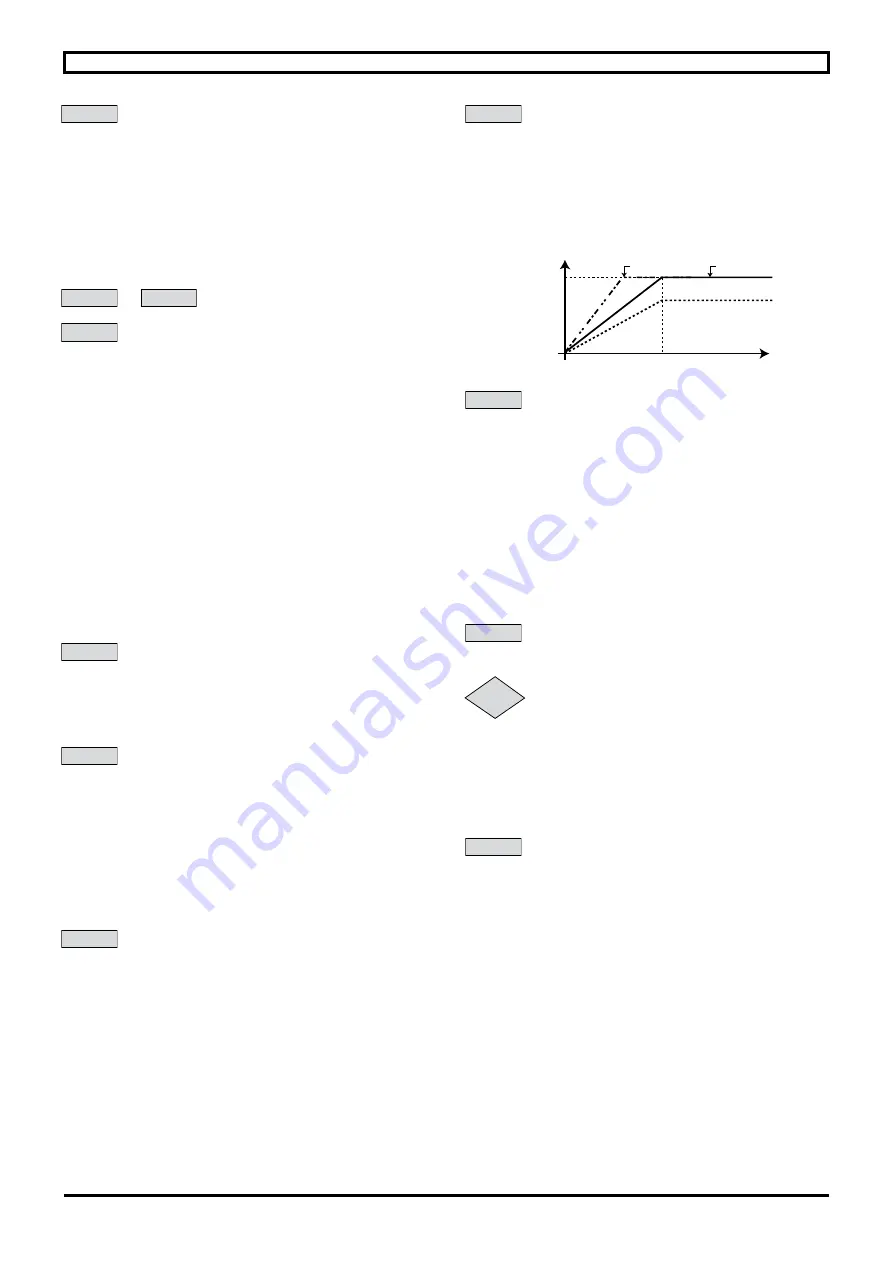
75
ADVANCED PARAMETER-SETTING MODE
Commissioning manual Powerdrive MD2/FX
4617 en - 2017.09 / e
05.37 : Variable inductance parameter set
Adjustment range: Yes (1)/No (0)
Factory setting: No (0)
Format: 8 bits
Yes
(1): Reserved for machines with a cogging rate (Lq/Ld
ratio at the nominal point) is higher than 25%. See parameters
05.72
to
05.88
.
No
(0): Only the Ld and Lq values entered in
05.24
and
05.51
are taken into account by the motor control. Reserved for
machines with a cogging rate lower than 25%.
05.38 to 05.49 : Not used
05.50
: Motor ventilation
Adjustment range: Not cooled (0), Self cooled (1)
Forced cooling (2)
Factory setting : Self cooled (1)
Format: 8 bits
Not cooled (0):
The motor has neither an internal fan nor a forced ventilation
unit.
Self cooled (1):
The motor has a fan on the shaft.
Forced cooling (2):
The motor has a forced ventilation unit.
The value of parameter
05.50
combined with the values of
parameters
04.15
(Motor thermal time constant),
05.07
(Motor rated current),
05.08
(Motor rated speed ) and
11.31
(User drive mode) is used to estimate the machine thermal use
percentage indicated in
04.19
(%).
05.51
: Q axis inductance (synchronous motor)
Adjustment range : 40 to 999% of
05.24
Factory setting : 100%
Format: 16 bits
Used to set an inductance value in quadrature with the pole
axis for synchronous motors with projecting poles.
05.52
: Starting current (synchronous motor)
Adjustment range : ± 300% of
05.07
Factory setting : 20%
Format: 16 bits
With a synchronous motor (
11.31
= Servo (3)), this parameter is
used to improve starting for permanent magnet motors controlled
without a position sensor.
With an asynchronous motor (
11.31
= Closed Loop vector),
this parameter is used to boost the magnetising current on
machine starting for quicker flux installation.
05.53
: Flux establishment time
Adjustment range : 0.00 to 320.00 s
Factory setting : 0.25 s
Format: 16 bits
With a synchronous motor (
11.31
= Servo (3)) without a sensor,
this parameter defines the «parking» time before motor rotation.
With an asynchronous motor, after a run command, the flux is
deemed to have been installed if
05.53
has elapsed or if 7/8 of
the machine flux is obtained.
05.54
: Base Freq./nominal Freq. ratio
Adjustment range : 75 to 150%
Factory setting : 100%
Format: 16 bits
This parameter is used to adjust the level of flux in the induction
motor.
The diagram below shows the influence of
05.54
on the
change in the motor no-load voltage characteristic as a function
of the speed of rotation.
05.55
: Motor overcurrent threshold
Adjustment range : 0 to 999%
Factory setting : 160%
Format: 16 bits
Synchronous motors:
This threshold (% of
05.07
) defines the detection level for the
«Motor overcurrent» trip. If this threshold expressed in A is
higher than 1.6 x
11.32
, the «Overcurrent at drive output» trip
will then override the «Motor overcurrent» trip.
Asynchronous motors: No effect.
05.56
: Not used
05.57
: Actual switching frequency
Adjustment range : 2 kHz to 18 kHz
Format: 8 bits
Displays the switching frequency actually used. Related
parameters:
05.18
,
05.60
and
18.27
.
05.58
: Two PWM update per period
Adjustment range : No (0) or Yes (1)
Factory setting : Yes (1)
Format: 8 bits
No (0):
The frequency for calculating the motor control is the same as
that displayed by
05.57
.
Yes (1):
The frequency for calculating the motor control is double that
displayed by
05.57
. This option allows more precise motor
control. It is not available when the user has chosen a switching
frequency
05.18
higher than 8 kHz
.
05.09
05.54
> 100%
05.54
05.06
= 100%
05.54
< 100%
Motor voltage
Motor
speed
Summary of Contents for LEROY-SOMER Powerdrive FX
Page 1: ...4647 en 2017 09 e Powerdrive MD2 FX Commissioning manual R f rence...
Page 41: ...41 QUICK SETUP MODE Commissioning manual Powerdrive MD2 FX 4617 en 2017 09 e Notes...
Page 174: ...174 MAINTENANCE Commissioning manual Powerdrive MD2 FX 4617 en 2017 09 e Notes...
Page 175: ...175 MAINTENANCE Commissioning manual Powerdrive MD2 FX 4617 en 2017 09 e Notes...