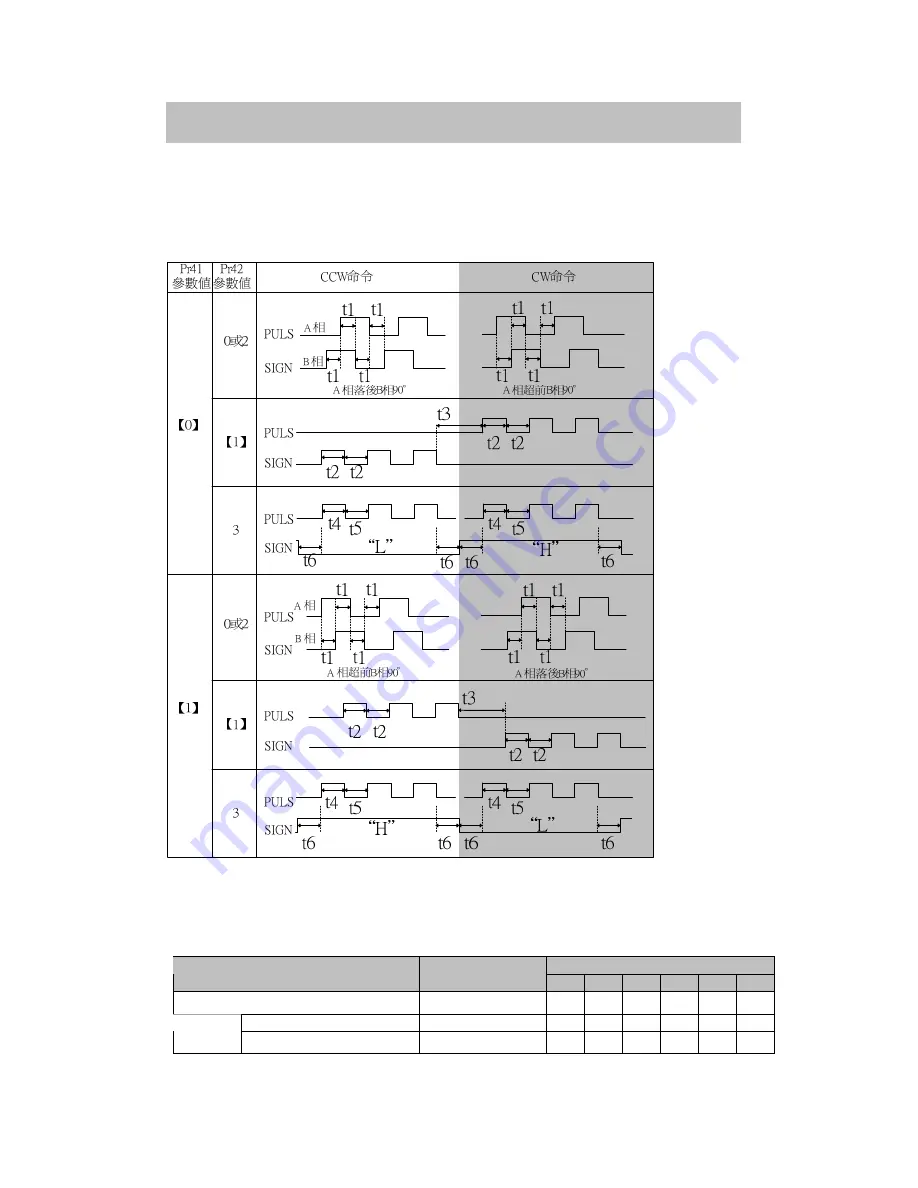
Kingservo
68
Pr
Pr
Pr
Pr41 |
41 |
41 |
41 |
Control Pulse Reversion
★
A
AA
A
Initial Value
:
:
:
:
【
0
】
Setting Range
:
:
:
:
0~1
Unit
:
:
:
:–
–
–
–
Function
:
:
:
:
Set rotary direction and form of command pulse for command pulse input.
Pr41=0,
Pr42=0 or 2 Command pulse form is 9
0°
phase differnce of 2 phase pulse(A phase+B phase)
Pr42=1 Command pulse form is CW pulse wave line and CCW pulse wave line.
Pr42=3 Command pulse form is pulse wave line+sign
•Allowable maximum frequency and minimum time range of command pulse input sign.
Minimum required time width
PULS/SIGN Input Interface
Allowable Input
Maximum Frequency
t1
t2
t3
t4
t5
t6
Line drive executive pusle line interface
2Mpps
500ns 250ns 250ns 250ns 250ns 250ns
Lind drive interface
500kpps
2µs
1µs
1µs
1µs
1µs
1µs
Pulse line
interface Interface of open zone polarity
200kpps
5µs 2.5µs 2.5µs 2.5µs 2.5µs 2.5µs
Rising/decending time of comman pulse input signa shall be kept lower than 0.1µs.
Summary of Contents for KSDG Series
Page 4: ...KingServo 4...
Page 5: ...KingServo 5 Chapter One Identificaiotns of Products 1 1Safety Sign Warning Sign...
Page 10: ...KingServo 10 1 5 2 Motor KSMA 400W 750W 4...
Page 14: ...KingServo 14 RS 232 DC24V...
Page 24: ...KingServo 24 Speed Mode Speed Mode Speed Mode Speed Mode...
Page 26: ...KingServo 26 72 0 67 0 5 0 132 0 Kingservo L1 L2 L3 r t P B1 B2 U V W I F SIG MODE SET RS 232...
Page 88: ...Kingservo 88...
Page 104: ...KingServo 104...
Page 106: ...KingServo 106 Motor KSMA 400W 50h7 44 0 5 0 11 0...