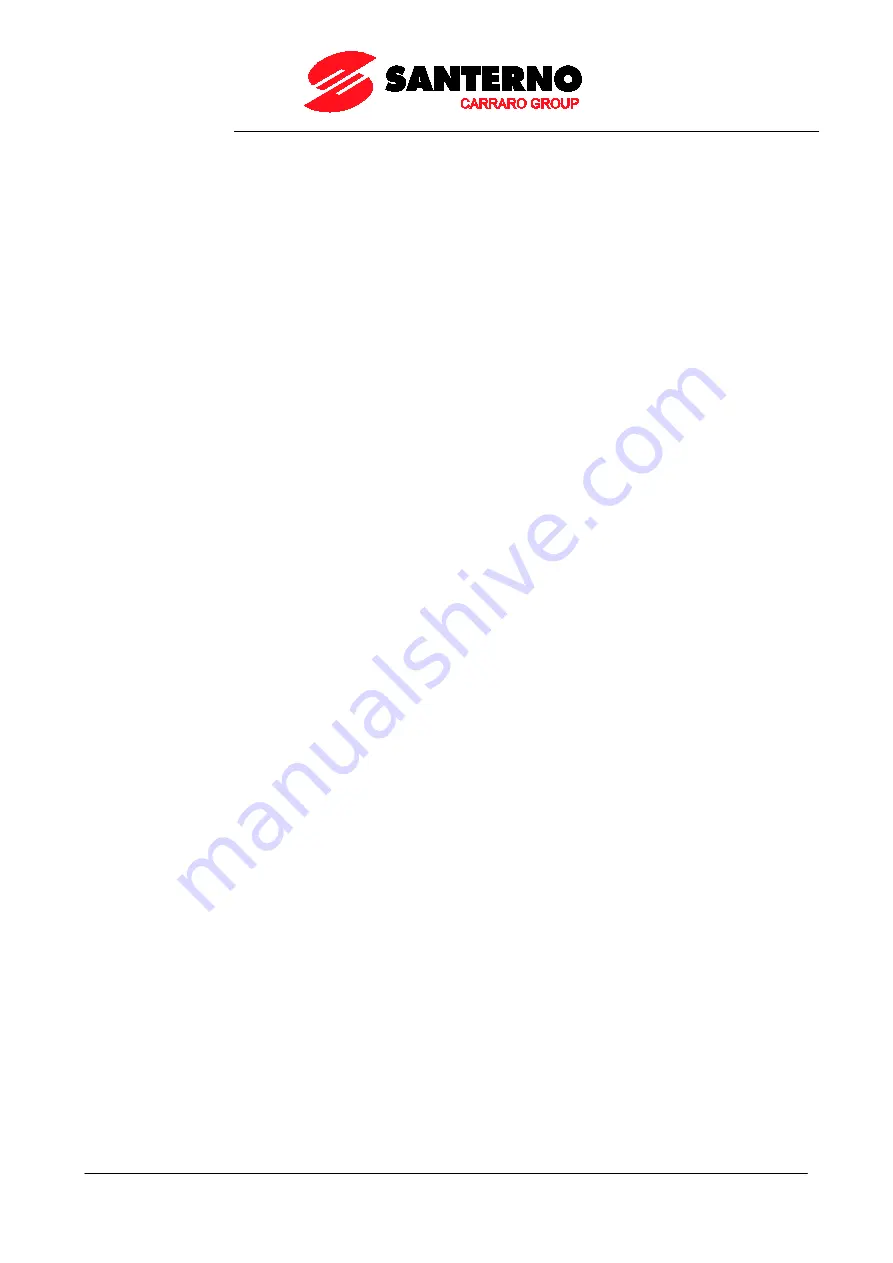
SINUS PENTA
PROGRAMMING GUIDE
48
/
486
Close the
ENABLE-A
and
ENABLE-B
commands and wait until tune is complete (Warning
“
W32
Open Enable” is displayed).
The drive has now computed and saved the following parameter values:
-
P175t1
(proportional gain of the current control) through motor measurements.
-
P175u1
(integral time of the current control) through motor measurements.
If alarm “
A065
Autotune KO” trips, this means that the
ENABLE-A
and
ENABLE-B
commands
have opened before autotune was complete or the autotune algorithm has failed within the
preset timeout. In that case, reset the drive sending a command from terminal MDI3, or press
the
RESET
key in the display/keypad and perform the autotune procedure again.
8) Overload:
Set parameter
C048
in the LIMITS MENU based on the maximum torque that can be generated
expressed as a percentage of the motor rated torque.
9) Start up:
Activate the
ENABLE-A
input (terminal 15),
ENABLE-B
(terminal S) and the
START
input
(terminal 14) and send a speed reference. The
RUN
LED and
REF
LED will come on and the
motor will start. Make sure that the motor is rotating in the correct direction. If not, set
parameter
C014
(Phase Rotation) = [1:Yes], or open the
ENABLE-A
,
ENABLE-B
and
START
inputs, remove voltage from the drive and, after waiting at least 20 minutes, swap two of the
motor phases.
10) Speed regulator
adjustment:
If overshoot occurs when the speed setpoint is attained or if a system instability is detected
(jerking), adjust the parameters relating to the speed loop (SPEED LOOP AND CURRENT
BALANCING MENU). Set the two parameters relating to integral time (
P125, P126
) as
[Disabled] and set low values for the parameters relating to proportional gain (
P128, P129
). Set
equal values for
P128
and
P129
and increase them equally until overshoot takes place when
the setpoint is attained. Decrease
P128
and
P129
by approx. 30%, then decrease the high
values set for integral time in
P125
and
P126
(keep both values equal) until an acceptable
setpoint response is obtained. Check to see if the motor runs smoothly at constant speed.
11) Possible failures:
If alarm “
A060
Fault No Curr.” trips, this means that the current loop is not properly tuned.
Follow the instructions given in step 6 and decrease the value of
I
0
(parameter
C021
in the
If the motor is noisy when starting, this means that the rotor time constant is not correct.
Follow the instructions given in step 7a) or 7b) again, or manually change the value of the rotor
time constant (parameter
C025
) for a smooth motor startup.
If no failure occurred, go to step 7. Otherwise, check the drive connections paying particular
attention to supply voltages, DC link and input reference. Also check if alarm messages are
displayed. In the Motor Measures Menu, check the speed reference (
M000
), the reference
speed processed by the ramps (
M002
), the supply voltage of the control section (
M030
), the
DC link voltage (
M029
), the condition of the control terminals (
M033
). Check to see if these
readouts match with the measured values.
12)
Additional
parameter
modifications:
For the optimization of the motor performance, adjust parameters
C021
(no-load current),
C024
(mutual inductance),
C025
(rotor time constant). Consider the following:
•
C021
Too high values
→
Lower torque, especially at rated speed, because most
part of the voltage imposed by the drive is used to magnetize the motor instead of
generating a proper motor torque;
•
C021
Too low values
→
Because of the motor flux weakening, higher current
ratings are needed;
•
C024
Mutual inductance
→
This is computed each time the no-load current level is
changed. This is not binding for the motor control, but strongly affects the correct
estimation of the output torque; in case of overestimation, decrease
C024
, and vice
versa;
•
C025
Optimum value
→
To obtain the optimum value of the rotor time constant, the
best way consists in performing several attempts with a constant load but with
different values of
C025
. The optimum value is the one ensuring to obtain the output
torque with the lower current (see
M026
).
When parameter
P003
= Standby Only (condition required for changing C parameters), you
can change
Cxxx
parameters in the CONFIGURATION menu only when the drive is
DISABLED or STOPPED, whereas if
P003
= S Fluxing, you can change
Cxxx
parameters when the motor is stopped but the drive is enabled.
You can write down any custom parameters in the table provided on the last pages of this
Programming Guide (CUSTOM PARAMETERS).