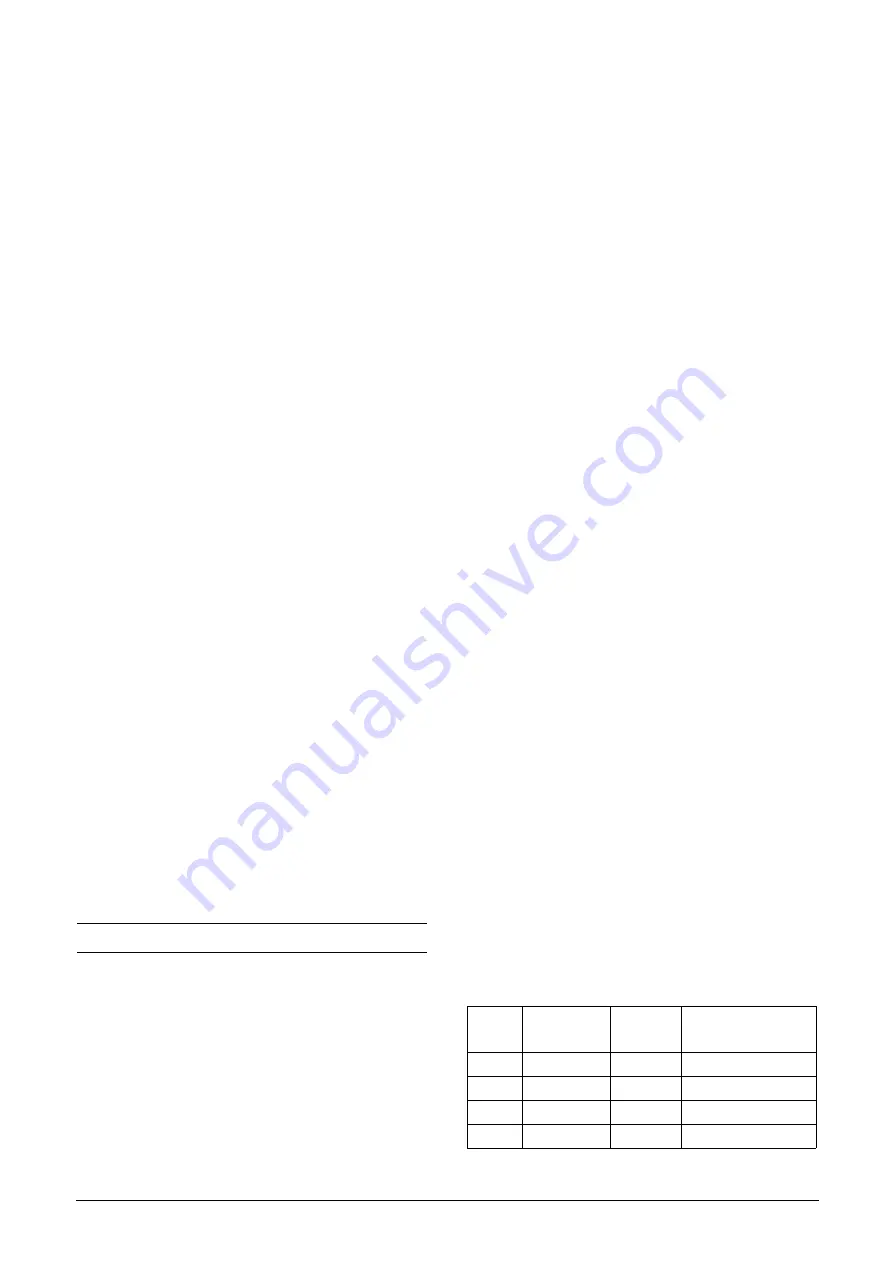
34
Main Features
and DigIn 4 and DigIn 5 for selecting the parameter
sets.
Bottling machine with 3 different products
Use 3 parameter sets for 3 different Jog reference
speeds when the machine needs to be set up. The 4th
parameter set can be used for “normal” remote control
when the machine is running at full production.
Manual - automatic control
If in an application something is filled up manually and
then the level is automatically controlled using PID reg-
ulation, this is solved using one parameter set for the
manual control and one for the automatic control.
7.1.1 One motor and one parameter
set
This is the most common application for pumps and
fans.
Once default motor M1 and parameter set A have been
selected:
1. Enter the settings for motor data.
2. Enter the settings for other parameters e.g. inputs
and outputs
7.1.2 One motor and two parameter
sets
This application is useful if you for example have a
machine running at two different speeds for different
products.
Once default motor M1 is selected:
1. Select parameter set A in menu [241].
2. Enter motor data in menu [220].
3. Enter the settings for other parameters e.g. inputs
and outputs.
4. If there are only minor differences between the set-
tings in the parameter sets, you can copy parameter
set A to parameter set B, menu [242].
5.
Enter the settings for parameters e.g. inputs and
outputs.
7.1.3 Two motors and two parameter
sets
This is useful if you have a machine with two motors
that can not run at the same time, such as a cable
winding machine that lifts up the reel with one motor
and then turns the wheel with the other motor.
One motor must stop before changing to an other
motor.
1. Select parameter set A in menu [241].
2. Select motor M1 in menu [212].
3. Enter motor data and settings for other parameters
e.g. inputs and outputs.
4. Select parameter set B in menu [241].
5. Select M2 in menu [212].
6. Enter motor data and settings for other parameters
e.g. inputs and outputs.
7.1.4 Autoreset at trip
For several non-critical application-related failure condi-
tions, it is possible to automatically generate a reset
command to overcome the fault condition. The selec-
tion can be made in menu [250]. In this menu the max-
imum number of automatically generated restarts
allowed can be set, see menu [251], after this the VSD
will stay in fault condition because external assistance
is required.
Example
The motor is protected by an internal protection for ther-
mal overload. When this protection is activated, the
VSD should wait until the motor is cooled down enough
before resuming normal operation. When this problem
occurs three times in a short period of time, external
assistance is required.
The following settings should be applied:
• Insert maximum number of restarts; set menu [251]
to 3.
• Activate Motor I
2
t to be automatically reset; set
menu [25A] to 300 s.
• Set relay 1, menu [551] to AutoRst Trip; a signal will
be available when the maximum number of restarts
is reached and the VSD stays in fault condition.
• The reset input must be constantly activated.
7.1.5 Reference priority
The active speed reference signal can be programmed
from several sources and functions. The table below
shows the priority of the different functions with
regards to the speed reference.
Note: Do not change motor data in parameter set B.
Table 18
Reference priority
Jog
Mode
Preset
Reference
Motor Pot
Ref. Signal
On/Off
On/Off
On/Off
Option cards
On
On/Off
On/Off
Jog Ref
Off
On
On/Off
Preset Ref
Off
Off
On
Motor pot commands
Summary of Contents for F33 Series
Page 1: ...TECO F33 Variable Speed Drive Instruction manual English Software version 4 2X...
Page 3: ......
Page 33: ...30 Getting Started...
Page 51: ...48 Main Features...
Page 53: ...50 EMC and Machine Directive...
Page 59: ...56 Operation via the Control Panel...
Page 65: ...62 Serial communication...
Page 159: ...156 Troubleshooting Diagnoses and Maintenance...
Page 165: ...162 Options...
Page 179: ...176 Technical Data...
Page 187: ...184 Menu List...