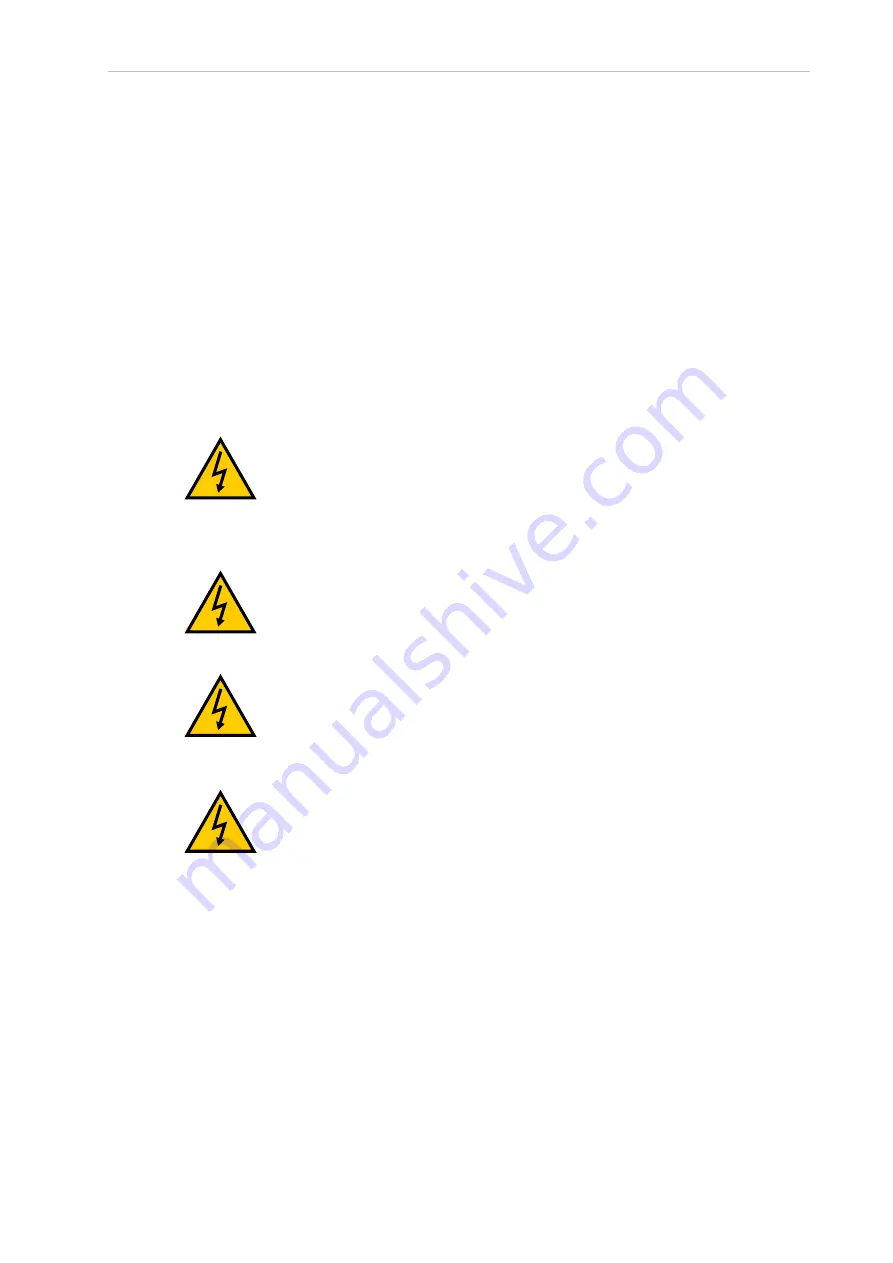
Chapter 4: System Cable Installation
2. Connect the cable shield (D) to frame ground on the power supply (C).
3. Plug the mating connector end of the 24 VDC cable (F) into the 24 VDC connector on
the robot interface panel(A).
4. Connect the cable shield (G) to the ground point on the robot interface panel (A).
4.4 Connecting 200-240 VAC Power Cable
Use the following procedure to connect the 200-240 VAC cable from the power supply to the
robot interface panel.
Additional Information
: Refer to External Connection Specifications on page 145
for more information.
IMPORTANT:
Do not apply AC power until all installation steps are complete
and verified and all safety measures are in place.
WARNING: ELECTROCUTION RISK
National Electrical Code (and/or local codes) require that you provide an appro-
priately sized branch circuit protection and lockout/tagout capability. Ensure
you comply with all local and national safety and electrical codes for the
installation and operation of the robot system.
DANGER: ELECTROCUTION RISK
ISO 10218-1, Clause 5.2.4 mandates that, during installation, you must provide
a fail-safe lockout to prevent unauthorized third parties from turning on power.
WARNING: ELECTROCUTION RISK
eCobra robot systems require an isolating transformer for connection to asym-
metrical mains systems or those using an isolated (impedant) neutral. Many
parts of Europe use an impedant neutral.
DANGER: ELECTROCUTION RISK
Only a skilled and instructed person must install AC power. Clause 5.2.4 of the
ISO 10218-1 requires that the person installing the system must use fail-safe
lockout measures to prevent unauthorized third parties from turning on power.
Refer to the
Robot Safety Guide (Cat. No. I590)
for more information.
NOTE:
Install the robot system as a piece of equipment in a permanently-
installed system.
AC Power Diagrams
If using a three-phase power source, it must be symmetrically-earthed (with grounded neutral).
Connections called out as single-phase can be wired Line-to-Neutral or Line-to-Line.
24402-000 Rev B
eCobra 600 and 800 Robots with EtherCAT
81