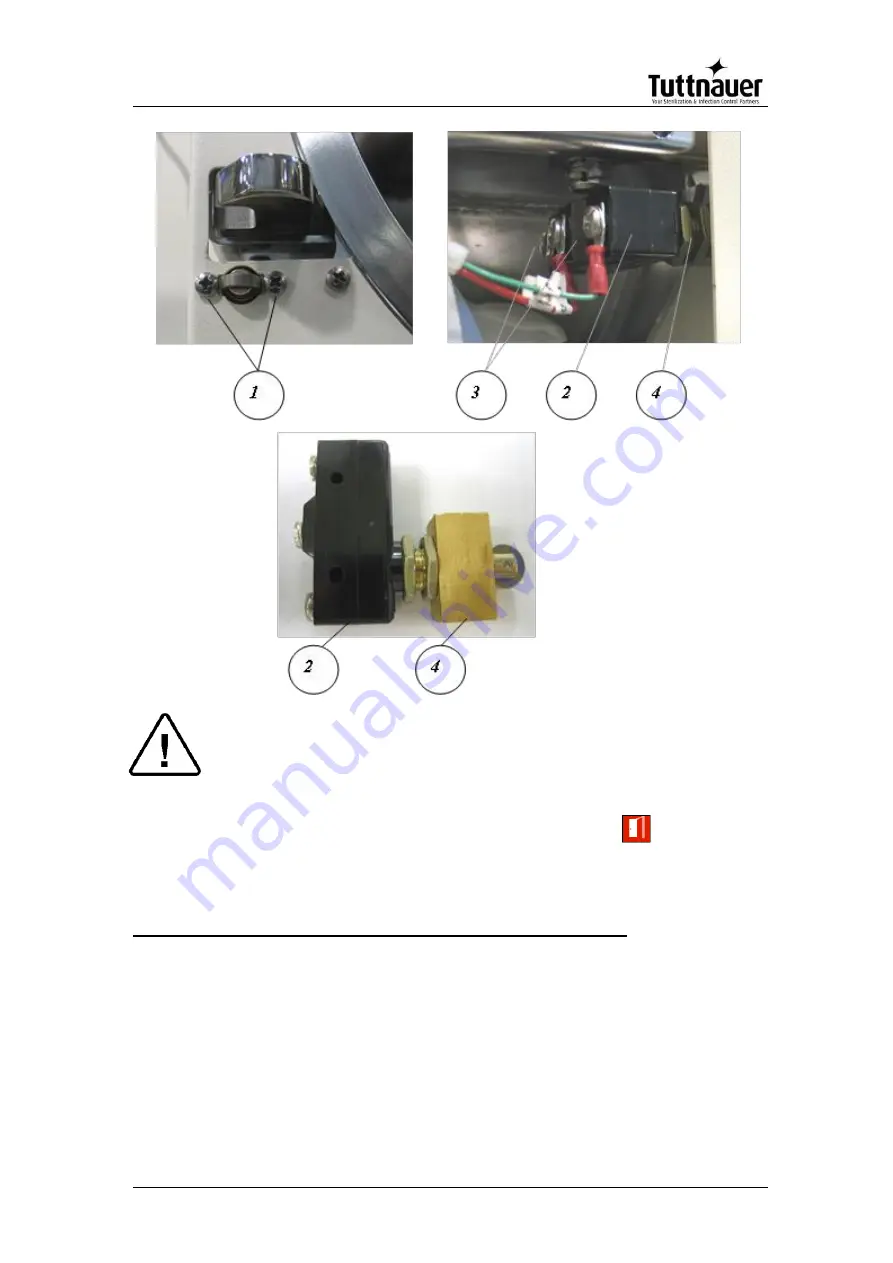
Page 105
Caution!
Make sure that the door switch is installed correctly!
Check that the operational message “Door is Open"
is displayed
when the door is opened and that the message disappears when the door
is closed.
10.15
Replacing the Solid State Relay (SSR)
1. Remove the Control System (see ).
2. Disconnect the AC (1) and DC (3) connectors.
3. Unscrew the screws connecting the SSR to the control system base (2).
4. Disassemble the SSR from the base.
5. Replace the SSR with the new one.
6. Restore the connections (1,2, 3).
7. Assemble the new SSR with two screws (2).
www.shanghaidelan.com 021-54263653
Summary of Contents for ELARA11-D
Page 163: ...Page 162 Piping Diagram w w w s h a n g h a i d e l a n c o m 0 2 1 5 4 2 6 3 6 5 3...
Page 164: ...Page 163 w w w s h a n g h a i d e l a n c o m 0 2 1 5 4 2 6 3 6 5 3...
Page 165: ...Page 164 w w w s h a n g h a i d e l a n c o m 0 2 1 5 4 2 6 3 6 5 3...
Page 166: ...Page 165 w w w s h a n g h a i d e l a n c o m 0 2 1 5 4 2 6 3 6 5 3...
Page 167: ...Page 166 w w w s h a n g h a i d e l a n c o m 0 2 1 5 4 2 6 3 6 5 3...
Page 168: ...Page 167 w w w s h a n g h a i d e l a n c o m 0 2 1 5 4 2 6 3 6 5 3...
Page 169: ...Page 168 Electric Diagram w w w s h a n g h a i d e l a n c o m 0 2 1 5 4 2 6 3 6 5 3...
Page 170: ...Page 169 w w w s h a n g h a i d e l a n c o m 0 2 1 5 4 2 6 3 6 5 3...
Page 171: ...Page 170 w w w s h a n g h a i d e l a n c o m 0 2 1 5 4 2 6 3 6 5 3...
Page 172: ...Page 171 w w w s h a n g h a i d e l a n c o m 0 2 1 5 4 2 6 3 6 5 3...
Page 173: ...Page 172 w w w s h a n g h a i d e l a n c o m 0 2 1 5 4 2 6 3 6 5 3...
Page 174: ...Page 173 w w w s h a n g h a i d e l a n c o m 0 2 1 5 4 2 6 3 6 5 3...
Page 175: ...Page 174 w w w s h a n g h a i d e l a n c o m 0 2 1 5 4 2 6 3 6 5 3...
Page 176: ...Page 175 w w w s h a n g h a i d e l a n c o m 0 2 1 5 4 2 6 3 6 5 3...