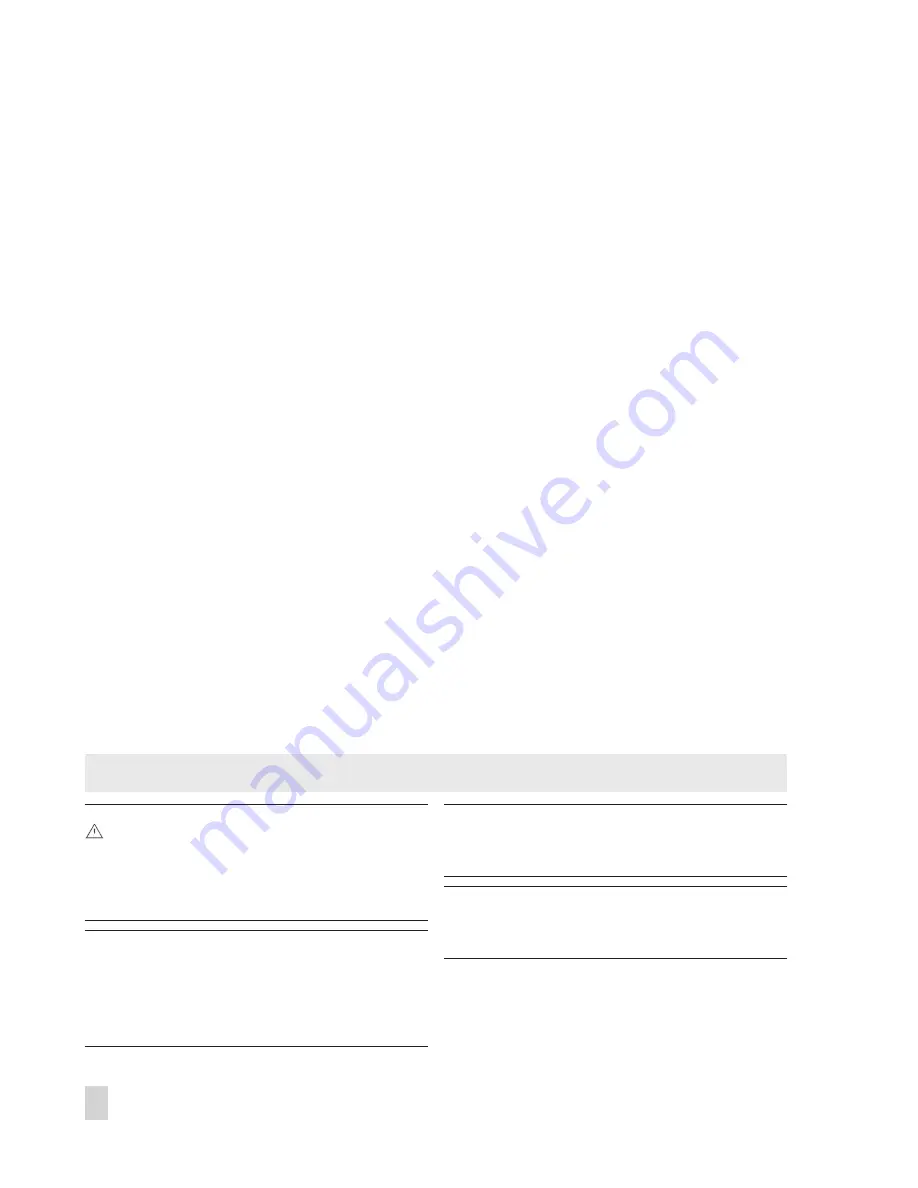
2
EB 8384-6 EN
DANGER!
indicates a hazardous situation which, if not
avoided, will result in death or serious injury.
WARNING!
indicates a hazardous situation which, if not
avoided, could result in death or serious
injury.
NOTICE
indicates a property damage message.
Note:
Supplementary explanations, informa-
tion and tips
Definitions of the signal words used in these instructions
Summary of Contents for 3730-6
Page 19: ...EB 8384 6 EN 19...
Page 51: ...EB 8384 6 EN 51...
Page 113: ...EB 8384 6 EN 113...
Page 114: ...114 EB 8384 6 EN...
Page 115: ...EB 8384 6 EN 115...
Page 116: ...116 EB 8384 6 EN...
Page 117: ...EB 8384 6 EN 117...
Page 118: ...118 EB 8384 6 EN...
Page 119: ...EB 8384 6 EN 119...
Page 120: ...120 EB 8384 6 EN...
Page 123: ...EB 8384 6 EN 123 diagnostic functions 11 Z Zero calibration 68 Index...