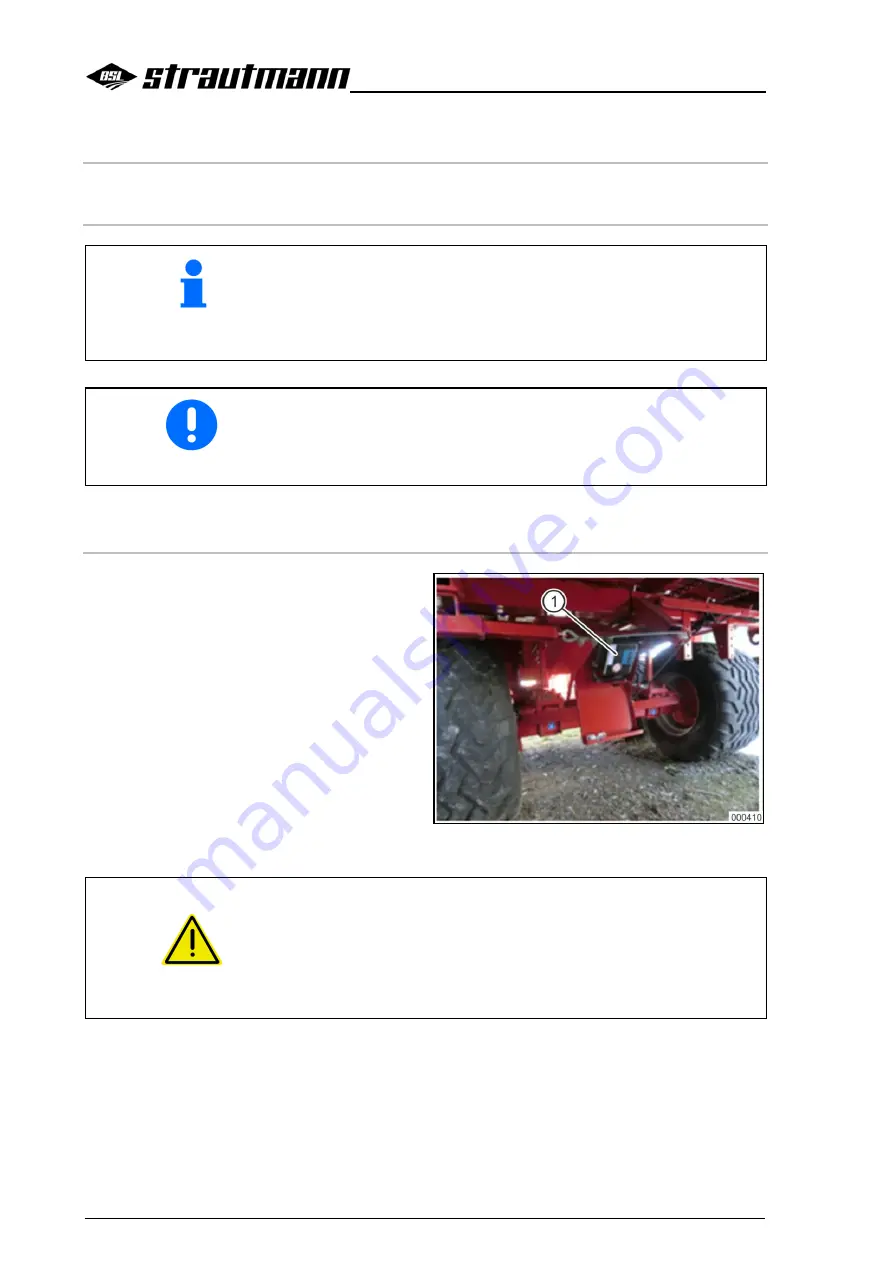
Operation
207
Giga-Vitesse CFS 3602 - 4402, Giga-Vitesse CFS 3602 DO - 4402 DO 03.18
6.3
Steering
6.3.1
Operation of steering computer
Usually, you have to make use of the steering computer only:
•
for error diagnosis during operation, see chapter "Display in
case of trouble".
•
for read-out of the fault memory, see chapter "Read out fault
memory"(service menu "alarm memory“)".
The steering computer is permanently supplied with power, even
after the control set has been switched off.
Therefore, always pull the plug for the power supply out after
completion of work.
6.3.1.1
Access to steering computer
The steering computer is mounted behind a
protective cover (1) beneath the machine.
Fig. 86
WARNING
Risk of injury due to movements of the machine or its working
tools when operating the steering computer!
Secure tractor and machine against accidental starting, rolling and
actuation, before accessing the steering computer!
In particular, lock the driver's cabin of the tractor, as the ignition
must be switched on when operating the steering computer.
Summary of Contents for Giga-Vitesse CFS 3602
Page 2: ......
Page 4: ...Bad Laer den 26 03 2018 Dipl Kfm W Strautmann Managing Director...
Page 306: ...Circuit diagrams Giga Vitesse CFS 3602 4402 Giga Vitesse CFS 3602 DO 4402 DO 03 18 306 Fig 174...
Page 309: ...Circuit diagrams 309 Giga Vitesse CFS 3602 4402 Giga Vitesse CFS 3602 DO 4402 DO 03 18...
Page 310: ...Circuit diagrams Giga Vitesse CFS 3602 4402 Giga Vitesse CFS 3602 DO 4402 DO 03 18 310...
Page 313: ...Circuit diagrams 313 Giga Vitesse CFS 3602 4402 Giga Vitesse CFS 3602 DO 4402 DO 03 18...
Page 314: ...Circuit diagrams Giga Vitesse CFS 3602 4402 Giga Vitesse CFS 3602 DO 4402 DO 03 18 314...
Page 317: ...Circuit diagrams 317 Giga Vitesse CFS 3602 4402 Giga Vitesse CFS 3602 DO 4402 DO 03 18...
Page 318: ...Circuit diagrams Giga Vitesse CFS 3602 4402 Giga Vitesse CFS 3602 DO 4402 DO 03 18 318...
Page 320: ...Circuit diagrams Giga Vitesse CFS 3602 4402 Giga Vitesse CFS 3602 DO 4402 DO 03 18 320...
Page 326: ......