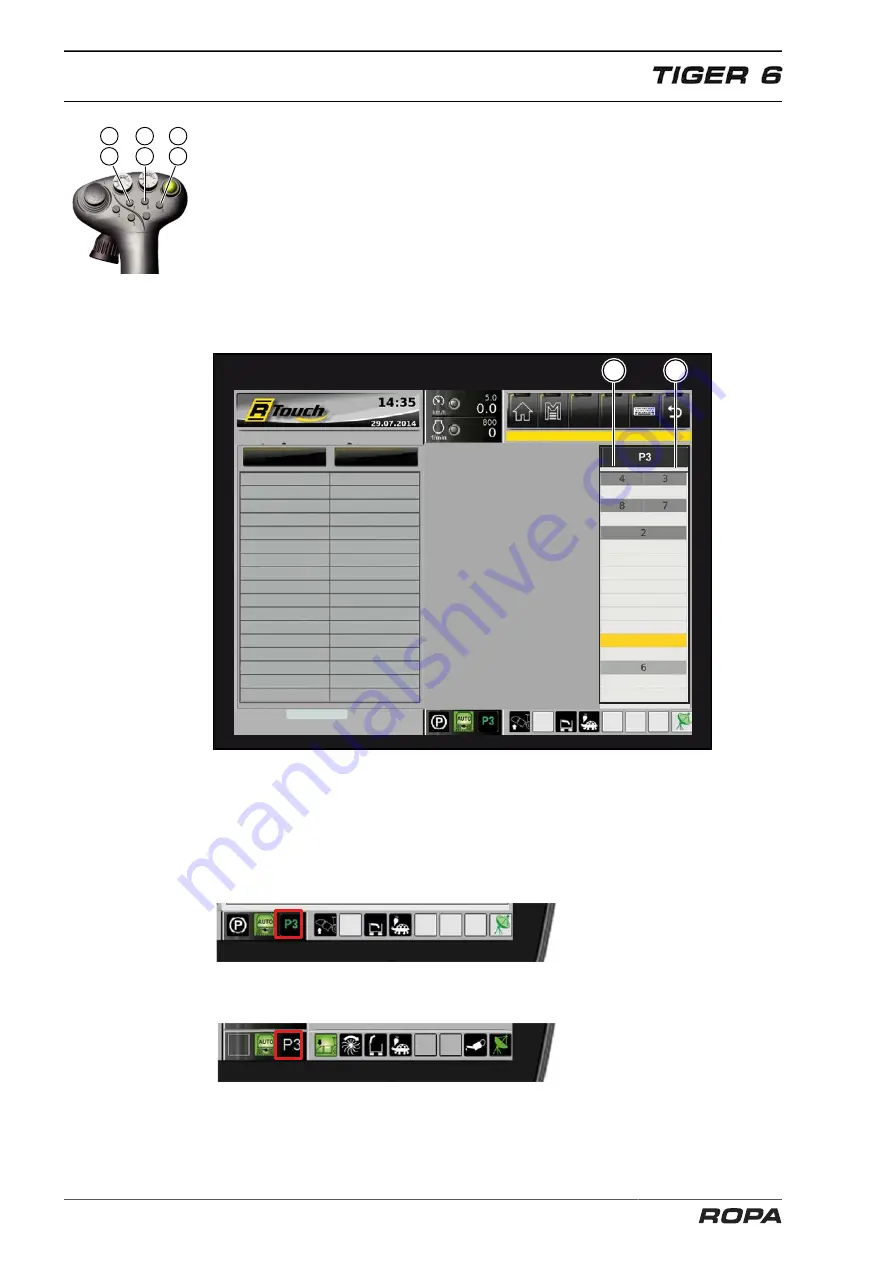
Operation
R-Concept
114 / 564
9
8
7
P1
P2
P3
Call up the saved machine settings
Pressing on one of three programmable keys P1 (
7
), P2 (
8
), P3 (
9
) you can activate
one of three different machine settings. It enables you to call up the optimum settings
for specific - recurrent - lifting conditions or ground types by pressing just one key.
After pressing one of the programmable keys P1, P2 or P3, a brief overview of the
machine settings appears on the R-Touch.
Programmable keys (P1/P2/P3)
defoliator depth
spreader speed
elevator speed
turbines stage
Infeed conveyor stage
lifting rollers stage
depth-contr. sh. stage
shaking share stage
defoliator rpm
lifting rpm
Cruise control
guide grid height
Pinch roller on/off
Share depth
Scalper
depth-contr. wh. height
defoliat. discharge act.
memory (teach)
no memory
no memory
memory (edit)
no memory
emergency operation
no memory
no memory
no memory
no memory
no memory
no memory
no memory
memory (teach)
no memory
memory (teach)
no memory
import
export
P3
2
1
(1)
Values on the left side
(2)
Values on the right side
The machine settings stored on the respective programmable key are shown in the
field with the black surround. These values are set on the machine upon pressing the
programmable key. On the R-Touch at the status indicators the icon for the program-
mable key is displayed in green.
Once you change a set with the programmable key value manually, the icon on the R-
Touch, e.g. "P3", will be highlighted grey.
Summary of Contents for Tiger 6
Page 3: ...Contents 3 564 Contents...
Page 4: ...Contents 4 564...
Page 13: ...Preface 13 564 1 Preface...
Page 14: ...Preface 14 564...
Page 22: ...Safety 22 564...
Page 23: ...Safety 23 564 2 Safety...
Page 24: ...Safety 24 564...
Page 41: ...General View and Specifications 41 564 3 General View and Specifications...
Page 42: ...General View and Specifications 42 564...
Page 53: ...General Description 53 564 4 General Description...
Page 54: ...General Description 54 564...
Page 57: ...Operating Components 57 564 5 Operating Components...
Page 58: ...Operating Components 58 564...
Page 98: ...Operation 98 564...
Page 99: ...Operation 99 564 6 Operation...
Page 100: ...Operation 100 564...
Page 226: ...Operation Defoliator 226 564 RIS defoliator RES defoliator...
Page 291: ...Operation Infeed conveyor 291 564 2 1 1 Infeed conveyor control block...
Page 299: ...Operation Strainer wheels turbines 299 564 4 Rpm strainer wheels...
Page 325: ...Operation Bunker unloading 325 564 6 19 Bunker unloading...
Page 361: ...Maintenance and Service 361 564 7 Maintenance and Service...
Page 362: ...Maintenance and Service 362 564...
Page 418: ...Maintenance and Service Defoliator 418 564 Defoliator in the maintenance position...
Page 475: ...Malfunction and Remedies 475 564 8 Malfunction and Remedies...
Page 476: ...Malfunction and Remedies 476 564...
Page 528: ...Lists Tables Plans Diagrams Maintenance Verification 528 564...
Page 558: ...558 564...
Page 559: ...Index 559 564 10 Index...
Page 560: ...Index 560 564...