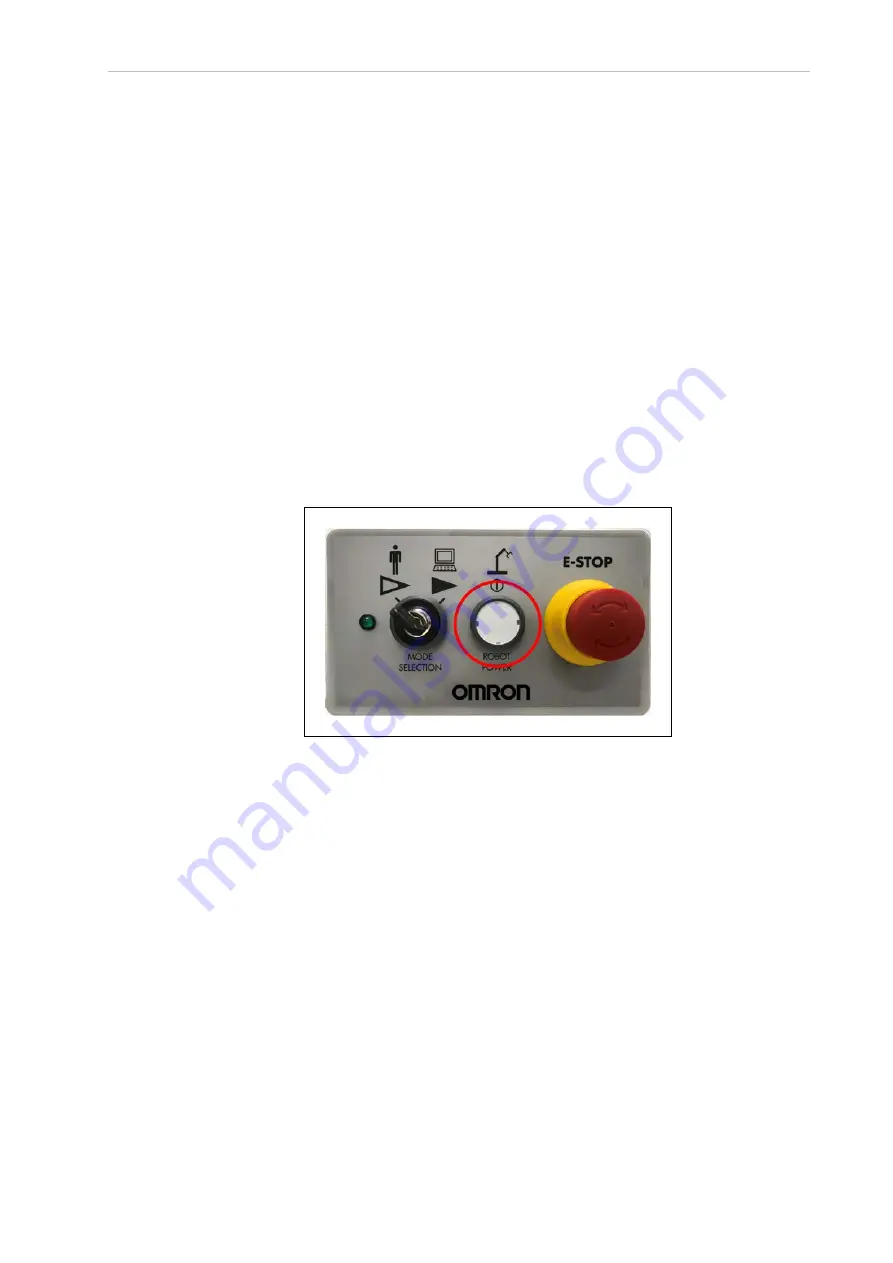
Chapter 6: System Operation
High Power and Faults
The AUTO.POWER.OFF system switch controls if the robot prevents or disables high power for
the following errors. Refer to the
eV+3 User's Manual (Cat. No. I651)
for more information.
l
(-624) Force protect limit exceeded
l
(-1003) Time-out nulling errors Mtr
l
(-1006) Soft envelope error Mtr
High Power Request Methods
There are several methods to request robot high power as described below.
Request High Power with the Front Panel
When a Front Panel is present in the system, the high power button can be used to request
high power to the robot.
Additional Information
: Refer to Front Panel Schematic on page 48 for more
information about connecting external devices to the high power enable signal
on the XFP connector.
Figure 6-6. High Power Button on Front Panel
Request High Power with a Connected PC
High power can be requested with Sysmac Studio software. Refer to the software user doc-
umentation for more information.
Request High Power with a User Program
High power can be requested with a user program through the use of the POWER system
switch or an NJ function block. Refer to the
eV+3 User's Manual (Cat. No. I651)
or the
Sysmac Stu-
dio Version 1 Operation Manual (Cat. No. W504)
for more information.
Request High Power with the Pendant
The handheld pendant can be used to request high power to the robot. Refer to the
T20 Pendant
User's Manual (Cat. No. I601)
for more information.
24402-000 Rev B
eCobra 600 and 800 Robots with EtherCAT
107