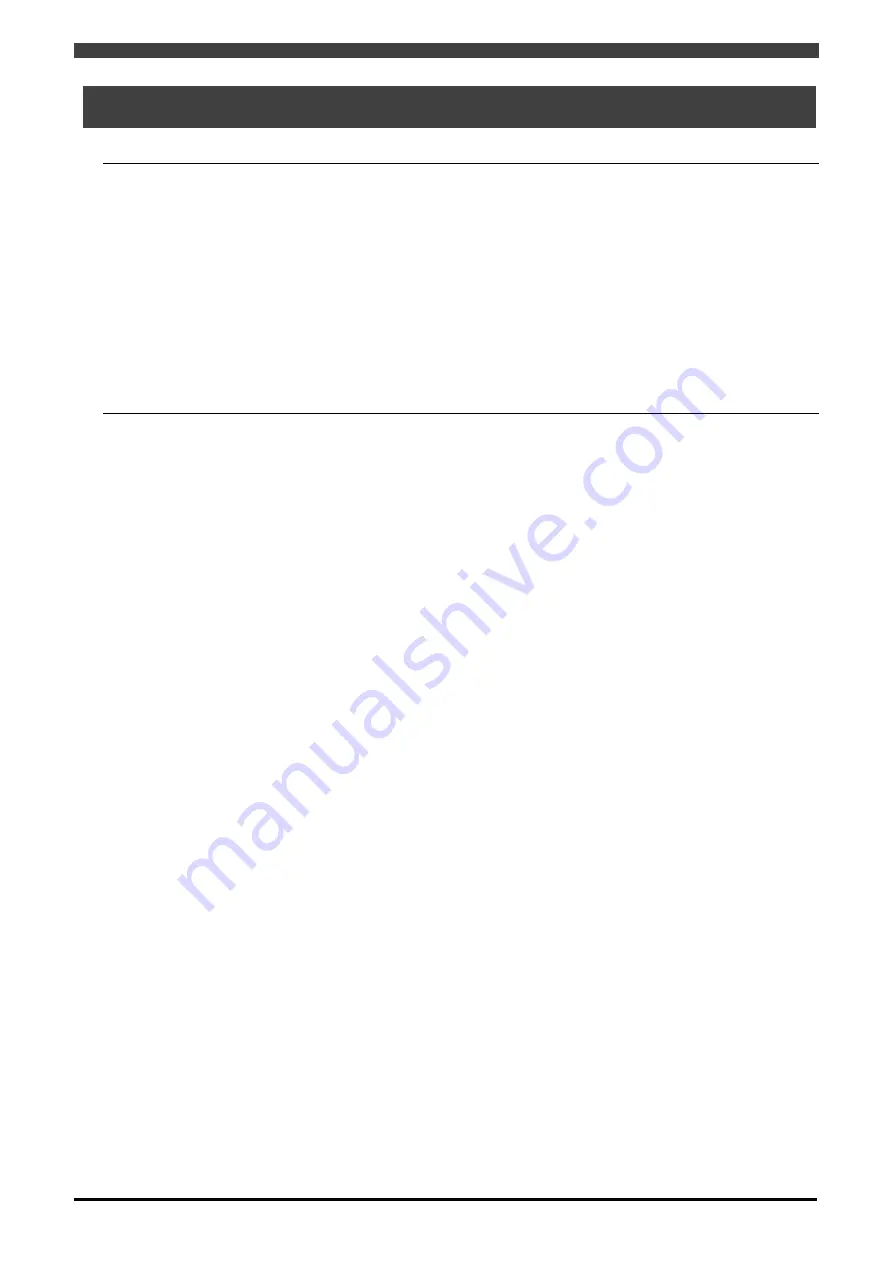
1.1 Outline
1-1
1.1 Outline
1.1.1 Features of robot monitoring unit
The robot monitoring unit (RMU20) is a Category 4 and PLe compliant system which monitors the robot
position and speed so as to shut off the power to the robot when its position or speed are deemed to be irregular.
The robot position monitoring system consists of safety circuits using microcomputers and semiconductors,
and input/output signals, redundant safety signals and other signals from the process control panel are
connected as the input/output signals from outside the robot controller.
Control signals of emergency stop button, operation switches, and magnetic switch of the robot controller are
connected as the internal input/output signals, and the unit has functions for monitoring the sequence and
status.
The robot monitoring unit is connected by a cable to the position encoder of the drive motor so that the unit
can monitor the robot operations, and the system ensures that the robot will stop safely when the robot has
operated irregularly.
1.1.2 Functions of robot monitoring unit
The robot monitoring unit is equipped with the following safety functions.
Operating range monitoring function
This function shuts off the safety outputs and stops the robot safely when the robot wrist, tool, work or robot
arm is about to move outside any of the operating ranges which have been set.
Angle monitoring function
This function monitors the operating ranges of the robot axes, and it shuts off the safety outputs and stops the
robot safely when movement along any one of the axes is about to exceed an operating range which has been
set.
Speed monitoring function
This function shuts off the safety outputs and stops the robot safely when the TCP speed exceeds 250
mm/sec. in TEACH mode.
Also this function shuts off the safety outputs and stops the robot safely when the TCP speed or each joint
speed has exceeded the pre-determined level in AUTO and MANUAL mode.
Stop monitoring function
When the "
Stop watch signal
" (stop monitoring input signal) has been cut off, this function monitors
whether the TCP and each joint angle are operating or not. This function shuts off the safety outputs and stops
the robot safely when they have exceeded the pre-determined level.
Robot controller communication
This function enables the parameters required for monitoring to be set from the robot controller.
Encoder and motor I/F
This function is for reading out the position information required for monitoring the robot position and speed
from the encoder and motor power lines.
Input/output signal, Motor power control sequence
This function always monitors statuses of redundant emergency stop and enable switch, and it executes the
servo power on/off sequences. It uses the B (normally closed) contact of the magnet switch that turns the drive
power of the motor on and off as a start condition of the robot, and enables the melting of the magnet switch to
be back-checked.
Summary of Contents for RMU20-20
Page 2: ......
Page 6: ...Contents 4 ...
Page 8: ......
Page 26: ...1 4 EC DECLARATION OF CONFORMITY FOR MACHINERY 1 18 NOTE ...
Page 68: ...2 9 Enabling RMU 2 40 NOTE ...
Page 70: ......
Page 100: ...3 4 Setting when a slider unit is used 3 30 NOTE ...
Page 102: ......
Page 138: ...4 4Approval 4 36 8 Approval is completed The following screen will be displayed ...
Page 144: ......
Page 154: ...5 4Trouble shooting 5 10 NOTE ...
Page 156: ......
Page 166: ...6 4Trouble shooting 6 10 NOTE ...
Page 168: ......
Page 189: ......