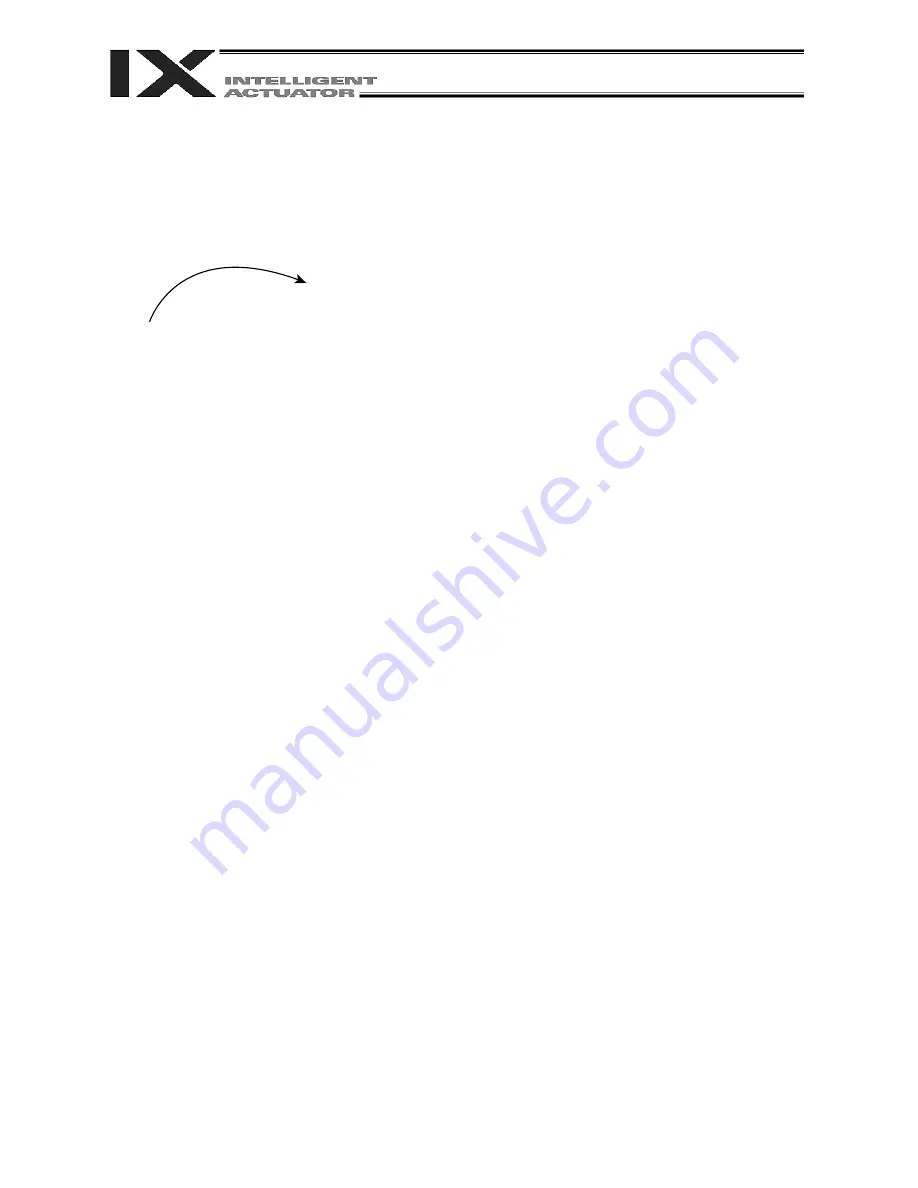
325
Part 4 Commands
(3) Notes on CP operation
The singular point refers to a position where arms 1 and 2 form a straight line.
Performing CP operation along a path near the singular point may reduce locus accuracy, cause
vibration (noise) or generate errors. The errors that may occur include the following:
"D09: Driver overspeed error," "B91: Main overspeed error," "C64: Invalid servo
acceleration/deceleration error," "B74: CP-operation restriction zone entry error," and "C6B:
Deviation overflow error"
These problems may be prevented by lowering the speed or acceleration/deceleration.
The CP-operation restriction zone is defined
as the area between the singular point locus
and the locus of the value set in all-axis
parameter No. 50. CP operation is prohibited
inside this area. (In the figure shown at left, the
area between the solid line and dotted line is
the CP-operation restriction zone.)
The controller will generate an error upon
detecting that the target locus used in locus
calculation or the actual movement locus has
entered the CP-operation restriction zone. If
the target movement locus has entered the
CP-operation restriction zone during locus
calculation, a "B7C: Error due to target locus
inside CP-operation restriction zone
(PTP/jogging of each axis enabled)" will
generate.
When the actual movement locus has entered the CP-operation restriction zone, a "B74: CP-
operation restriction zone entry error (PTP/jogging of each axis enabled)" or "C74: Actual-position
soft limit over error" will generate.
The width of the CP-operation restriction zone (distance between the solid line and dotted line) will
vary depending on the robot arm length. (If the arm length is 500/600, the restriction zone will
become approx. 0.5 mm wide (All-axis parameter No. 50: Width of CP-operation restriction zone
near arm 1/2 straight-line point)).
Avoid creating a program that will cause the axes to pass the CP-operation restriction zone during CP
operation.
Once inside, the axes cannot be pulled out of the CP-operation restriction zone via CP operation.
Move the axes via PTP operation. Exercise caution when the arm condition is not recognized at the
start of program, etc.
As for CP operation, always perform test operation at low speed and confirm absence of problem
beforehand. Then, gradually raise the speed to an appropriate level.
All-axis parameter
No. 50
CP-operation
restriction zone
326
Part 4 Commands
1.2 PTP Operation
(1) Movement locus
The axes move to the target position at the specified speed. The locus of axis tip during movement
cannot be specified using commands.
Example)
MOVP 1
Move from the current position to position No. 1 via PTP
operation.
The arm system may change during movement depending on the operation area or upon execution
of an arm-system control command.
PTP operation commands: MOVP, MVPI, TMPI, PACH, PMVP, ARCH
For details on these commands, refer to Chapter 2, "Explanation of Commands."
(2) Speed and acceleration/deceleration settings for PTP operation
The speed and acceleration/deceleration for PTP operation are predefined in a program using
control declaration commands.
Speed setting command "VELS"; unit [% (ratio to the value set in “Axis-specific parameter No. 28:
Maximum PTP speed (SCARA axis)”)]
Acceleration setting command "ACCS"; unit [% (ratio to the value set in “Axis-specific parameter No.
134: Maximum PTP acceleration (SCARA axis)”)]
Deceleration setting command "DCLS"; unit [% (ratio to the value set in “Axis-specific parameter No.
135: Maximum PTP deceleration (SCARA axis)”)]
Example)
ACCS
50
Set the acceleration for PTP operation to 50% of the maximum PTP
acceleration.
DCLS
50
Set the deceleration for PTP operation to 50% of the maximum PTP
deceleration.
VELS 50 Set the speed for PTP operation to 50% of the maximum PTP speed.
MOVP
2
Move to position No. 2 via PTP operation.
(3) Notes on PTP operation
The arm system may change during movement depending on the operation area or upon execution
of an arm-system control command.
Refer to 2, "Arm System," on the following page.
Position No. 1
329
Summary of Contents for X-SEL PX
Page 1: ...Operation ManualSeventh Edition X SEL Controller PX QX Type Tenth Edition ...
Page 2: ......
Page 8: ......
Page 14: ......
Page 410: ...383 Appendix 386 ...
Page 452: ...425 Appendix 5 428 ...
Page 559: ......