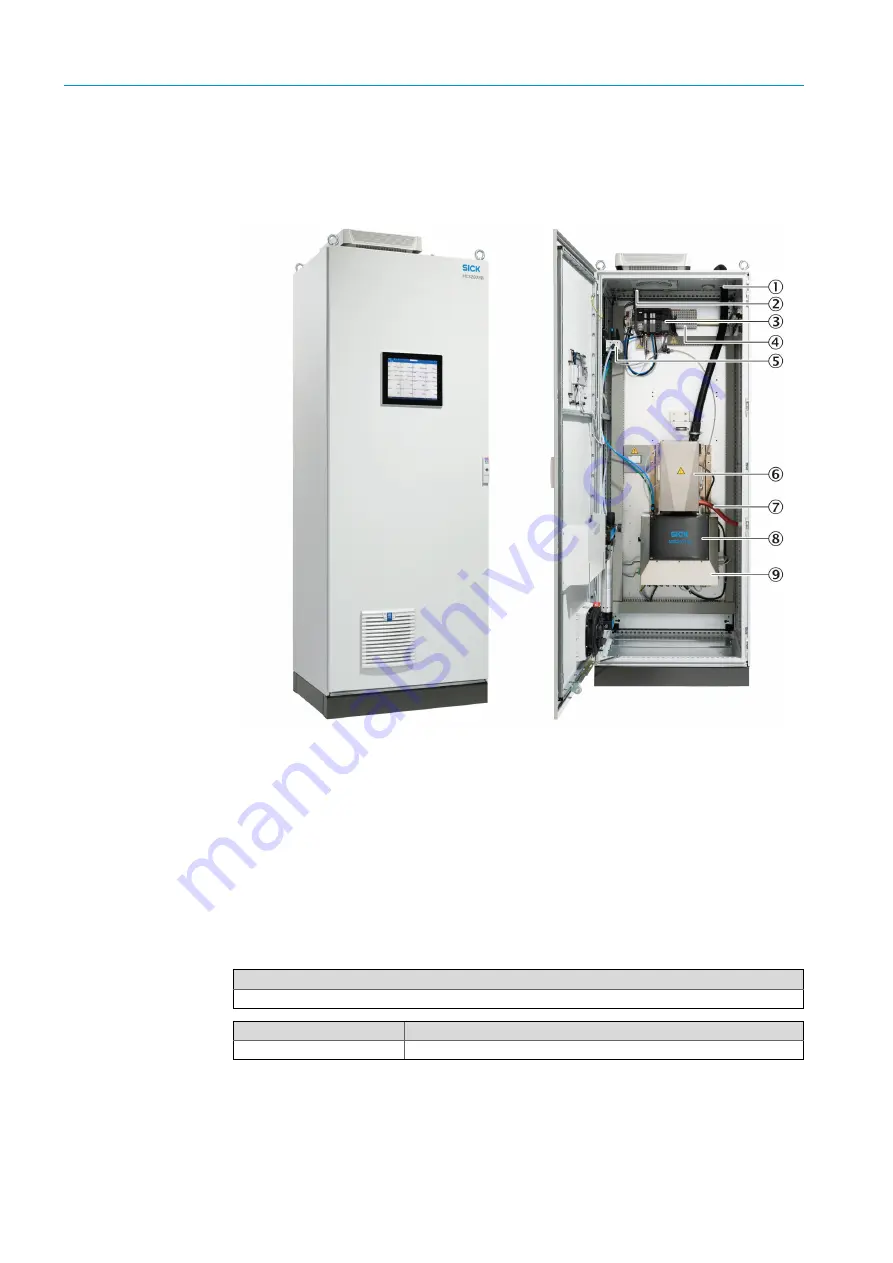
52
8024638/AE00/V1-0/2019-09| SICK
S E R V I C E M A N U A L | MCS200HW
Subject to change without notice
5
REPAIRS
5
Repairs
5.1
Working on the device cabinet
Fig. 59: Equipment cabinet, inside
5.1.1
Replacing the door fan
1
Disconnect the MCS200HW power supply.
2
Disconnect the power supply of the door fan.
1
Heated sample gas line
2
Roof ventilator
3
Valve manifold
4
IO modules
5
Pressure reducer unit
6
Cell
7
Test gas line
8
Sender/receiver unit
9
Electronics unit
Tools required
Phillips screwdriver
Spare parts set No.
Contents
6048627
Door fan