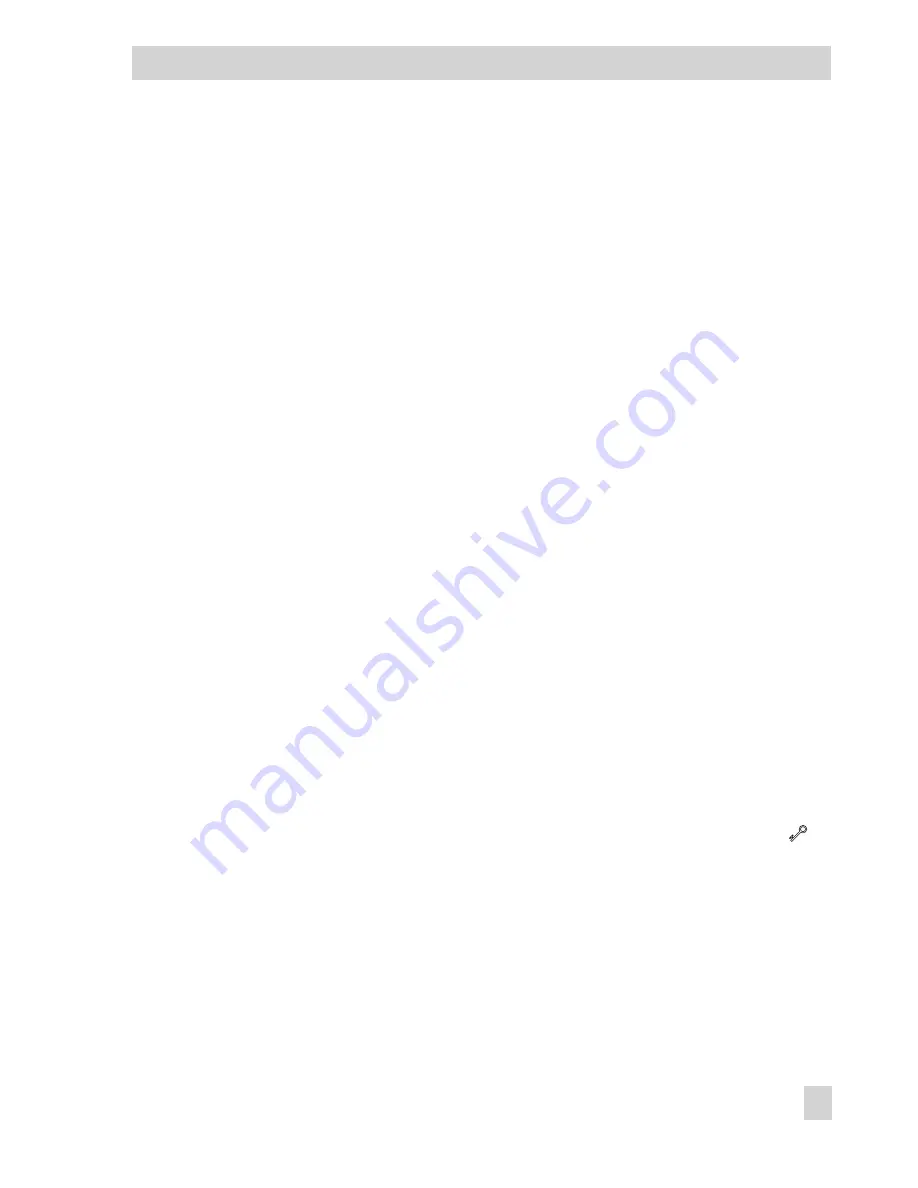
3.6
Additional equipment
Inductive limit switch
In the version with inductive limit switch, the
rotary shaft of the positioner carries an ad-
justable tag which actuates the installed
proximity switch. The optional inductive limit
switch (11) is connected to A1, while the re-
maining software limit switch is connected to
A2.
Solenoid valve
If the operating voltage for the solenoid
valve (12) falls under 12 V, the supply pres-
sure for the i/p converter (6) is vented to the
atmosphere. The positioner can no longer
operate and the control valve moves to the
fail-safe position determined by the actua-
tor, independent of the reference variable.
In manual mode, the manual set point is
reset to 0 %. A different manual set point
must entered again.
Forced venting
If the voltage signal at ter81/–82
falls below 12 V, the i/p converter (6) is
de-energized. The positioner vents the actu-
ator, causing valve to move to the fail-safe
position determined by the actuator, inde-
pendent of the reference variable.
Analog position transmitter
The position transmitter (13) is a two-wire
transmitter and issues the travel sensor sig-
nal as a 4 to 20 mA signal processed by the
microcontroller. Since this signal is issued in-
dependent of the positioner’s input signal,
the momentary travel/angle of rotation is
controlled in real-time. Additionally, the po-
sition transmitter allows positioner faults to
be indicated over a signal current of
< 2.4 mA or > 21.6 mA.
Leakage sensor
By upgrading the positioner with a leakage
sensor, it is possible to detect seat leakage
when the valve is in the closed position. For
more details, refer to the Operating Instruc-
tions EB 8389-1 EN on EXPERTplus Valve
Diagnostics.
Binary input
The optional binary input can be configured:
4
To connect a floating contact
4
To connect a non-floating contact (0 to
24 V DC)
By selecting a certain function, one of the
following actions can be activated:
4
Transmit switching state
The switching state of the binary input is
logged.
4
Activate local write protection
After the first initialization, a local write
protection can be activated. While the
binary input is active, no settings can be
changed at the positioner. The positioner
cannot be re-initialized. Configuration
enabling over
Code 3
is not active ( ).
4
Start PST
The positioner start a single partial stroke
test. The test is performed with the set-
tings in
Code 49 - d2
to
Code 49 - d9
(refer to Operating Instructions
EB 8389-1 EN on EXPERTplus Valve Di-
agnostics).
4
Move valve to safety set point
An on/off valve moves to the predeter-
EB 8384-6 EN
13
Design and principle of operation
Summary of Contents for 3730-6
Page 19: ...EB 8384 6 EN 19...
Page 51: ...EB 8384 6 EN 51...
Page 113: ...EB 8384 6 EN 113...
Page 114: ...114 EB 8384 6 EN...
Page 115: ...EB 8384 6 EN 115...
Page 116: ...116 EB 8384 6 EN...
Page 117: ...EB 8384 6 EN 117...
Page 118: ...118 EB 8384 6 EN...
Page 119: ...EB 8384 6 EN 119...
Page 120: ...120 EB 8384 6 EN...
Page 123: ...EB 8384 6 EN 123 diagnostic functions 11 Z Zero calibration 68 Index...