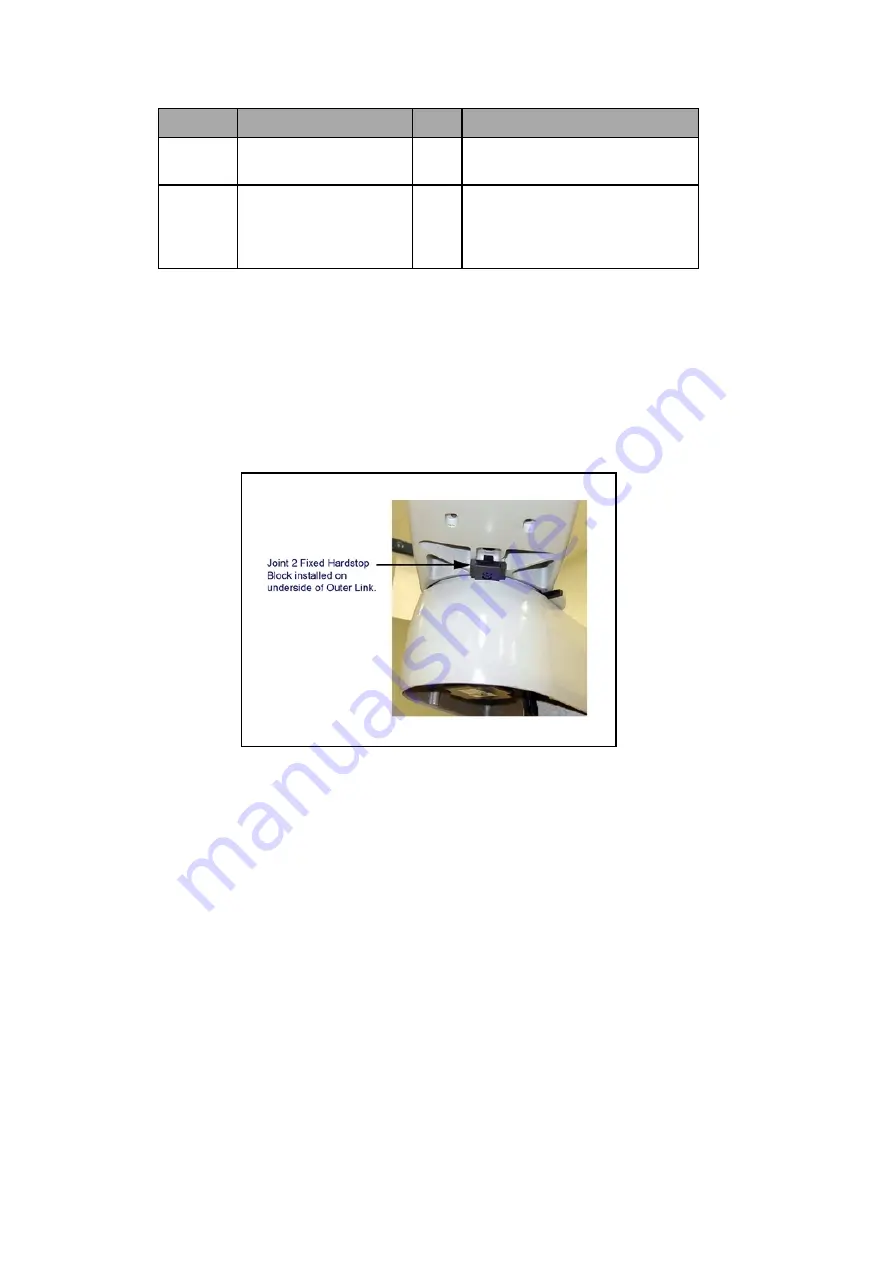
98
eCobra 600 and 800 Robots with EtherCAT
24402-000 Rev B
Item
Meaning
Item
Meaning
Plate installed in -81°
position
C
12 thru holes for M5 x
10 screws to install
Joint 2 hardstops, loc-
ated 30° apart
F
Joint 2 Fixed Hardstop device
2. Use a 4 mm hex wrench to install three supplied M5 x 10 screws to secure the plate.
Tighten the screws to 4.5 N·m. Repeat the process for the second plate. The plates can be
installed in a number of different positions, depending on how much you need to limit
the range of Joint 2.
NOTE:
The two hardstop sides do not have to be in the same position, so the
workspace does not have to be symmetrical.
3. Slide the fixed hardstop device into the slot on the underside of the outer link. See Fig-
Figure 5-17. Fixed Hardstop Block for Joint 2 installed on underside of Outer Link
4. Use a 3 mm hex wrench to install two supplied M4 x 10 screws to secure the hardstop
device. Tighten the screws to a torque of 2.5 N·m.
IMPORTANT:
After installing any adjustable hardstops, modify the robot joint
motion limit(s). Refer to the
Sysmac Studio Version 1 Operation Manual (Cat. No.
W504)
for more information. Refer to Adjustable Hardstops on page 32 for
information about robot joint range limitations.