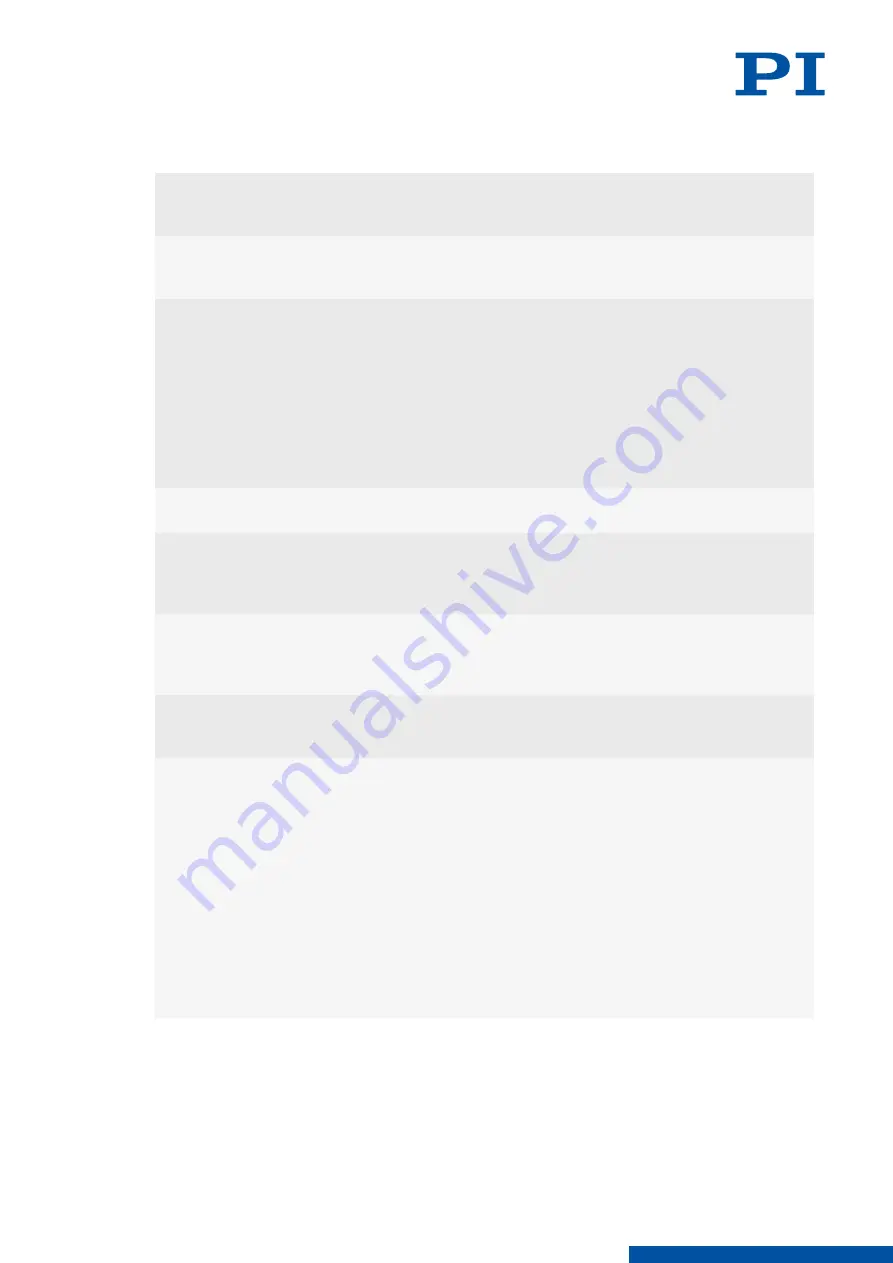
10
Parameter Reference
Proportional constant of the PID servo algorithm.
Is used for fast correction of the position error.
0 to 32767
Integration constant of the PID servo algorithm.
Used for reducing static position error.
0 to 32767
Differential constant of the PID servo algorithm.
Used for damping rapid control oscillation.
The D term can be calculated as a floating
average over several servo cycles. The
parameter 0x71 (D-Term Delay) specifies how
many values (i.e., servo cycles) are to be used
for calculating the average.
0 to 32767
The preset value of this parameter should not be
changed.
Limit of the integration constant.
0 to 32767
Feed-forward control of the commanded
velocity.
Used for minimizing positioning error.
0 to 32767
Maximum Position
Error (Phys. Unit)
Maximum position error.
Used by controllers that support a dynamic
profile (parameter 0x1B < > 5) for detecting
motion error.
Maximum control value for driving an axis
respectively a channel.
See the response to HPA? for possible values
Numerator Of The
Counts-Per-Physical-
Unit Factor
Numerator of the factor for converting impulses
to physical units.
The factor for the counts per physical unit of
length specifies the unit of length for position
queries and motion commands in closed-loop
operation. The values of every parameter, whose
unit is either the physical unit of length itself or a
unit of measurement based on it, are
automatically adapted to the set factor. The
factor for the counts per physical unit of length
has no impact on the stability of the servo loop
but is used for the input and output scaling of
position values.
Decimal number
10 PARAMETER REFERENCE
PZ285EN
‒
1/30/2019
169
M O T I O N | P O S I T I O N I N G