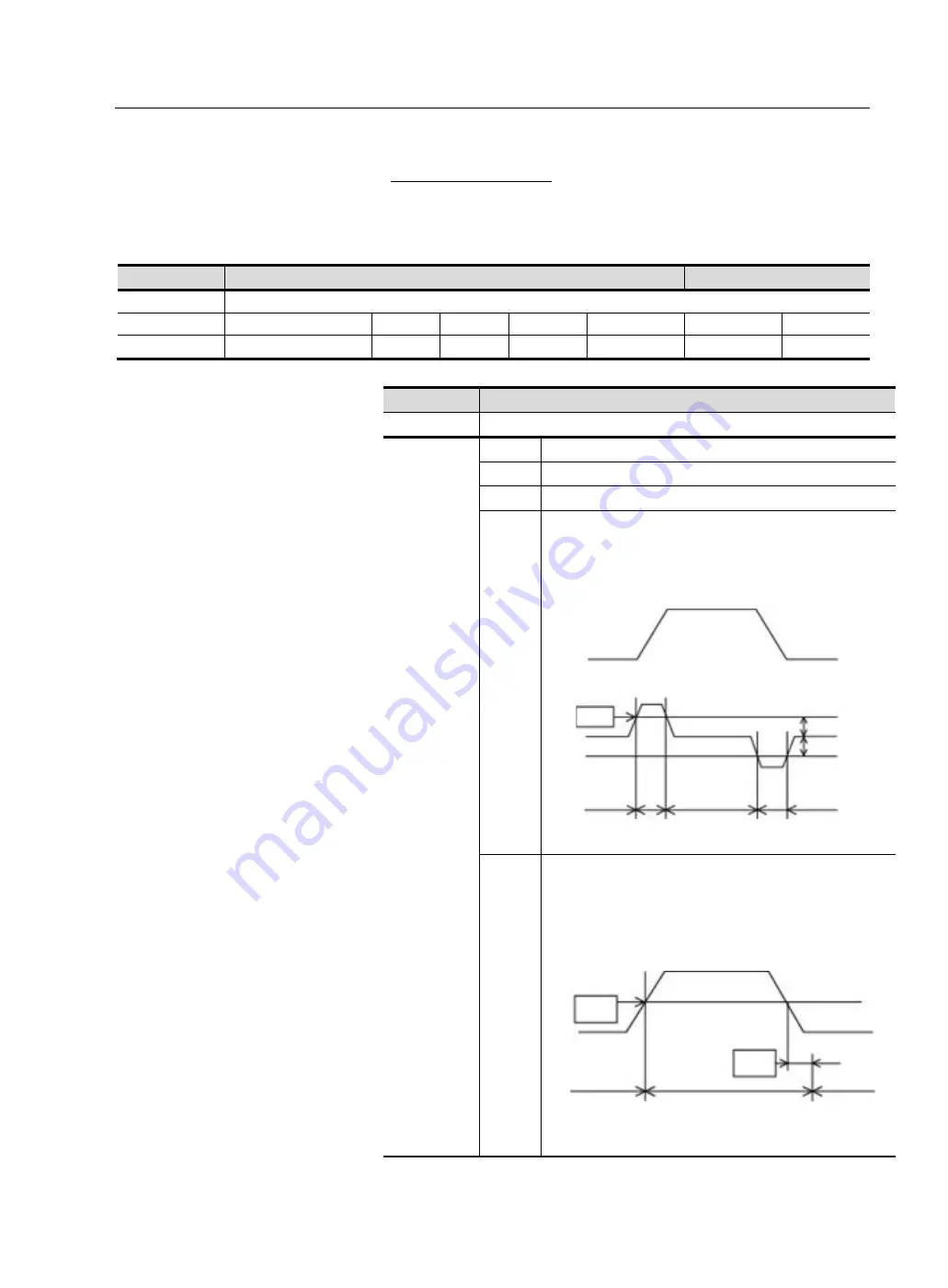
Tuning by Gain Setting
8-45
CSD7 Servo Drive (EtherCAT)
Gain Switching Mode
Gain Switching Mode can be chosen in 0x2006[03] (Ft-0.06[D2]).
0x2006
Auxiliary Function Selection 1
CSP
Sub-Index 3
Gain Switching Mode
Setting Range
Size (Data Type)
Unit
Access
PDO Map
Attribute
Init Value
Ft-no
0~9
1 byte(USINT)
-
RW
-
Always
0x0
Ft-0.06[D2]
Ft-0.06[D2]
Gain Switching Mode
Range
0~9
Description
0
The 1st gain is fixed (1, 3 group gain).
1
The 2nd gain is fixed (2, 4 group gain).
2
The 2nd gain is used when </G-SEL> signal is input.
3
When the torque command is higher than the set value, the
2nd gain is used.
4
When the velocity command is higher than the set value,
the 2nd gain is used.
Switching level
Velocity
Level
1st
1st gain
1st
Torque
Switching level
2nd
2nd
Velocity
Command
Level
Delay
1st
1st
2nd gain
Summary of Contents for OEMax CSD7
Page 1: ...CSD7 Servo Drive User Manual Catalog Number s CSD7_ BN F 1 EtherCAT Network type ...
Page 4: ......
Page 12: ...viii CSD7 Servo Drive EtherCAT SAFETY FUNCTION CONNECTOR B 6 ...
Page 23: ...Preface P 11 CSD7 Servo Drive EtherCAT ...
Page 24: ......
Page 33: ...Installation 2 5 CSD7 Servo Drive EtherCAT 100W 200W 400W 800W 1KW 1 5KW ...
Page 38: ......
Page 76: ......
Page 94: ......
Page 114: ......
Page 126: ......
Page 314: ......
Page 327: ...able and Connector Specification B 5 CSD7 Servo Drive EtherCAT ...
Page 330: ......
Page 331: ...Publication CSD7 UM001A Network EN October 2015 ...
Page 332: ...Copyright 2015 RS Automation Co Ltd All rights reserved ...