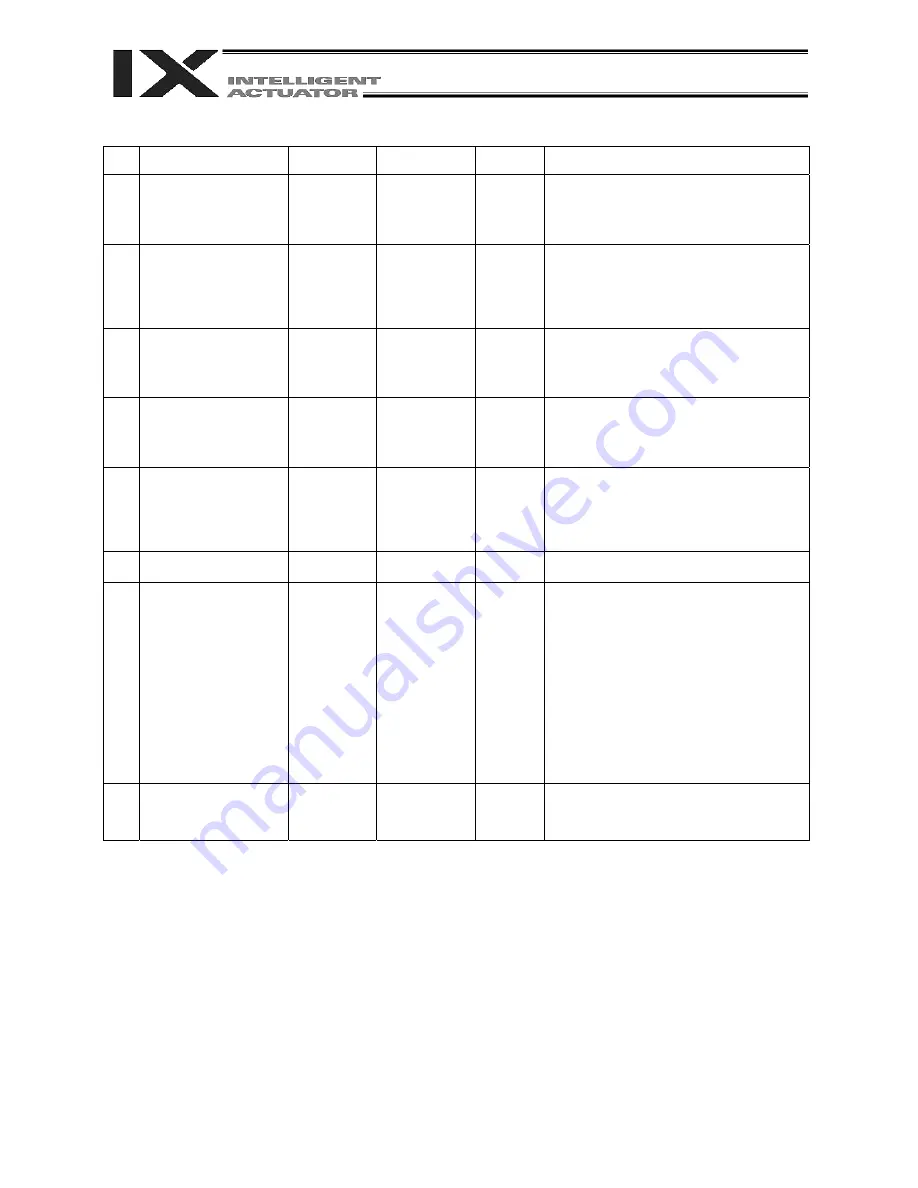
455
Appendix
Axis-Specific Parameters
No.
Parameter name
Default value
(Reference)
s
k
r
a
m
e
R
ti
n
U
e
g
n
a
r
t
u
p
n
I
93 Zone 3 MIN of linear
movement axis
0
-99999999 ~
99999999
Reference only
for SCARA axes
(axes 1 to 4)
0.001 mm Valid only when MAX > MIN. * Must be inside
the range for at least 3 msec.
* Valid for linear movement axes (axes 5 and 6
(6-axis type)) only.
(Main application version 0.15 or later)
94 Zone 3 output number for
linear movement axis
0
0 ~ 899
Reference only
for SCARA axes
(axes 1 to 4)
Physical output port or global flag (Output is
invalid if “0” is input; multiple specification is
invalid)
* Valid for linear movement axes (axes 5 and 6
(6-axis type)) only.
(Main application version 0.15 or later)
95 Zone 4 MAX of linear
movement axis
0
-99999999 ~
99999999
Reference only
for SCARA axes
(axes 1 to 4)
0.001 mm Valid only when MAX > MIN. * Must be inside
the range for at least 3 msec.
* Valid for linear movement axes (axes 5 and 6
(6-axis type)) only.
(Main application version 0.15 or later)
96 Zone 4 MIN of linear
movement axis
0
-99999999 ~
99999999
Reference only
for SCARA axes
(axes 1 to 4)
0.001 mm Valid only when MAX > MIN. * Must be inside
the range for at least 3 msec.
* Valid for linear movement axes (axes 5 and 6
(6-axis type)) only.
(Main application version 0.15 or later)
97 Zone 4 output number for
linear movement axis
0
0 ~ 899
Reference only
for SCARA axes
(axes 1 to 4)
Physical output port or global flag (Output is
invalid if “0” is input; multiple specification is
invalid)
* Valid for linear movement axes (axes 5 and 6
(6-axis type)) only.
(Main application version 0.15 or later)
98~
113
112
(For extension)
0
~
OLWL
Driver overload warning
load level ratio
100
50 ~ 100
Set the estimated motor temperature rise that
generates the overload alarm as 100%, output is
made as the overload warning to the port set in
Each Parameter No. 114 when the motor
temperature exceeded the ratio set in this parameter.
(Main application version 1.51 or later)
* To prevent motor burnout, the startup initial
temperature is assumed high considering the hot
start for the controller load ratio calculation
(Safety side). Therefore, the specification is
established not to detect the driver overload
warning till the first servo-on after specific period
of time after the controller startup in order of wrong
identification prevention when using the driver
overload warning output in purpose of malfunction
foresight monitoring.
%
Physical Output Port (Ineffective at 0, duplicated
indication invalid)
114 OLWNO
Driver overload warning
output No.
0
0 ~ 6999
(Main application Ver. 1.51 or later)
* Contact b
456
Appendix
Axis-Specific Parameters
No.
Parameter name
Default value
(Reference)
s
k
r
a
m
e
R
ti
n
U
e
g
n
a
r
t
u
p
n
I
116 (For extension)
0
~
117 PIG
0
Reference only
For adjustment by the manufacturer
118 PDG
0
Reference only
For adjustment by the manufacturer
119 PFSG
50,
50,
50,
50,
0,
0
0 ~ 100
* Change is prohibited unless instructed by the
manufacturer.
120 PFF
10
0 ~ 100
* Change is prohibited unless instructed by the
manufacturer.
121~
130
(For extension)
0
~
115
OUTDT: OLLV
0
0H ~
FFFFFFFFH
<Caution>
• The recommended output port is the fieldbus
domain.
• Confirm the fieldbus type and assign to the
domain that can ensure the simultaneity (identity)
for the specified number of bits.
* There may be a case that the simultaneity
(identity) of the data cannot be ensured
depending on the fieldbus type such as the
domain setting that exceeds the 32-bit boundary.
• When connecting to a master device available for
data simultaneity (identity) setting, make sure to
establish the setting to ensure the data
simultaneity (identity).
Bits 00 to 15: NOPIO (output port No. MIN,
BCD 4 digits input)
Bits 16 to 19: BYTPIO (number of output bites,
BCD 1 digit input)
(1: 1byte (8bits) 2: 2bytes (16bits)
4: 4bytes (32bits))
Data output setting:
Overload lebel monitor (%)
Bits 20 to 23: FPIO (format (bite order), BCD 1
digit input)
(0: Big Endian (1234ABCDh
→12h|34h|ABh|CDh, ABCDh
→ABh|CDh)
1: Middle Endian 1 (1234ABCDh
→34h|12h|CDh|ABh)
2: Middle Endian 2 (1234ABCDh
→ABh|CDh|12h|34h)
3: Little Endian (1234ABCDh
→CDh|ABh|34h|12h,
ABCDh→CDh|ABh))
Bits 24 to 27: TYPDT (output data classification,
BCD 1 digit input)
(0: Invalid (no update (no operation))
1: Test Data (Output 1234ABCDh
/ABCDh/CDh after applying FPIO)
2: OLLV (overload level monitor (%),
binary output)
* To prevent motor burnout, the
startup initial temperature is
assumed high considering the
hot start for the controller load
ratio calculation (Safety side).
Therefore, the specification is
established to output 0 for the
specific period of time after the
startup in order of wrong
identification prevention when
using the overload level monitor
output in purpose of malfunction
foresight monitoring.
On the monitoring system side,
treat the amount as a valid
value after detecting an overload
level monitor output value other
than 0 after the controller startup.
Bits 28 to 31: future expansion
(Main application Ver. 1.51 or later)
458
Summary of Contents for X-SEL PX
Page 1: ...Operation ManualSeventh Edition X SEL Controller PX QX Type Tenth Edition ...
Page 2: ......
Page 8: ......
Page 14: ......
Page 410: ...383 Appendix 386 ...
Page 452: ...425 Appendix 5 428 ...
Page 559: ......