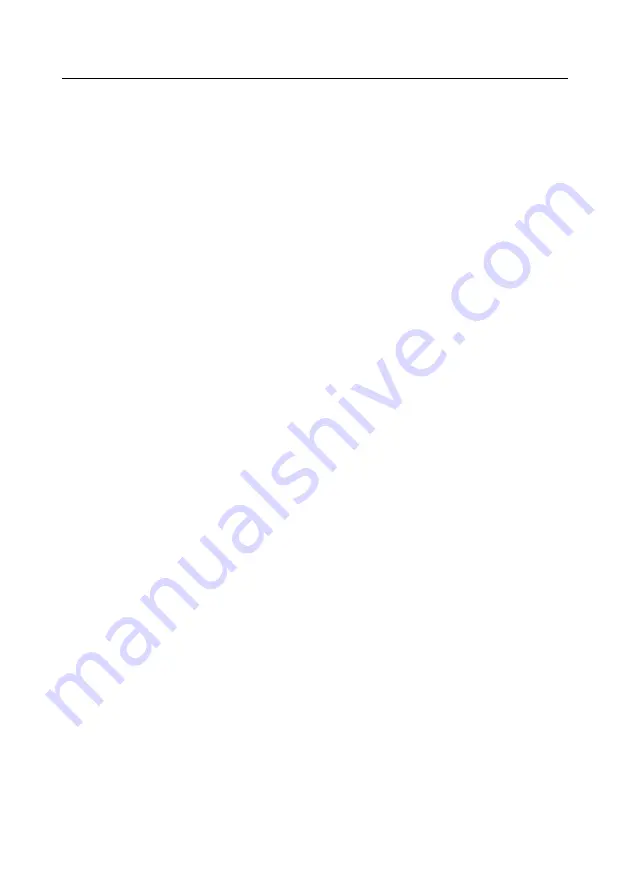
Goodrive350-19 series VFD for crane
Commissioning guidelines
-76-
5.11.2 Brake function in open/closed-loop vector control
1. Set P90.04 to 1 to enable the brake function.
2. Set relay brake output. If RO1 is connected to the braking contactor, set P06.03 to 49.
3. If the brake contactor has the feedback function, connect the brake feedback wire to an input
terminal, for example, S6. Then set P25.02 to 75 indicating brake feedback signal. Set P90.31 to
1 to enable brake feedback detection. In closed-loop mode, the brake current monitoring function
is enabled automatically. If a brake exception occurs, a protection method is applied depending
on the present current and the value of P90.34. Skip this step if the braking contactor has no
feedback function.
4. Set P90.14 (Forward brake release torque) and P90.13 (Reverse brake release torque) to
ensure there is enough torque before the brake is opened. You do not need to set P90.12 and
P90.13. In closed-loop mode, you can set P93.00 (Brake slip speed threshold) to check whether
the braking torque is enough.
5. Set the brake timing, including the forward/reverse brake release frequency, forward/reverse
brake closing frequency, delay before forward brake release (T1), delay before reverse brake
release (T5), delay after forward brake release (T2), delay after reverse brake release (T6), delay
before forward brake closing (T3), delay before reverse brake closing (T7), delay after forward
brake closing (T4), and delay after reverse brake closing (T8).
6. In closed-loop mode, you can decrease the brake release frequency and brake closing frequency
and adjust the T1
–T8 delay parameters in the timing sequence.
7. Perform trial run and check whether the brake timing is correct.