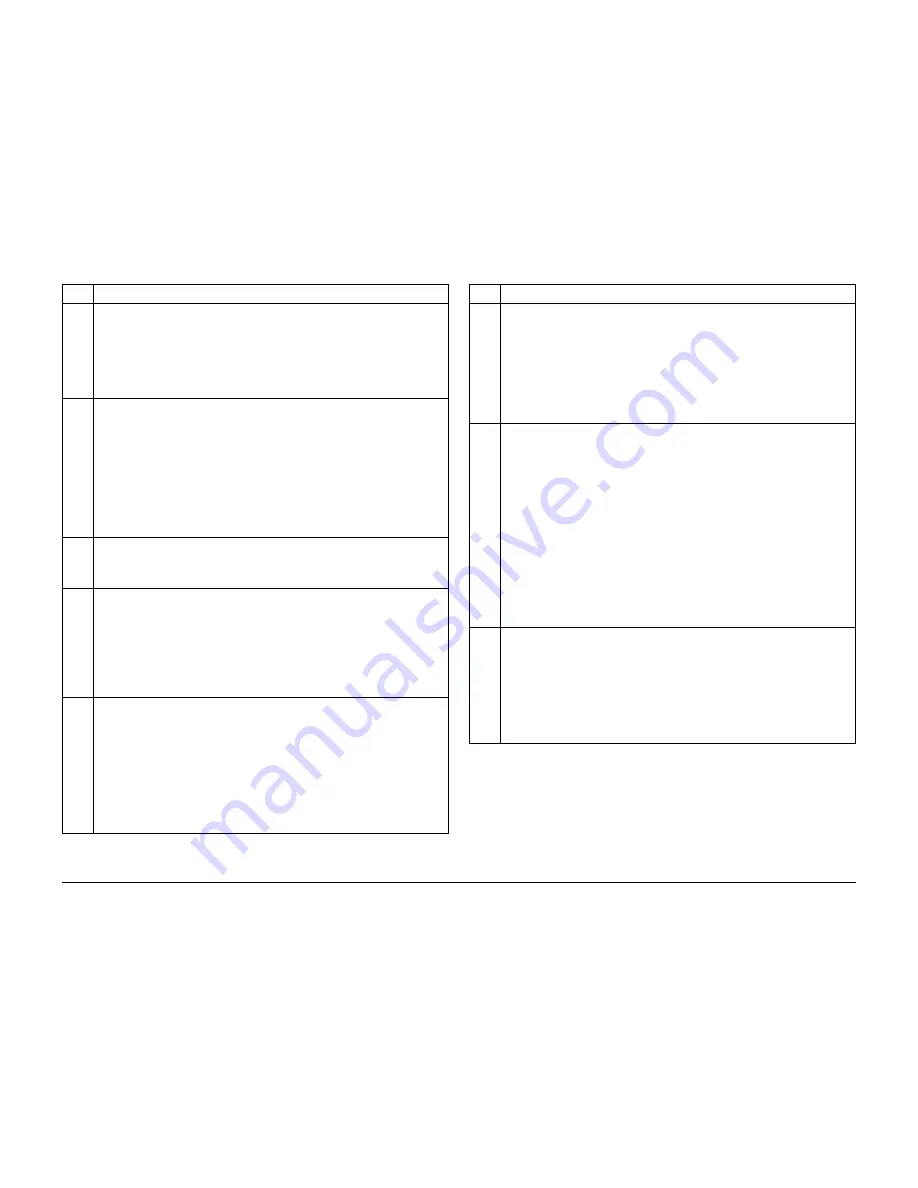
09/2007
2-55
Phaser 8860/8860MFP Service Manual
Jam Codes
Error Messages and Codes
Initial Issue
C2X
Strip flag unexpected event during exit.
1.
Check that the media is not too thick and is supported by the system.
2.
Use a less glossy media.
3.
Check that the guides in the tray are snug against the media.
4.
If the Drum Maintenance Kit is near end of life, replace it.
5.
Clean and inspect the exit rollers.
6.
Test the Paper Path Drive using Service Diagnostics.
C3M
C3N
C3P
C3Q
C3T
The strip flag timed out waiting for the paper picked from Tray 2.
The strip flag timed out waiting for the paper picked from Tray 3.
The strip flag timed out waiting for the paper picked from Tray 4.
The strip flag timed out waiting for the paper picked from Tray 1.
Strip flag time-out during transfix.
1.
Check that the media is the correct size and type for the tray. If envelope jam, try
a different style.
2.
Check the Drum Maintenance Kit for proper operation, replace if necessary.
3.
Check that the Process Drive is correctly homed (
ADJ 4.7.1
).
4.
Test the Stripper Carriage using the Stripper Contact test in Service Diagnostics.
5.
Test the Transfix Drive using the Transfix Drive Slow and Transfix Drive Fast tests.
C3X
Strip flag time-out during exit.
1.
Open the Exit Door and ensure the springs for the idler rollers are present and
installed correctly (they should be the same for all 5 rollers).
2.
Verify the metal bar is installed on top of the Exit Guide.
C5X
Print pulled back into transfix nip during exit.
1.
Check that the media is not too thick and is supported by the system.
2.
Use a less glossy media.
3.
If the Drum Maintenance Kit is near end of life, replace it.
4.
Clean and inspect the exit rollers.
5.
Check that the Process Drive is correctly homed (
ADJ 4.7.1
).
6.
Test the Paper Path Drive using Service Diagnostics.
7.
Replace the Lower Exit Guide.
D2D
D2M
D2N
D2P
D2Q
D2R
D2T
Exit flag unexpected event during warm-up.
The exit flag actuated unexpectedly when paper was picked from Tray 2.
The exit flag actuated unexpectedly when paper was picked from Tray 3.
The exit flag actuated unexpectedly when paper was picked from Tray 4.
The exit flag actuated unexpectedly when paper was picked from Tray 1.
The exit flag actuated unexpectedly when duplexing
The exit flag actuated unexpectedly when transfixing
1.
Check system grounds.
2.
Test the Exit Sensor using Service Diagnostics.
3.
Run the Paper Lead Edge Times test using Service Diagnostics.
4.
Replace the problem component, then retest.
Table 3 Jam Code Troubleshooting
Code Description / Procedure
D2X
The exit flag actuated unexpectedly exit.
1.
Check that the media is not too thick and is supported by the system.
2.
Use a less glossy media.
3.
If the Drum Maintenance Kit is near end of life, replace it.
4.
Clean and inspect the exit rollers.
5.
Check that the Exit Sensor Flag for proper installation or damage. Replace if nec-
essary.
6.
Test the Paper Path Drive using Service Diagnostics.
7.
Replace the problem component.
D3C
D3M
D3N
D3P
D3Q
D3R
D3T
Exit flag time-out during mechanical recovery.
Exit flag timed out following Tray 2 Pick.
Exit flag timed out following Tray 3 Pick.
Exit flag timed out following Tray 4 Pick.
Exit flag timed out following Tray 1 Pick.
Exit flag timed out during duplexing.
Exit flag time-out during transfix.
1.
Check that the media is not too thick and is supported by the system.
2.
Check that the exit path is free of obstructions.
3.
If the Drum Maintenance Kit is near end of life, replace it.
4.
Clean and inspect the Stripper Blade.
5.
Clean and inspect the exit rollers. Check that the rollers rotate freely.
6.
Check the Exit Sensor Flag for proper installation or damage. Replace if neces-
sary.
7.
Test the Paper Path Drive using Service Diagnostics.
8.
Replace the problem component.
E2D
E2E
E2Q
Tray 1 width sensor during warm-up.
Tray 1 width sensor during operation.
Tray 1 width sensor during Tray 1 pick
1.
Check the Tray 1 width guides for proper operation. Verify the guides are not
moving during printing.
2.
Check the Front Door is closed and the wiring is properly connected and seated.
3.
Test the Tray 1 Width Sensor using Service Diagnostics.
4.
Check the Tray 1 wiring to the I/O board.
5.
Replace the I/O Board (
REP 5.0.13
), then retest.
Table 3 Jam Code Troubleshooting
Code Description / Procedure
Summary of Contents for Phaser 8860
Page 1: ...705P01205 September 2007 Phaser 8860 8860MFP Service Documentation...
Page 4: ...09 2007 iv Phaser 8860 8860MFP Service Manual Initial Issue Introduction...
Page 28: ...09 2007 1 2 Phaser 8860 8860MFP Service Manual Initial Issue Service Call Procedures...
Page 34: ...09 2007 2 2 Phaser 8860 8860MFP Service Manual Initial Issue Error Messages and Codes...
Page 94: ...09 2007 3 2 Phaser 8860 8860MFP Service Manual Initial Issue Image Quality...
Page 126: ...09 2007 4 2 Phaser 8860 8860MFP Service Manual Initial Issue Repairs and Adjustments...
Page 208: ...09 2007 5 2 Phaser 8860 8860MFP Service Manual Initial Issue Parts List...
Page 222: ...09 2007 6 2 Phaser 8860 8860MFP Service Manual Initial Issue Diagnostics...
Page 274: ...09 2007 7 2 Phaser 8860 8860MFP Service Manual Initial Issue Wiring Data...
Page 294: ...09 2007 8 2 Phaser 8860 8860MFP Service Manual Initial Issue Theory of Operation...