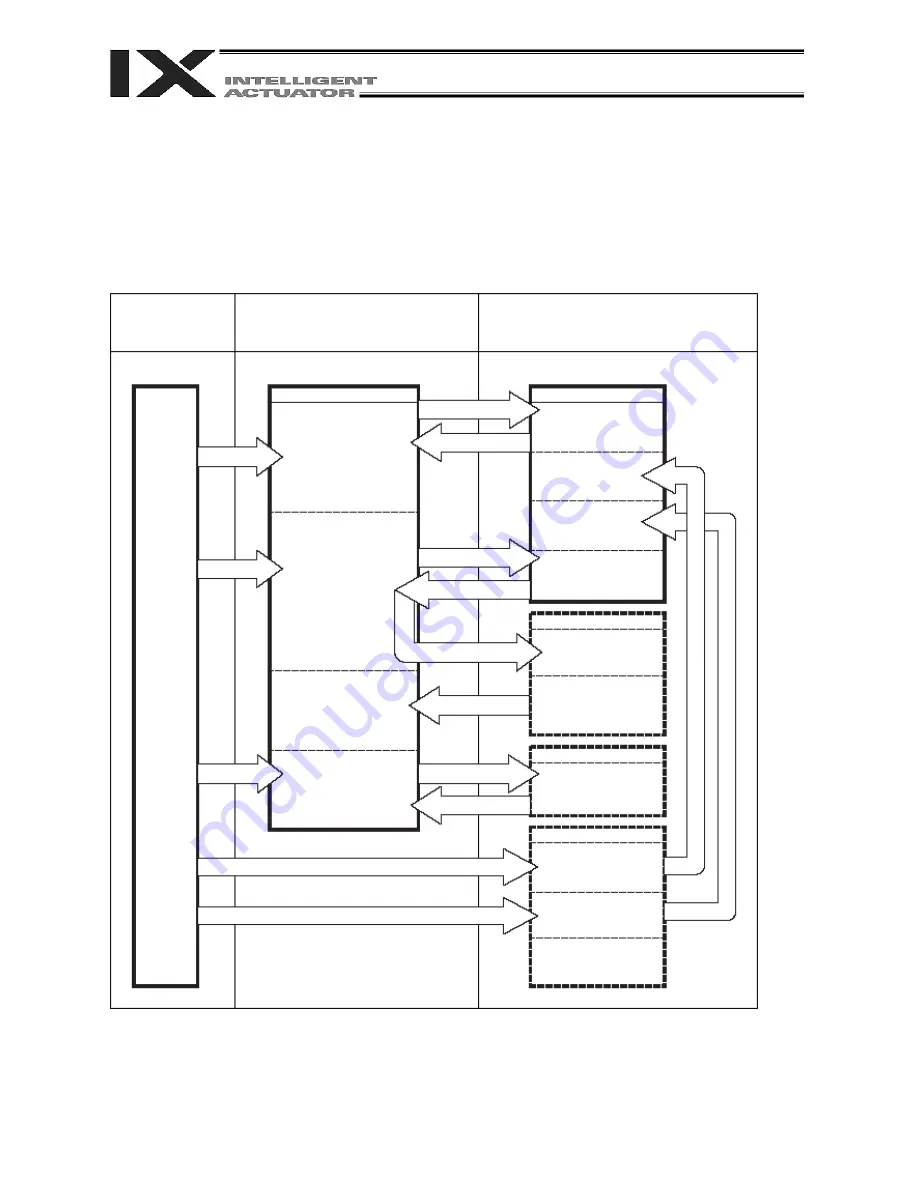
107
Part 3 Controller Data Structure
Chapter 1 How to Save Data
Since the X-SEL controller uses flash memory, some data are saved by battery backup while others are
saved in the flash memory.
When data is transferred from the PC software or teaching pendant to the controller, the data is only
written to the main CPU memory as shown in the diagram below and will be erased once the controller is
powered down or reset.
For important data, always write to the flash memory so that they will not be lost.
1. Factory Settings: When the System Memory Backup Battery is Used
1.1 Controller without Increased Memory Size
(Other parameter No. 20 = 2 (System-memory backup battery installed))
Data edited on the PC
or teaching pendant
Data will be retained while
the power is on and cleared
upon reset
Data will be retained even after the
power is turned off
PC
software,
TP
Transfer
Transfer
Transfer
Main CPU memory
Programs
Parameters (other than
slave parameters)
Symbols
Slave card parameters
(driver card
parameters)
Slave card parameters
(encoder parameters)
Write to flash memory
Write to flash memory
Transfer upon reset
Transfer upon reset
Transfer upon reset
Transfer upon reset
Transfer upon reset
Transfer
Transfer
Main CPU flash memory
Slave card memory
Slave card memory
Slave card parameters
(driver card parameters and
power system parameters
that are fixed (cannot be
changed))
Battery backup memory
Positions
Coordinate system
data
SEL global data (flags,
variables, strings)
Error lists
Write
to
flash
memory
108
Part 3 Controller Data Structure
Since the programs, parameters and symbols are read from the flash memory at restart, the data in the
temporary memory will remain the same as the original data before edit unless the edited data are written
to the flash memory.
The controller always operates in accordance with the data in the main CPU memory (excluding the
parameters).
1.2 Controller with Increased Memory Size (with Gateway Function)
(Other parameter No. 20 = 2 (System-memory backup battery installed))
The programs, parameters, symbols and positions are read from the flash memory at restart. The data in
the main CPU memory will remain the same as the original data before edit unless the edited data are
written to the flash memory. The controller always operates in accordance with the data in the main CPU
memory (excluding the parameters).
Data edited on the
PC or teaching
pendant
Data will be retained while the power is
on and cleared upon reset
Data will be retained even after the power is
turned off
PC
software,
TP
Transfer
Transfer
Transfer
Main CPU RAM memory
Programs
Parameters (other than
slave parameters)
Symbols
Positions (X-SEL axis)
(No.10001~20000)
Slave card
parameters
(Variable driver
parameters)
Slave card parameters
(Encoder parameters,
etc.)
Write to flash memory
Write to flash memory
Transfer upon reset
Transfer upon reset
Transfer upon reset
Transfer upon reset
Transfer upon reset
Transfer
Transfer
Main CPU flash memory
Slave card memory
Slave card memory
Battery backup memory
SEL global data (flags,
variables, strings)
Error lists
Write
to
flash
memory
Transfer
Write
to
flash
memory
Slave card parameters
(Fixed driver parameters
and power-supply
parameters)
(Cannot be changed)
Positions (X-SEL axis)
(Nos. 1 to 10000)
Coordinate system data
User-data backup
memory
(Positions (RC axis))
111
Summary of Contents for X-SEL PX
Page 1: ...Operation ManualSeventh Edition X SEL Controller PX QX Type Tenth Edition ...
Page 2: ......
Page 8: ......
Page 14: ......
Page 410: ...383 Appendix 386 ...
Page 452: ...425 Appendix 5 428 ...
Page 559: ......