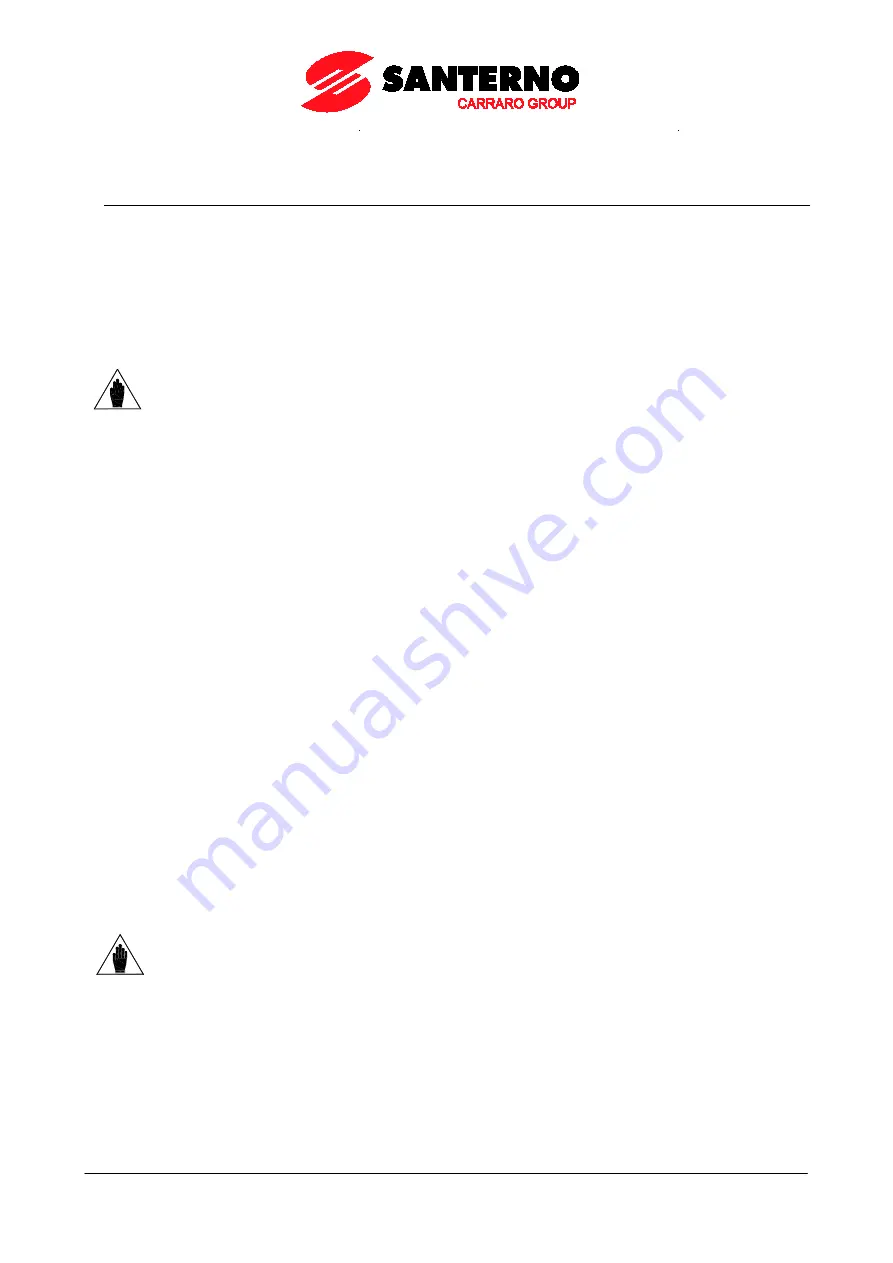
SINUS PENTA
GUIDA ALLA
PROGRAMMAZIONE
358
/
486
39. BRAKING
AND
RAMP
EXTENSION
MENU
39.1.
Overview
The Braking and Ramp Extension Menu enables the clamp transistor command and sets its max. duty cycle for the drive
braking resistance. If no braking resistance is installed, promptness of the DC bus voltage control can be adjusted in
order to avoid OVERVOLTAGE alarm, causing abrupt deceleration. Special parameters are available, enabling
controlling actions to limit DC bus voltage increase due to motor load variation.
39.1.1.
B
RAKING MODULE AND RAMP EX T ENSION
To enable the clamp transistor command for the braking resistance, set
C210=[With resistor]
. In this operating mode,
when DC bus voltage exceeds a preset threshold value depending on the drive voltage class, the clamp transistor
closes in the braking resistor, so energy in excess is dissipated to the resistor and DC bus voltage does not exceed
voltage ratings.
The max. duty cycle of the braking resistor is parameterized with
C212
and
C211
: maximum duty cycle (100 * Ton /
(Ton+Toff) [%] ) and maximum time of continuous supply (Ton) respectively. If the braking resistor activation is Ton =
C212
, when this interval is over, the relevant command will be disabled for a time equal to Toff = (100 –
C212
) *
C211
/
C212
[sec].
Example
:
A lifting application featuring a Sinus Penta 0086 at 400V requires a braking resistor with a 50% duty cycle. The braking
period is 30s. According to the tables in the “Braking Resistors” section (Motor Drives Accessories – User Manual) the
applicable braking resistor is 10
Ω
– 24 kW.
The max. continuous duty for said resistor is 62s: the braking period is then compatible with that rating. Otherwise, a
higher rated resistor should be applied.
Parameter setting:
C210
=
[With resistor]
.
C211
=30s
C212
=50%
When
C210
=
[With resistor]
the deceleration ramp extension is never performed, unless the clamp transistor of the
brake resistor has been inactive for a time longer than the time set in parameters
C211
,
C212
(weak power
resistance/energy).
Factory-setting assumes that no braking resistor is provided. In this case,
C210
sets promptness, with respect to
variations of DC bus, for the deceleration ramp slowing-down, in order not to overload the bus capacitor bank.
If
C210
is set to zero in FOC control, overfluxing deceleration is performed. For the other controls with
C210
=0,
deceleration slows down when given values of the bus voltage are reached (depending on the drive voltage class).
If
C210
is > 0, DC bus voltage is controlled by considering the derivative of the bus voltage. The higher the value in
C210
, the lower the values for voltage variation affecting deceleration ramp times.
NOTE
The clamp transistor is not commanded if the drive is supplied from a Regenerative
source (see
C008
= xT Regen, where x can be 2, 4, 5, or 6).
NOTE
If the drive is powered by a Regenerative source (see parameter
C008
= xT Regen, where x
may be 2, 4, 5 or 6) the clamp transistor is not controlled and the ramp extension functionality
is disabled.