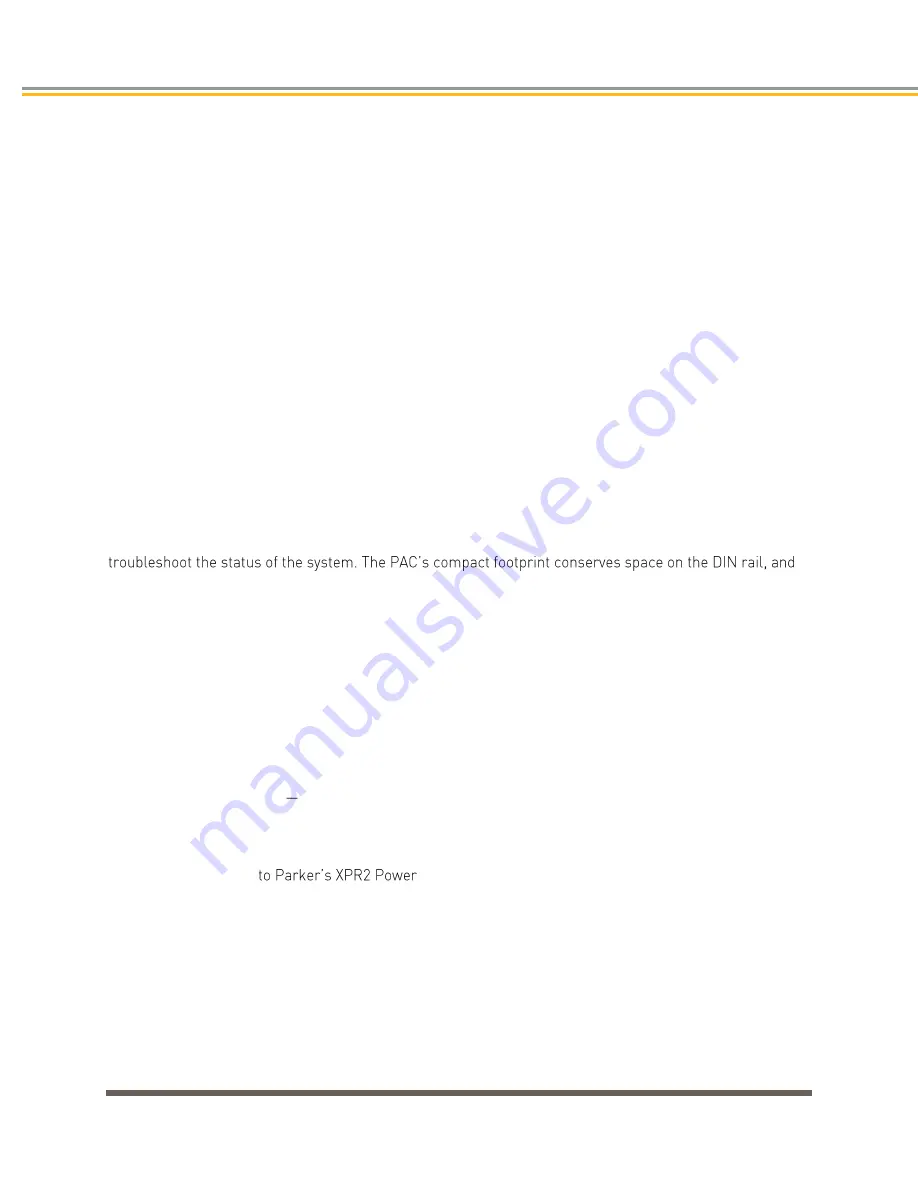
PRODUCT OVERVIEW
12
Parker Automation Controller Installation Guide
Product Description
The Parker Automation Controller (PAC) is a specialized control device with programmable software
designed to automate high-speed, electromechanical processes such as those involved in operating
assembly line equipment. The PAC is engineered to offer a wide variety of input/output arrangements for
fast-motion control, while withstanding the temperature ranges, vibrations, and electrical noise of
industrial environments.
The PAC features a modular design that makes it a highly flexible solution. The PAC connects to a series
of PACIO Modules, which you choose based on the requirements of your specific application. The selection
of PACIO Modules includes a bus coupler, a variety of digital or analog input/output modules, a counter,
temperature modules, and interface modules.
The PAC also accommodates connections to remote I/O Modules, industrial control networks, terminals,
factory displays, and Internet-connected devices such as PCs, notebooks, and even smart phones.
The PAC includes ports for Ethernet and EtherCAT communications. For applications requiring additional
communication capabilities, customers can order the PAC with an optional communication protocol, such
as PROFINET or Ethernet/IP.
The PAC operating system and runtime software reside on a standard Secure Digital (SD) memory card
inserted into a slot at the top of the PAC. LED indicators on the PAC front panel help you to monitor and
its installation requires only a small screwdriver.
Product training videos are available on our website. These include videos on: Quick Start, Software
Introduction and Configuration, as well as other topics.
Discrete Logic Capabilities: The PAC incorporates an internal, high-speed EtherCAT bus (E-Bus) that can
communicate to locally attached I/O Modules for discrete control and sensing. In addition, the PAC
incorporates an external EtherCAT RJ45 connector for connection of EtherCAT motor drives, remote
discrete I/O (via EtherCAT Bus Couplers) racks or other miscellaneous EtherCAT sensors, and devices.
Motion and 3D Coordinated Motion: The PAC offers two levels of motion control software utilizing
IEE1388 distributed clocks one for simple motion and another for advanced CNC. An external EtherCAT
connector provides communications to up to 32 axes of EtherCAT motor drives.
Visualization: The PAC offers two options for visualization. For complete HMI capabilities, the PAC
connects via MODBUS
Stations with the award winning Interact Xpress software.
The MODBUS communication driver comes standard with each PAC system. The PAC also offers a Web
visualization option that allows users to visualize project screens in a web browser.
Communication Interface Protocols: The PAC offers several options for communications to external
devices. The PAC comes standard with MODBUS TCP Master and Slave capabilities. The PAC has an
optional Ethernet/IP option to produce tags to and Allen Bradley PLC. The PAC also offers a PROFINET
Slave option via a communication module.
Summary of Contents for PAC
Page 11: ...CHAPTER 1 Product Overview...
Page 18: ......
Page 19: ...CHAPTER 2 Installation...
Page 33: ...CHAPTER 3 System Start up and Configuration...
Page 69: ...CHAPTER 4 PACIO Modules...
Page 143: ...2 After adding the device and code to the project you will configure the IO map as displayed...
Page 155: ...PAC with 400XR series...
Page 156: ...PACIO MODULES 156 Parker Automation Controller Installation Guide...
Page 157: ...PAC with 400LXR...
Page 158: ...PACIO MODULES 158 Parker Automation Controller Installation Guide PAC with SMH sensors...
Page 159: ...CHAPTER 5 Communication Interfaces Optional...
Page 176: ......
Page 177: ...CHAPTER 6 Troubleshooting...
Page 188: ...TROUBLESHOOTING 188 Parker Automation Controller Installation Guide...
Page 189: ...APPENDIX A PAC System Specifications...
Page 195: ...APPENDIX B Additional Information...