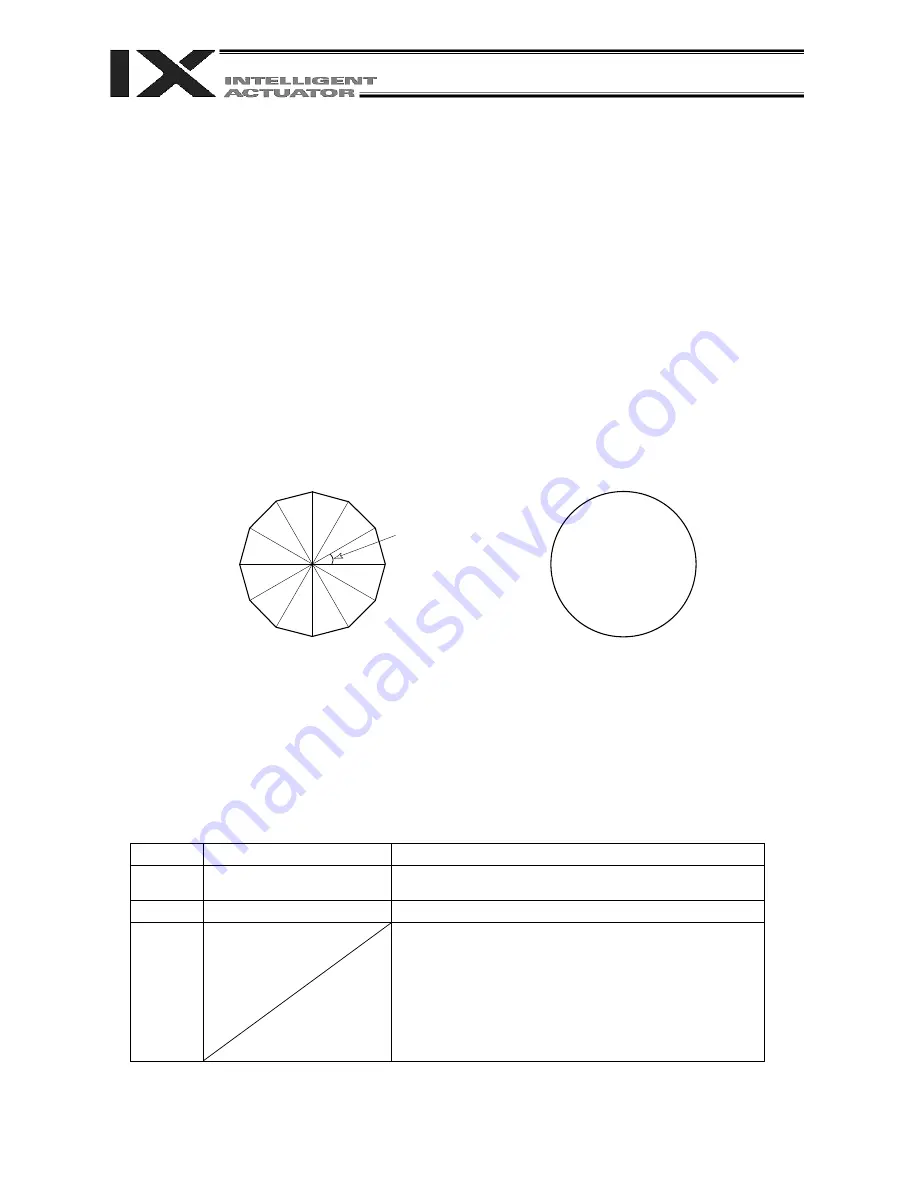
357
Part 4 Commands
[Example 3]
If an input condition is specified, the output will turn ON upon completion of operation in
the step before the one in which the input condition is specified.
Output field
Timing
POTP
1
308
Turn ON as P1 approaches.
309
Turn ON as P2 approaches.
310
Turn ON when P3 operation is
complete.
311
Turn ON as P11 approaches.
PATH
1 3 308
312
Turn ON as P21 approaches.
20
ARC2 10
11
311
313
Turn ON as P22 approaches.
PATH
21 23 312
314
Turn ON when P23 operation is
complete.
[4] When executing continuous movement commands sequentially, the controller is calculating
approx. 100 positions ahead. This is why the steps are displayed continuously on the PC screen
or teaching-pendant screen, regardless of the actual operation. The last step in the continuous
operation section executed by continuous movement commands will wait for the applicable
operation to complete.
PATH
1 5 Actuator
operation
ARC
6 7
PATH
8
12
Step displayed on the PC software or teaching pendant
BTON
310
[5] Do not allow the output fields to duplicate in the continuous operation section executed by
continuous movement commands.
Duplicating output fields in the continuous operation section will not achieve the expected result.
The output field will turn OFF at the start of processing of each command.
POTP 1
Do not let outputs 305 through 308 to duplicate, as in
the example shown at left.
PATH
1 5 305
Continuous operation section executed by continuous
movement commands
PATH
11 15 304
The final output status of duplicate 305 through 308 is indeterminable, because it is affected by
the positioning calculation time and the relationship of durations of actual operations.
Do not create a program containing an indefinite loop of continuous movement commands using
the TAG-GOTO syntax. (It will result in an accumulation of coordinate conversion errors.)
358
Part 4 Commands
2. PATH/PSPL Commands
When executing a PATH or PSPL command, pay attention to the locus because it will change if the
acceleration/deceleration is different between points.
The locus can be fine-tuned by changing the acceleration/deceleration, but different
acceleration/deceleration settings between points will prevent smooth transition of speeds when
moving from one position to another.
If there is a large difference in deceleration/acceleration between points and the positioning distance
is small, the speed may drop. Exercise caution.
3. CIR/ARC Commands
The processing by a CIR or ARC command resembles moving along a polygon with a PATH
command.
A small division angle may cause the speed to drop.
CIR2, ARC2, ARCD and ARCC commands actually perform arc interpolation.
This command is valid only on the XY plane.
4. CIR2/ARC2/ARCD/ARCC Commands
With a CIR2, ARC2, ARCD or ARCC command, the speed can be changed (only in the arc
interpolation section) by inputting a speed for the point specified in operand 1. These commands are
effective when you must lower the speed partially because the radius is small and the arc locus
cannot be maintained inside the allowable range.
The speed and acceleration will take valid values based on the following priorities:
Priority
Speed
Acceleration (deceleration)
1
Setting in the position data
specified in operand 1
Setting in the position data specified in operand 1
2
Setting by VEL command Setting by ACC (DCL) command
3
All-axis parameter No. 11, Default CP acceleration of
SCARA axis
(All-axis parameter No. 12, Default CP deceleration of
SCARA axis)
All-axis parameter No. 200, Default acceleration of
linear movement axis
(All-axis parameter No. 201, Default deceleration of
linear movement axis)
This command is valid only on the XY plane.
Division angle set by
a DEG command
CIR CIR2
361
Summary of Contents for X-SEL PX
Page 1: ...Operation ManualSeventh Edition X SEL Controller PX QX Type Tenth Edition ...
Page 2: ......
Page 8: ......
Page 14: ......
Page 410: ...383 Appendix 386 ...
Page 452: ...425 Appendix 5 428 ...
Page 559: ......