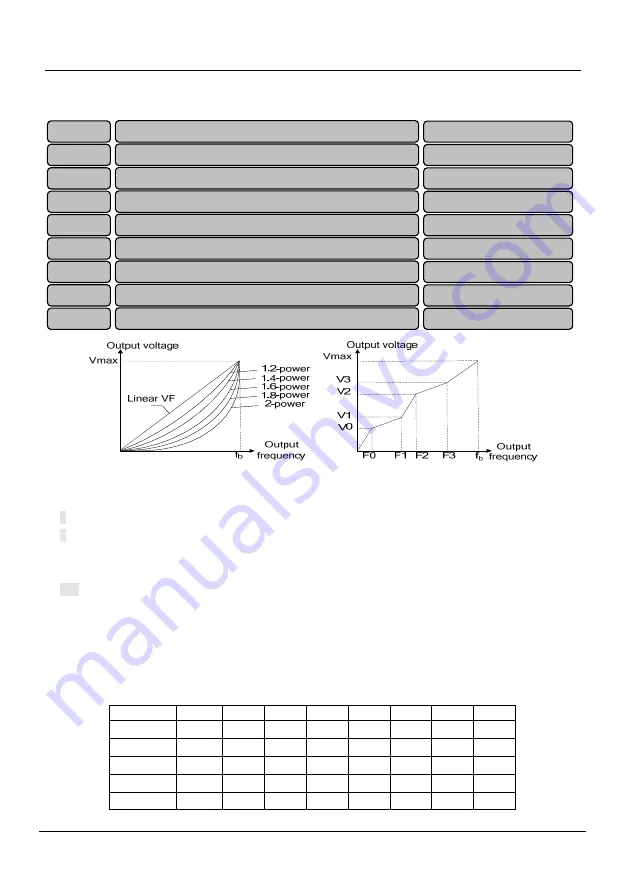
E5 Series High Performance Universal Inverter User’s Manual
Chapter 6 Parameter Descriptions
71
6.5 Multi−step Parameters (Group P4)
Figure 6−TT VTF curve Figure6−T3 Multi−point VTF curve
P4.00 is used to set the VTF curve selection.
0: Linear VF, Applicable to the constant torque load situation.
T: Multi-point VF curve setting by user, applicable to sectional constant torque load.
F0<FT<FT<F3<f
b
f
b
is the motor basic frequency P0.T5
V0≤VT≤VT≤V3≤T00% V0, VT, VT, V3 are the percentage of maximum output voltage P0.TT
T~6: Applicable to the variable torque loads such as fan and pump. When P4.00 is set to T~6, it
corresponds to T.T−power, T.4−power, T.6−power, T.8−power and T-power. The T-power curve is
for water supply and the T.T−power to T.8−power curves are for other liquid media loads. Proper
curve can be selected according to the actual situation.
P4.00=T~6 is valid in E5−A, E5−H−4T**G−63 series.
P4.00=T~6 is invalid in E5−H series, if power curve is needed, use multi-point VTF curve instead.
For settings, refer to the following table.
Power curve
P4.0T
P4.0T
P4.03
P4.04
P4.05
P4.06
P4.07
P4.08
T.T-power
T.00
3.0
T0.00
T6.0
T5.00
44.0
40.00
76.0
T.4-power
T.00
3.0
T0.00
T4.0
T5.00
39.0
40.00
73.0
T.6-power
T.00
3.0
T0.00
T3.0
T5.00
35.0
40.00
70.0
T.8-power
T.00
3.0
T0.00
TT.0
T5.00
3T.0
40.00
67.0
T-power
T.00
3.0
T0.00
TT.0
T5.00
T8.0
40.00
64.0
0.0 ~ T00.0 %( T00.0%)
Multi-point VTF voltage V3
P4.08
0.00 ~ 300.00 Hz (50.00Hz)
Multi-point VTF frequency F3
P4.07
0.0 ~ T00.0 %( 50.0%)
Multi-point VTF voltage VT
P4.06
0.00 ~ 300.00 Hz (T5.00Hz)
Multi-point VTF frequency FT
P4.05
0.0 ~ T00.0 %( T0.0%)
Multi-point VTF voltage VT
P4.04
0.00 ~ 300.00 Hz (T0.00Hz)
Multi-point VTF frequency FT
P4.03
0.0 ~ T00.0 %( 3.0%)
Multi-point VTF voltage V0
P4.0T
0.00 ~ 300.00 Hz (T.00Hz)
Multi-point VTF frequency F0
P4.0T
0 ~ 6(0)
VTF curve selection
P4.00
Summary of Contents for E5 Series
Page 1: ...E5 Series High Performance Universal Inverter USER S MANUAL E5 Series USER S MANUAL ...
Page 7: ...vi T Setting Process for Open Loop ...
Page 8: ...vii Open loop setting process continued ...
Page 9: ...viii 3 Setting Process for Closed Loop ...
Page 10: ...ix Setting Process for Closed Loop continued ...